Samsung, VeriSilicon Support Blaize AI Platform
October 28, 2020 | BlaizeEstimated reading time: 4 minutes
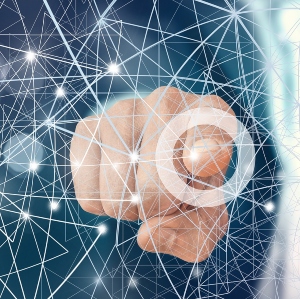
Samsung Electronics Co., Ltd., a world leader in advanced semiconductor technology, in collaboration with design services provider, VeriSilicon, has successfully supported the on-time market launch of AI Edge computing startup Blaize’s hardware platform, despite the COVID-19 pandemic.
Leveraging Samsung Foundry’s 14nm FinFET process technology and VeriSilicon’s chip design expertise and IP, Blaize is now offering its AI Edge computing Pathfinder and Xplorer platforms equipped with the Blaize Graph Streaming Processor (GSP), bringing a new class of powerful AI compute capabilities to edge applications such as industrial, smart city, automotive sensor fusion, last mile delivery and retail.
Blaize, based in El Dorado Hills, Calif., is addressing a fundamental issue in Edge AI application deployment: existing solutions are either unable to handle the required computational load, or too costly and difficult to implement in products. At the heart of Blaize’s solution is a 100% programmable hardware platform that offers an unprecedented combination of low-latency AI processing, low energy demand, multi-sensor AI analytics, and an accompanying suite of software tools that greatly simplify and accelerate the AI development process.
“We built our architecture for Edge AI, rather than adapting it from designs developed for larger settings like data centers and Cloud applications,” explains Santiago Fernandez-Gomez, Blaize vice president of platform engineering. “Our customers are asking for solutions that are a fraction of the size, use much less power, and can be tailored to their specific market requirements.”
Blaize’s platform strategy implementation faced a critical challenge: quickly bringing a robust product to market. “For both technical and business reasons, our number one goal was to get into production and have products to sell, so we needed working GSP chips as soon as possible. That made a mature process node a top priority,” notes Fernandez-Gomez.
At the outset of Blaize’s engagement, Samsung Foundry assessed initial plans and goals for the GSP and recommended involving VeriSilicon, a one-stop source for custom silicon solutions and semiconductor IP, with an extensive track record including other AI-related projects.
“The Blaize GSP project is a perfect example of why Samsung Foundry has prioritized development of the Samsung Advanced Foundry Ecosystem (SAFE) partnership program, as we pursue our goal of delivering flawless execution,” states Hong Hao, senior vice president of Foundry Business at Samsung Electronics. “Providing well-integrated access to VeriSilicon’s design and IP expertise allows a young and innovative company like Blaize to leverage the full breadth and value of our leading process technologies in the most efficient way.”
“It is a compelling chip design, and the Blaize team has a very good technical background and competence in collaborating across multiple sites,” recalls Dr. Mahadev Kolluru, VeriSilicon’s vice president for North America platform solutions sales. An early order of business was selecting the optimal manufacturing process node; after evaluation of many options, Samsung Foundry’s 14nm FinFET process emerged as the ideal choice for this product.
“When we considered the target applications for the initial chip, and the fact that much of the required IP at the time was not yet available in more advanced nodes, the mature node made sense,” says Dr.
Kolluru. “Cost is always a concern for everyone. And given our experience working with Samsung on this process over the years, we were confident it was the best path to first-time silicon success.”
“In those initial few months, the Samsung Foundry team worked hand-in-hand with VeriSilicon, going through every possible design method that would give us the combination of performance and power consumption we required,” recalls Fernandez-Gomez. “The Samsung foundry brought solutions to the table beyond the standard flows that allowed us to fully meet out targets.”
Another key factor was effective supply chain planning. Despite the Covid-19 pandemic and global materials supply shortage, VeriSilicon was able to reserve production capacity not only with Samsung foundry but also with packaging, assembly, and test contractors.
The process rolled forward smoothly through 2019 and into 2020, with teams across locations working together in seamless fashion to address design challenges like system timing and integration of complex machine-learning IP blocks with the graphic-processing elements of the chip. VeriSilicon also provided a verification platform that allowed Blaize to begin developing drivers for the hardware platform. All systems were ready for scheduled tape-out in February when the global COVID-19 forced the lockdown of companies worldwide. VeriSilicon had to close offices 2 weeks before tape-out, but quickly adapted to working remotely along with the Blaize teams who were also transitioning to working remote, to deliver on the original target date.
Even better, when first silicon arrived, the samples were good enough to go directly into production. “In my experience,” adds Fernandez-Gomez, “it can often take six to nine months to go from first silicon to customer samples, and 12 to 18 months to a full production run. VeriSilicon delivered customer samples in two months and the silicon was pretty much perfect, and we will be in real production after six months.”
Samsung’s Hao calls the project “a success story that shows how a collaborative team effort can solve tough problems and meet ambitious goals. It is tremendously satisfying to work alongside people of the caliber found at Blaize and VeriSilicon, and to see so much knowledge and capability coming together in service of these exciting new Edge AI applications.”
Testimonial
"We’re proud to call I-Connect007 a trusted partner. Their innovative approach and industry insight made our podcast collaboration a success by connecting us with the right audience and delivering real results."
Julia McCaffrey - NCAB GroupSuggested Items
I-Connect007 Editor's Choice: Five Must-Reads for the Week
08/22/2025 | Andy Shaughnessy, I-Connect007In this week’s roundup, we have a variety of articles covering design, manufacturing, sustainability, and, of course, tariff negotiations. We have a milestone anniversary to celebrate as well, with Dan Beaulieu about to publish his 1,000th column. When does Dan even sleep? Here’s to hoping that we have 1,000 more weeks of "It’s Only Common Sense."
New Episode Drop: MKS’ ESI’s Role in Optimize the Interconnect
08/21/2025 | I-Connect007In this latest episode, Casey Kruger, director of product marketing at MKS’ ESI, joins On the Line With… host Nolan Johnson to share how CO₂ laser technology delivers faster, more accurate vias in a smaller, more energy-efficient footprint.
PEDC Call for Abstracts Deadline Extended to Aug. 31
08/20/2025 | I-Connect007 Editorial TeamThe second Pan-European Electronics Design Conference (PEDC) will take place Jan. 21-22, 2026, in Prague, Czech Republic. The call for abstracts deadline has been extended to Aug. 31. Organized jointly by the German Electronics Design and Manufacturing Association (FED) and the Global Electronics Association (formerly IPC), PEDC serves as a European platform for knowledge exchange, networking, and innovation in electronics design and development.
How Good Design Enables Sustainable PCBs
08/21/2025 | Gerry Partida, Summit InterconnectSustainability has become a key focus for PCB companies seeking to reduce waste, conserve energy, and optimize resources. While many discussions on sustainability center around materials or energy-efficient processes, PCB design is an often overlooked factor that lies at the heart of manufacturing. Good design practices, especially those based on established IPC standards, play a central role in enabling sustainable PCB production. By ensuring designs are manufacturable and reliable, engineers can significantly reduce the environmental impact of their products.
Meet the Round 1 Winners of the Bright Manufacturing Student Challenge 2025
08/20/2025 | Tara Dunn, SMTAThe Bright Manufacturing Student Challenge is an opportunity for student teams to design and develop innovative solutions for real-world electronics manufacturing problems. The eight-week competition, sponsored by the Electronics Manufacturing & Assembly Collaborative (EMAC) through electronicsworkforce.com, allows students to showcase their technical skills, creativity, and problem-solving abilities.