-
-
News
News Highlights
- Books
Featured Books
- pcb007 Magazine
Latest Issues
Current IssueThe Hole Truth: Via Integrity in an HDI World
From the drilled hole to registration across multiple sequential lamination cycles, to the quality of your copper plating, via reliability in an HDI world is becoming an ever-greater challenge. This month we look at “The Hole Truth,” from creating the “perfect” via to how you can assure via quality and reliability, the first time, every time.
In Pursuit of Perfection: Defect Reduction
For bare PCB board fabrication, defect reduction is a critical aspect of a company's bottom line profitability. In this issue, we examine how imaging, etching, and plating processes can provide information and insight into reducing defects and increasing yields.
Voices of the Industry
We take the pulse of the PCB industry by sharing insights from leading fabricators and suppliers in this month's issue. We've gathered their thoughts on the new U.S. administration, spending, the war in Ukraine, and their most pressing needs. It’s an eye-opening and enlightening look behind the curtain.
- Articles
- Columns
- Links
- Media kit
||| MENU - pcb007 Magazine
Quality and Continuous Improvement
February 24, 2021 | Patrick Valentine, UYEMURA USAEstimated reading time: 2 minutes
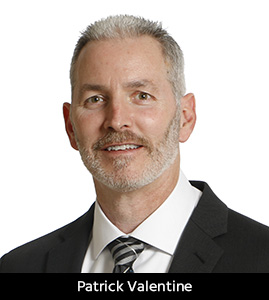
Introduction
Quality and continuous improvement are an integral part of the electronics industry. Poor quality is costly. Remediation costs of poor quality can cost a company 25% of its annual sales. Poor quality and the need for high reliability are the catalysts driving continuous improvement today. An in-depth review of quality and continuous improvement is presented.
The History of Quality
The concern for quality control and reduced product variation can be traced back centuries. Archaic quality control methods were used by the Xia Dynasty in 2100 BC in ancient China. During the late 1290s in medieval Europe, guilds—the pre-cursor to unions—were responsible for product and service quality. From 1700 to 1900, product quality was determined by the individual craftsman’s efforts. At the close of the 19th century, Eli Whitney introduced standardized, interchangeable parts to simplify assembly. In 1875, Frederick W. Taylor introduced the scientific management principles, which divided work into smaller, more easily accomplished tasks. Taylor believed the key to productivity and improved quality was knowledge, organization, and leadership. In 1903, Karol Adamiecki developed the harmonograph, a chart depicting workers’ movements and actions indicating the causes of low productivity and potential quality issues. Quality principles were accelerating at the beginning of the 20th century as manufacturers began to shift from purely focusing on their production economy to balancing the number of products produced while meeting increased consumer demands for quality.
In 1901, the Engineering Standards Committee was formed in Great Britain to establish imperial standards in all fields. In 1906, the International Electro-Technical Committee was created to prepare and publish international standards for all electrical, electronic, and related technologies. By 1930, most industrialized countries had established national standards organizations. Most of these national standards organizations were linked to the International Federation of the National Standardizing Association, formed between 1926 and 1928. Global standard settings were stifled during the Great Depression of the 1930s and were furthered hampered in 1939 with the beginning of World War II.
In 1941, the United States entered World War II. The U.S. government enacted legislation to switch the civilian economy to military production. During this time, military contracts were typically awarded to the lowest bidding manufacturer. Product quality was determined by inspection after delivery. This quality inspection method consumed copious amounts of human resources and led to recruiting and retaining problems. With the help of Bell Labs and Dr. Walter Shewhart, the military adopted sampling inspection techniques to save time and resources.
To read this entire article, which appeared in the February 2021 issue of PCB007 Magazine, click here.
Suggested Items
Green Circuits to Exhibit Full-Service Electronics Manufacturing Solutions at 2025 SMD Symposium
07/02/2025 | Green CircuitsGreen Circuits, a full-service Electronics Manufacturing Services (EMS) partner to leading OEMs, is pleased to announce its participation in the 2025 SMD Symposium, taking place August 5-7 at the Von Braun Center in Huntsville, Alabama.
RTX, Shield AI Partner to Develop New Defense Capabilities
07/01/2025 | RTXRTX and Shield AI announced a new partnership to integrate Shield AI capabilities into select RTX defense products, like loitering munitions and sensors. This collaboration will deliver enhanced, autonomous capabilities to US and allied defense forces.
Lockheed Martin Completes Acquisition of Amentum’s Rapid Solutions Portfolio
07/01/2025 | Lockheed MartinLockheed Martin has closed its acquisition of the Rapid Solutions business of Amentum, an engineering and technology solutions company.
Saab Receives Order for Ground-Based Air Defense from Sweden
07/01/2025 | SaabSaab has received an order from the Swedish Defense Materiel Administration (FMV) for the mobile short-range air defense solution RBS 70 NG with missiles.
Kitron Strengthens Order Backlog with EUR 11 Million Contract for Defense Communication
07/01/2025 | KitronKitron has received an order valued at EUR 11 million to produce advanced military communication products destined for the European market.