Aismalibar, American Standard Circuits Confirm IST Thermal Testing of HTC 3.2w High Tg Multilayer Thermal Conductive Material
January 11, 2021 | AismalibarEstimated reading time: 3 minutes
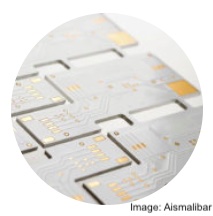
Aismalibar and American Standard Circuits confirm successful IST thermal testing of HTC 3.2w High Tg Multilayer Thermal Conductive Material.
In order to confirm that the Aismalibar High Tg (180 °C), thermal conductive (3.2 w/mc), multilayer material system would pass rigorous automotive thermal cycling testing, the proven IST thermal testing methodology was chosen. American Standard Circuits manufactured the thermal conductive multilayer test panels. PWB Interconnect Solutions Inc. performed the thermal cycling testing.
“We believe there is no better material on the market today than Aismalibar’s HTC 3.2w High Tg Multilayer Thermal conductive material. To demonstrate that, we passed it through very rigorous thermal cycling testing. The best part? Our trusted customer partners American Standard Circuits and PWB Interconnect Solutions Inc. were involved in the process,” said Aismalibar North America President Jeff Brandman when making the announcement.
The IST system automatically sequences a constant DC current through the designed PWB interconnect test coupon, providing the thermal cycling of the samples. The rise in temperature of the circuits is from 25°C to 150°C for reliability testing or an upper temperature of 230°C to 260°C for simulating assembly stress. Once the specified temperature has been achieved, the system turns off the current and cooling begins. After a 3-minute heating cycle, the coupons are forced air cooled for 2 minutes, which represents one cycle. The specified upper temperature for reliability testing is just below the glass transition temperature of the base material.
During each thermal excursion, the system continuously monitors the minute resistance changes in the PTH, blind, buried and micro-via or inner layer to barrel (post) interconnects. Due to the temperature of the interconnect cycles, the resistance values of the interconnect, traces, pads, and hole barrels will also change. The IST system is designed to measure resistance changes to signify when the PCB reaches the point of interconnect degradation or failure. Typical multilayers will survive between 200 to 500 thermal cycles. The Aismalibar High Tg, thermal conductive, multilayer material system survived the required 1000 cycles with no noticeable degradation. The first test coupons were stressed with 3 pre-condition cycles at 245°C and 300°C thermal cycles at 150°C. The 350-cycle testing passed with no degradation. To stress the coupons to the maximum, trying to force failures, a second more severe test called for 9 times preconditioning at 300°C. Capacitance readings were taken after 3, 6 and 9 pre-conditioning cycles to check for delamination. The coupons easily passed 1000 cycles, showing the superiority of the Aismalibar high HT 3.2 w/mc multilayer lamination system.
About Aismalibar (Copper Clad Laminates and Metal Clad Laminates for PCB)
Aismalibar has over sixty years of experience manufacturing high end copper and metal clad laminates for the printed circuit board industry. During the last two decades, Aismalibar has been focused on offering the best solutions to reduce the operational temperature of printed circuit boards.
For more information, visit www.aismalibar.com.
About American Standard Circuits
American Standard Circuits (ASC) prides itself on being a total solutions provider. They manufacture quality rigid, metal-backed, RF/microwave, flex, and rigid-flex PCBs for the medical, automotive, industrial, defense, and aerospace markets in volumes, from test and prototypes, to large production orders. ASC has expertise to provide a wide variety of technologies in a time-critical environment.
Their qualifications include AS9100 Rev D, ISO 9001:2015, MIL-PRF 31032, MIL-PRF-55110, MIL-PRF-50884 certification and ITAR registration. In addition to manufacturing in the USA, ASC can transition and manage your PCB requirements to lower cost regions via its qualified supply chain of offshore partners. ASC also holds many key patents for metal bonding processes. For more information about American Standard Circuits' services or to ask one of their technology experts a question, visit www.asc-i.com.
Visit I-007eBooks to download your copies of American Standard Circuits’ micro eBooks today:
The Printed Circuit Designer’s Guide to… Fundamentals of RF/ Microwave PCBs
The Printed Circuit Designer's Guide to... Flex and Rigid-Flex Fundamentals
The Printed Circuit Designer’s Guide to...Thermal Management: A Fabricator's Perspective
Testimonial
"In a year when every marketing dollar mattered, I chose to keep I-Connect007 in our 2025 plan. Their commitment to high-quality, insightful content aligns with Koh Young’s values and helps readers navigate a changing industry. "
Brent Fischthal - Koh YoungSuggested Items
Trouble in Your Tank: Minimizing Small-via Defects for High-reliability PCBs
08/27/2025 | Michael Carano -- Column: Trouble in Your TankTo quote the comedian Stephen Wright, “If at first you don’t succeed, then skydiving is not for you.” That can be the battle cry when you find that only small-diameter vias are exhibiting voids. Why are small holes more prone to voids than larger vias when processed through electroless copper? There are several reasons.
The Government Circuit: Navigating New Trade Headwinds and New Partnerships
08/25/2025 | Chris Mitchell -- Column: The Government CircuitAs global trade winds continue to howl, the electronics manufacturing industry finds itself at a critical juncture. After months of warnings, the U.S. Government has implemented a broad array of tariff increases, with fresh duties hitting copper-based products, semiconductors, and imports from many nations. On the positive side, tentative trade agreements with Europe, China, Japan, and other nations are providing at least some clarity and counterbalance.
How Good Design Enables Sustainable PCBs
08/21/2025 | Gerry Partida, Summit InterconnectSustainability has become a key focus for PCB companies seeking to reduce waste, conserve energy, and optimize resources. While many discussions on sustainability center around materials or energy-efficient processes, PCB design is an often overlooked factor that lies at the heart of manufacturing. Good design practices, especially those based on established IPC standards, play a central role in enabling sustainable PCB production. By ensuring designs are manufacturable and reliable, engineers can significantly reduce the environmental impact of their products.
50% Copper Tariffs, 100% Chip Uncertainty, and a Truce
08/19/2025 | Andy Shaughnessy, I-Connect007If you’re like me, tariffs were not on your radar screen until a few months ago, but now political rhetoric has turned to presidential action. Tariffs are front-page news with major developments coming directly from the Oval Office. These are not typical times. President Donald Trump campaigned on tariff reform, and he’s now busy revamping America’s tariff policy.
Global PCB Connections: Understanding the General Fabrication Process—A Designer’s Hidden Advantage
08/14/2025 | Markus Voeltz -- Column: Global PCB ConnectionsDesigners don’t need to become fabricators, but understanding the basics of PCB fabrication can save you time, money, and frustration. The more you understand what’s happening on the shop floor, the better you’ll be able to prevent downstream issues. As you move into more advanced designs like HDI, flex circuits, stacked vias, and embedded components, this foundational knowledge becomes even more critical. Remember: the fabricator is your partner.