-
- News
- Books
Featured Books
- pcb007 Magazine
Latest Issues
Current IssueInventing the Future with SEL
Two years after launching its state-of-the-art PCB facility, SEL shares lessons in vision, execution, and innovation, plus insights from industry icons and technology leaders shaping the future of PCB fabrication.
Sales: From Pitch to PO
From the first cold call to finally receiving that first purchase order, the July PCB007 Magazine breaks down some critical parts of the sales stack. To up your sales game, read on!
The Hole Truth: Via Integrity in an HDI World
From the drilled hole to registration across multiple sequential lamination cycles, to the quality of your copper plating, via reliability in an HDI world is becoming an ever-greater challenge. This month we look at “The Hole Truth,” from creating the “perfect” via to how you can assure via quality and reliability, the first time, every time.
- Articles
- Columns
- Links
- Media kit
||| MENU - pcb007 Magazine
Estimated reading time: 4 minutes
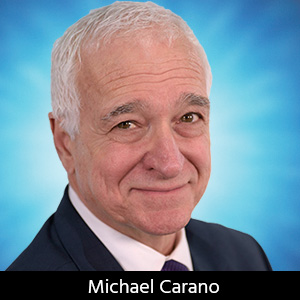
Contact Columnist Form
Trouble in Your Tank: A Process Engineer’s Guide to Surface Prep and Dry-Film Photoresist Adhesion
Introduction
One cannot underestimate the importance of surface preparation of the copper surface and its relationship to dry film adhesion. Further, the quality and dimensions of the circuit as it was designed depend heavily on the surface preparation of the copper foil. Certainly, we have witnessed a step-change in technology that has necessitated a total rethinking of how copper surfaces are cleaned and prepared to enhance photoresist adhesion.
Several of these changes are driven by cost pressures leading to substrate construction. The need to handle thin core materials, as well as lower copper foil thicknesses, is driving the move to alternative surface preparation techniques. And while many of these techniques are well-established, the drive to 5G, higher frequency transmission, and automotive changes—including crash avoidance and autonomous driving—higher-density designs with sub-three-mil lines and spaces are becoming the order of the day.
Thus, the first order of business is to prepare the surface for resist adhesion while reducing the amount of copper removal. In addition, designers prefer lower profile copper to effect improved signal integrity. In this context, low profile refers to the smoother, more uniform topography of the copper foil side facing the prepreg.
All this leads to increased emphasis on the adhesion of the photoresist to the copper substrate. Further, thinner core materials are prone to distortion and cold-working with mechanical surface preparation methods. Cold-working a metal can lead to the creation of internal stress, which then is the cause of copper foil cracking. For this reason, chemical cleaning methods are favored over mechanical methods, as long as copper removal rates are reduced and excessive surface roughness is avoided.
Getting to Optimum Resist Adhesion
Let’s review the task at hand. The objectives are simple. First, a clean, virgin copper surface is the first step to ensuring optimum adhesion. In addition, some surface restructuring is needed to provide anchoring points for the resist.
The ideal surface should include:
- Oxide-free
- Moisture-free (moisture causes resist to flow into holes, leading to lock-in)
- No pumice residues
- No fingerprints
- Complete chromate removal
- High surface area but somewhat uniform
- Water break test (holds film in water for 20–25 seconds)
Figure 1 shows an example of fingerprints, and Figure 2 demonstrates severe oxidation. The oxidation can be blamed on allowing moisture to remain on the boards without proper drying, or a heated dry was too hot. Oxidation leads to resist lock-in, making developing, resist stripping, and final etching problematic. Fingerprints are simply caused by poor handling procedures.
Keep in mind that rinsing after chemical processing steps is as important as the chemical processes themselves. Using counter-flow rinses and maintaining the cleanliness of the rinse water will minimize ionic contaminants from negatively impacting resist adhesion.
As stated earlier, oxidation will lead to resist lock-in. Fingerprints will prevent uniform adhesion of the film and will negatively impact surface preparation and final etching (Figure 3). The improper cleaning of panels, resulting in residues (i.e., fingerprints) remaining on the panel surface after precleaning before resist application, leads to the issue seen in Figure 3. Improper handling is also a potential root cause.
Figure 3: Example of oily fingerprint preventing complete etching of the copper. (Source: RBP Chemical Technology)
One should understand that copper foil producers apply an anti-tarnish coating (generally a chromate-based conversion coating). This helps maintain that cosmetic copper color. However, as the first step in surface preparation for inner layer processing, the chromate must be removed from the surface. Chromate thicknesses are somewhat non-uniform in practice. Regardless, before micro-etching the copper surface, it is highly recommended that the chromate be completely removed. This is accomplished with a mixture of strong mineral acids. It is recommended that a formulated acidic cleaner with some solvation properties (surfactants, solvents) be used to remove organic residues.
Proper surface cleaning before micro-etching or pumice treatment will minimize issues where the soils prevent uniform micro-roughening of the copper surface. My key point is chemical micro-etching, and pumice type treatments work best when the surface copper is free of organic soils and inorganic materials such as chromate coatings. The copper surface then is better able to obtain an acceptable surface roughness that will enhance resist adhesion.
Failure to completely remove soils prior to pumice or chemical micro-etching will only prevent the uniformity of the surface roughening process. Think of this as a surface where there are spots where there is very little, if any, roughening and where there could be areas of extreme roughness. This is not an optimum situation.
In addition, failure to remove chromates and other soils effectively will lead to what we call differential etching. Essentially, this means that during the surface roughening step (after chromate and soil removal), by employing a micro-etch formulation, the roughening will be less than optimal due to incomplete chromate and other soil removal. This negatively impacts the adhesion of resists. Understandably, in those areas where organic soils and chromates remain, the micro-etchant will have compromised ability to provide a uniformly structured surface.
Next Time
In a future column, I will explore the relationship between resist lamination parameters, developing, and etching.
This column originally appeared in the October 2020 issue of PCB007 Magazine.
More Columns from Trouble in Your Tank
Trouble in Your Tank: Metallizing Flexible Circuit Materials—Mitigating Deposit StressTrouble in Your Tank: Can You Drill the Perfect Hole?
Trouble in Your Tank: Yield Improvement and Reliability
Trouble in Your Tank: Causes of Plating Voids, Pre-electroless Copper
Trouble in Your Tank: Organic Addition Agents in Electrolytic Copper Plating
Trouble in Your Tank: Interconnect Defect—The Three Degrees of Separation
Trouble in Your Tank: Things You Can Do for Better Wet Process Control
Trouble in Your Tank: Processes to Support IC Substrates and Advanced Packaging, Part 5