-
- News
- Books
Featured Books
- pcb007 Magazine
Latest Issues
Current IssueInventing the Future with SEL
Two years after launching its state-of-the-art PCB facility, SEL shares lessons in vision, execution, and innovation, plus insights from industry icons and technology leaders shaping the future of PCB fabrication.
Sales: From Pitch to PO
From the first cold call to finally receiving that first purchase order, the July PCB007 Magazine breaks down some critical parts of the sales stack. To up your sales game, read on!
The Hole Truth: Via Integrity in an HDI World
From the drilled hole to registration across multiple sequential lamination cycles, to the quality of your copper plating, via reliability in an HDI world is becoming an ever-greater challenge. This month we look at “The Hole Truth,” from creating the “perfect” via to how you can assure via quality and reliability, the first time, every time.
- Articles
- Columns
- Links
- Media kit
||| MENU - pcb007 Magazine
Estimated reading time: 12 minutes
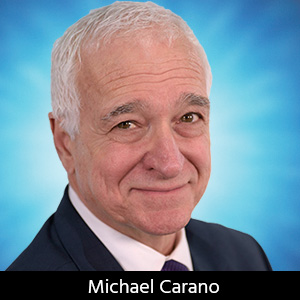
Contact Columnist Form
Trouble In Your Tank: Process Management and Control—Benchmarking Best Practices
Introduction
It is quite interesting and timely that the editorial staff of I-Connect007 has chosen the theme of benchmarking and process control/management for the February 2021 issue. This theme fits quite well with the global events of today. Moreover, this includes navigating through the global pandemic, adjusting to customer demand, and maintaining efficient operations regardless of the manufacturing business.
Having been involved in the printed circuit board, circuit board assembly, and semiconductor technology segments for the last 40 years, I have preached ad nauseum about minimizing defects and improving yields. This is especially true as the technology is becoming ever so complicated, and additional focus must be placed on yield improvements. This is where process management and control must be front and center.
Between a Rock and a Hard Place
This is what we see here today. There is an even larger chasm between quality (higher yields, less scrap, etc.) and productivity. “What happens to quality when there is a push to get more work out the door?” To further complicate matters, many fabricators tend to optimize their operation around cost rather than quality and yield. Thus, when optimizing around costs, quality and yields suffer, and the blame game begins.
Things go wrong (TGW). Stuff happens. But this is not the attitude to have when yields are headed south, and processes can indeed be out of control. It’s important to know what, exactly, is out of control. For example, is it the pH of the resist developer solution or the specific gravity of the alkaline etchant? Are these special causes or common causes? A special cause indicates that something in the related processes caused the change. In other words, there is an assignable cause. Where is the process control management plan and where was this listed?
What if there wasn’t a significant change and you don’t have a specific, assignable cause? There are multiple variations within the printed circuit board manufacturing process. That is a fact. Having a deep understanding of these possible variables and their ultimate effect on quality is the cornerstone of process control and management. This understanding becomes the basis for complex troubleshooting activities.
Approaches to Process Control
I strongly suggest that operators and engineers monitor all aspects of the processes for each unit operation. This includes walking the line, taking measurements, recognizing what is not in control (and getting it back within range). Quality and yields must come first—not pushing out production and cutting process costs! Indeed, SPC charts are often seen dotting the walls of the company’s laboratory, theoretically giving the impression that crucial unit operations within the manufacturing facility are in control. That is not always accurate. For example, several processes can be set up for automated analysis and replenishment of critical chemical additives. However, this often only covers the basic additives in the electroplating or electroless plating processes (copper concentration, acid levels, etc.). What about the organic additives (leveling agents, throwing power enhancers, stabilizers) that profoundly affect the overall quality and reliability of the plated deposit? How does one know with any confidence that these critical additives (special additives that influence ductility, grain structure, resistance to thermal excursions) are in the proper range?
The fabricator can rely somewhat on the chemical and material supplier for the analysis of key organic additives. In general terms, these critical additives are packaged so that they are replenished as the essential inorganic additives are added. Yet, TGW—there is potential for additive decomposition and the potential of over-adding these materials. This is precisely why different approaches to process control are needed. This means that additional analytical methods, coupled with quantitative measurements of rinse water cleanliness and temperature, are critical to success, along with the basics described above. In addition, operators should regularly inspect nozzles in various spray modules for wear and tear, then replace those nozzles as needed. Finally, methods to prevent the drag-in of harmful chemicals and enhanced filtration of all solutions are just several of the best practices that must be implemented.
Figure 1 shows the significant hole wall roughness. Analysis of this situation told the tale of too many hits from the drill bits. The fabricator looking to cut costs increased the hit rate from the recommended 2,000–2,500 hits to 4,500–5,000 hits, with deleterious consequences! Best practices were not being followed here. When best practice procedures were implemented—all drill bits were limited to 1,700–2,000 hits, resharpened once, and then discarded after another 1,500 hits—the drilled quality drastically improved, as did the subsequent plating quality (Figure 2).
Benchmarking Best Practices
The above example aside, let’s review what this author considers critical performance enhancers that often are not considered important by many fabricators. This is only a partial list, however, there are several deemed worthy of benchmarking and implementing best practices.
Rinsing
The PCB fabrication wet processes require good quality rinse water and best practice regarding proper rinsing design. Here again is the quest to reduce cost by cutting back on rinsing. This is not an ideal situation. Yes, it is a hard fact that processing printed circuit boards consumes large volumes of a precious resource. However, there are ways to remove contaminants from the printed circuit board and still conserve water.
At first thought, rinsing is often defined as removing process solutions from work, or in the case of the PCB industry, a panel. This is true, if not absolutely true. In general, rinsing is not the complete removal of the contaminants but rather a dilution of a process solution from work (panel) down to “manageable” concentrations. With this definition in mind, rinsing systems can be designed to minimize harmful contaminants on a printed circuit board and reduce water consumption. I’m often asked if some “standard” can be applied to the rinsing process. Are all types of contaminants the same? Is there a hard and fast rule for rinsing? The short answer is, not really. What constitutes a “manageable” concentration is dependent upon three conditions:
- The type of contaminant
- The tolerance of the following process step for the particular contaminant in question
- The effect the residual contaminants have on the work
The bottom line is to use tempered water rinses, along with sufficient dwell times required to remove the majority of these harmful contaminants. Counterflow rinses are particularly effective. When rinsing is ineffective (Figure 3), the stark reality of contaminant drag-in to subsequent process steps is certain.
Consider issues related to the electroless copper metallization process. Inadequate rinsing after the micro-etch step will lead to copper ion drag-in to the palladium-based catalyst. And it is well documented that high copper levels in this process will act as a catalytic poison, which then leads to the possibility of voids in the copper deposit.
Conductivity Probes
One of the least expensive things one can purchase for process control is a conductivity probe. This little unit (looks like a ballpoint pen) costs about $200. This is a great way to monitor the rinse water cleanliness and the rinsing operation’s overall effectiveness. The use of these probes is also an excellent method to measure contaminant build-up in certain chemical processes. An example of a conductivity probe is shown below (Figure 4).
CVS (Cyclic Voltametric Stripping)
While most fabricators rely on Hull cell plating analysis to gain some control of the additives in the electrolytic copper plating solutions, one must resort to a more quantifiable means to measure and control for today’s technology organic addition agents. Cyclic voltametric stripping is an electrochemical technique used for the measurement of organic additives in plating baths. It is based on the effect that the additives have on the rate of electroplating. Regardless of the specific type of organic additive (brightener, leveler, grain refiner, etc.), its activity is reflected in a change in the plating rate.
The analysis is performed in an electrochemical cell using a three-electrode system, one of which is a platinum rotating disk electrode. During measurement, the potential of the platinum electrode is controlled by the instrument. The potential is scanned at a constant rate back and forth between negative and positive voltage limits. A small amount of metal from the plating bath is alternatively plated onto and stripped off the working electrode as the potential is changed. During the scan, the current at the working electrode is measured as a function of potential.
The activity of the additive will affect the plating rate of the metal onto the electrode. The plating rate is determined by calculating the charge required to strip the metal of the working electrode. The relationship between the stripping charge and the additives’ activity is used to measure the additives and their components quantitatively.
A typical CVS scan for acid copper analysis may proceed from 1.5V to -0.225V and back again to 1.5V (Figure 5). During this potential sweep, the copper metal will be plated onto the platinum electrode and then again stripped off. The area of the curve under the stripping peak is measured in millicoulombs (mC). Each scan is performed equivalently, and multiple scans are committed to both condition the disk and allow for averaging the results from each potential sweep.
CVS analysis is used to measure the organic addition agents’ concentration present in the copper plating solution. This method is adaptable to quantifying both suppressors and the grain refiner/brightener in the working solution. This allows the fabricator to make required additions of critical components properly without the risk of over-adding or allowing the key components in the plating solution to fall out of balance.
Filtration
The need for filtration cannot be overemphasized, mainly when plating in through-holes and blind vias. Any void in the plating in the hole caused by small contaminants causes a reduction in the area available to carry the electric current. Rejects would also be caused when insoluble debris is co-deposited on the surface of the hole.
Flow rates are the only means of carrying solids to a filter or bringing a new solution into contact with the particulate matter. The flow rate is referred to as the turnover—total gallons pumped per hour concerning the size of the tank (for example, 200 gal/h on a 100-gallon tank is two turnovers per hour). Dirt-holding capacity is essential and can be attained with throw-away paper cartridges of different porosities, or filter surfaces coated with filter aid. Porosities of 100 microns down to less than 1 micron are typical. In practice, the average plating solution is turned over once per hour. The recommended flow rates should provide at least two complete tank volume turnovers per hour. However, to achieve the ultimate clarity, turnovers of up to 10 times per hour may be necessary. Keep in mind that the initial flow rate is not the average flow rate. In other words, if one started at 1000 gal/h, and cleaned or replaced the filter when the flow was reduced to 200 gal/h, the actual average flow would probably be about 600 gal/h, depending upon the type of filter media used.
Ineffective filtration leaves debris in the rinse and process tanks (Figure 6).
Temperature Control
All too often, while process engineers and technicians focus on wet analysis, the operating temperature checks often go overlooked. Rinsing and developing are typical processes that are more effective with tempered rinses. All too often, when rinsing uses incoming water (during the winter months in very cold climates), the water temperature is quite cold unless heaters are in place.
An increase of 10?K at temperatures not far from room temperature will increase the reaction rate by a factor of 2 to 3 (see chart below).
?F ?C ?K Rate Increase
72 22 295 --
90 32 305 2-3X (200-300%)
108 42 315 1 ½X (150%)
126 52 325 1X (100%)
At some point, the reaction rate increase starts to level off. What’s the point to this? The temperature has a significant influence on chemical reactions and rinsing.
Solution Agitation
Proper agitation and solution movement improves the efficiency of rinsing as well as improves plating distribution and uniformity. For best practices, the following rules apply:
Mechanical agitation for PTH processing:
1. Baskets/Racks
- Should be ridged to withstand the vibration energy
- Needs to hold the panels tightly so they don’t move
- < 0.059” @ 0.5”
- 0.060-0.125” @ 0.5-1.0”
- 0.125-0.250 “@ 1-2”
- >0.250” @ 2”
- 2- to 4-inch stroke on center
- 14-16 revolutions/minute
For Electroplating Processes:
This will depend on the electrolyte. Electrolytic copper responds very well to eductor-type agitation. Eductor agitation is based on the Venturi Principle, whereby one volume is pumped, and up to four volumes are drawn-in by the pressure drop, making it a highly efficient jetting system. When fully submerged, no air is introduced into the plating solution. Several manufacturers market eductors. Eductor agitation overcomes several of the disadvantages associated with air agitation. Air bubbles and misting are eliminated. In addition, eductor agitation provides a more uniform mixing of the plating solution. This minimizes potential “dead spots” in the cell where the air agitation is lacking. It is well known that educators provide more uniform agitation, better known as laminar flow.
In contrast, air agitation provides turbulent flow and may only promote the mixing of the solution. For quality plating results, it is preferable to have interface agitation. That is, one interface agitation is directed more at the cathode diffusion layer. This reduces the diffusion layer thickness, thus permitting the efficient delivery of additives and ions to the cathode surface.
Concerning tin plating solutions (etch resist), metal deposit uniformity is critical. This is especially critical on the pads and the knee of the via. Thin deposits often occur in these areas on the circuit board. As a consequence of thin plating, the etching process’s opportunity to cut through the tin is easily realized. This then may lead to the etching of the plated copper.
This issue is mitigated with best practice agitation. While air and eductor agitation are contraindicated for electrolytic tin plating, mechanical agitation is a must. Tin plating best practice is to set up through-hole mechanical agitation. This action ensures optimal delivery of process chemistry to the surface of the board and through the vias.
Summary
Certainly, most operators and engineers worry about controlling the wet chemistry of the printed circuit board fabrication’s various processes. Yet, they are often surprised and disappointed that the finished product’s quality is not meeting stringent requirements and key workmanship standards. Further examination will find that other aspects of the process often overlooked were not controlled and maintained. Thus, it only makes sense that in addition to wet chemistry, other non-chemical factors be monitored and controlled. These include rinsing, filtration, agitation, and temperature controls. Ignore these best practices at one’s peril.
This column originally appeared in the February 2021 issue of PCB007 Magazine.
More Columns from Trouble in Your Tank
Trouble in Your Tank: Metallizing Flexible Circuit Materials—Mitigating Deposit StressTrouble in Your Tank: Can You Drill the Perfect Hole?
Trouble in Your Tank: Yield Improvement and Reliability
Trouble in Your Tank: Causes of Plating Voids, Pre-electroless Copper
Trouble in Your Tank: Organic Addition Agents in Electrolytic Copper Plating
Trouble in Your Tank: Interconnect Defect—The Three Degrees of Separation
Trouble in Your Tank: Things You Can Do for Better Wet Process Control
Trouble in Your Tank: Processes to Support IC Substrates and Advanced Packaging, Part 5