-
-
News
News Highlights
- Books
Featured Books
- pcb007 Magazine
Latest Issues
Current IssueThe Hole Truth: Via Integrity in an HDI World
From the drilled hole to registration across multiple sequential lamination cycles, to the quality of your copper plating, via reliability in an HDI world is becoming an ever-greater challenge. This month we look at “The Hole Truth,” from creating the “perfect” via to how you can assure via quality and reliability, the first time, every time.
In Pursuit of Perfection: Defect Reduction
For bare PCB board fabrication, defect reduction is a critical aspect of a company's bottom line profitability. In this issue, we examine how imaging, etching, and plating processes can provide information and insight into reducing defects and increasing yields.
Voices of the Industry
We take the pulse of the PCB industry by sharing insights from leading fabricators and suppliers in this month's issue. We've gathered their thoughts on the new U.S. administration, spending, the war in Ukraine, and their most pressing needs. It’s an eye-opening and enlightening look behind the curtain.
- Articles
- Columns
- Links
- Media kit
||| MENU - pcb007 Magazine
This Month in PCB007 Magazine: The Copper Foil Market Is Anything But Flat
November 18, 2020 | Nolan Johnson, PCB007Estimated reading time: 2 minutes
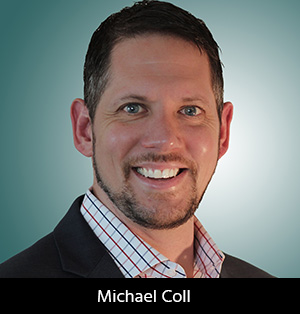
I interviewed Mike Coll, COO of Denkai America, about the copper foil and substrate market, the recent acquisition of the company by Nippon, and what they’re doing to respond to very small feature sizes.
Nolan Johnson: Mike, give us a quick introduction to your role.
Michael Coll: I’m the COO of Denkai America. We’re the United States’ only electrodeposit and copper foil manufacturer. We were recently acquired by Nippon Denkai (ND) from Japan. Nippon Denkai translates to “Japan Electroplating.” When they acquired us, we became Denkai America or “Electroplating America.”
Johnson: Where are your facilities located?
Coll: We are about 30 miles northeast of Columbia, South Carolina, and our parent, ND, is located about 50 miles northeast of Tokyo.
Johnson: Manufacturing copper foil in the U.S.: What are some of the particular challenges that you face?
Coll: We’ve been making copper foil in North America since 1976, and it was under the prior ownership of Mitsui Mining and Smelting, also known as Mitsui Kinzoku. In April this year, we were sold to ND. We’ve been operating under new ownership, without their presence, as this transition occurred just at the start of the COVID-19 pandemic. Needless to say, this is not ideal for our integration. As for ongoing manufacturing, when our facility was built in the early 2000s, our factory was set up to be a high-volume copper manufacturer for a limited set of products; at that time, our focus was the high-volume PCB industry in North America.
In the past 20 years, there have been significant changes in the PCB industry in North America. Consolidation and changing from high volume manufacturing to a quick turn, prototyping type of environment. Trying to continually retool an aging factory to meet the demands of the U.S. market is an extremely difficult proposition.
Johnson: That’s a particular challenge. One of the other dynamics that may play a part is the fact that there are so many more materials out there now. The materials and substrates market is booming with multiple simultaneous areas of growth, to respond, for example, to very small feature sizes, RF frequency requirements, speed issues, and extreme environment issues. Some of these requirements complement each other, but others conflict. You’re delivering foil to that market, and it has to be quite a diverse set of targets to try to hit.
Coll: It is, especially with all the changes in resin systems and material requirements. At one time, as long as your copper stuck to FR-4, that’s all that mattered. But with the wide variety of resin systems, copper foil needs to be more and more tailored to the specific user and specific application. Our initial manufacturing setup was for high-volume, “vanilla” copper foil. Now, with the vast number of resin systems and requirements from our customers, we need to adapt, change, and produce multiple different varieties of copper to meet those new and emerging applications.
To read this entire interview, which appeared in the November 2020 issue of PCB007 Magazine, click here.
Suggested Items
Trouble in Your Tank: Can You Drill the Perfect Hole?
07/07/2025 | Michael Carano -- Column: Trouble in Your TankIn the movie “Friday Night Lights,” the head football coach (played by Billy Bob Thornton) addresses his high school football team on a hot day in August in West Texas. He asks his players one question: “Can you be perfect?” That is an interesting question, in football and the printed circuit board fabrication world, where being perfect is somewhat elusive. When it comes to mechanical drilling and via formation, can you drill the perfect hole time after time?
The Evolution of Picosecond Laser Drilling
06/19/2025 | Marcy LaRont, PCB007 MagazineIs it hard to imagine a single laser pulse reduced not only from nanoseconds to picoseconds in its pulse duration, but even to femtoseconds? Well, buckle up because it seems we are there. In this interview, Dr. Stefan Rung, technical director of laser machines at Schmoll Maschinen GmbH, traces the technology trajectory of the laser drill from the CO2 laser to cutting-edge picosecond and hybrid laser drilling systems, highlighting the benefits and limitations of each method, and demonstrating how laser innovations are shaping the future of PCB fabrication.
Day 2: More Cutting-edge Insights at the EIPC Summer Conference
06/18/2025 | Pete Starkey, I-Connect007The European Institute for the PCB Community (EIPC) summer conference took place this year in Edinburgh, Scotland, June 3-4. This is the third of three articles on the conference. The other two cover Day 1’s sessions and the opening keynote speech. Below is a recap of the second day’s sessions.
Day 1: Cutting Edge Insights at the EIPC Summer Conference
06/17/2025 | Pete Starkey, I-Connect007The European Institute for the PCB Community (EIPC) Summer Conference took place this year in Edinburgh, Scotland, June 3-4. This is the second of three articles on the conference. The other two cover the keynote speeches and Day 2 of the technical conference. Below is a recap of the first day’s sessions.
Preventing Surface Prep Defects and Ensuring Reliability
06/10/2025 | Marcy LaRont, PCB007 MagazineIn printed circuit board (PCB) fabrication, surface preparation is a critical process that ensures strong adhesion, reliable plating, and long-term product performance. Without proper surface treatment, manufacturers may encounter defects such as delamination, poor solder mask adhesion, and plating failures. This article examines key surface preparation techniques, common defects resulting from improper processes, and real-world case studies that illustrate best practices.