-
- News
- Books
Featured Books
- pcb007 Magazine
Latest Issues
Current IssueInventing the Future with SEL
Two years after launching its state-of-the-art PCB facility, SEL shares lessons in vision, execution, and innovation, plus insights from industry icons and technology leaders shaping the future of PCB fabrication.
Sales: From Pitch to PO
From the first cold call to finally receiving that first purchase order, the July PCB007 Magazine breaks down some critical parts of the sales stack. To up your sales game, read on!
The Hole Truth: Via Integrity in an HDI World
From the drilled hole to registration across multiple sequential lamination cycles, to the quality of your copper plating, via reliability in an HDI world is becoming an ever-greater challenge. This month we look at “The Hole Truth,” from creating the “perfect” via to how you can assure via quality and reliability, the first time, every time.
- Articles
- Columns
- Links
- Media kit
||| MENU - pcb007 Magazine
Estimated reading time: 3 minutes
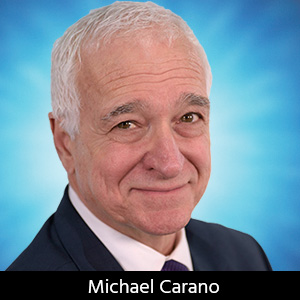
Contact Columnist Form
Trouble in Your Tank: Plating Anomalies and Defects—Part 2
Introduction
One of the most difficult things about troubleshooting PCB defects is getting to and understanding the root cause of defects. Many of these defects can have multiple origins. And many may not manifest themselves in the process where the defect actually occurred. Thus are the perils of jumping to conclusion about the defect. Not understanding the true genesis of the defect will lead to incorrect remedies to these issues. I will now present some of these defects and the possible remedies.
Blisters (Hole Wall Pull-away)
The common complaint one hears is that “the copper plating is peeling.” Okay, but where? From the surface or from within the via? What about the interconnect? And is the peeling layer the electroless copper deposit or the electrolytic copper? These are the questions one must answer to properly troubleshoot the defect. Figure 1 shows a real-life example of a blistered or peeling deposit. In Figure 1, the copper deposit has actually flaked off or blistered from the hole. In some cases, the deposit did not completely flake off the surface, but indeed did pull away from the hole wall. This condition is referred to as hole wall pull-away (HWPA).
Now the question is, where is the origin of the blister? The good news in this case is that we are only looking at the electroless copper. There has yet to be an electrolytic copper deposit applied to the circuit board. But that is all one can tell at this point. Figure 2 shows an actual cross-section of a circuit board that was part of the production lot related to the photo in Figure 1.
There are several possible causes for the condition shown in Figure 1:
Inadequate desmear
- Overactive electroless copper process
- Drill debris
- Excess catalyst
- Insufficient filtering of electroless copper solution
- Instability (“dusting” in the bath)
- Excessive solvent penetration
- Poor rinsing or rinse water quality
A more typical example of HWPA is depicted in Figure 3. The deposit pulled away from the hole wall but did not fracture or flake off. Nonetheless, this is a defect and must be remedied. The root cause of HWPA is very similar to those that lead to flaking and blistering. I consider this at the very least a “process indicator.” This means that the desmear and metalization processes need attention. Of course, if the hole wall pull-away causes a violation of hole wall minimum diameter or leads to other violations in hole diameter dimensional requirements, then this is, of course, a cause of concern and will result in non-conformance.
So, one is dealing with the origin of the blister or peeling deposit prior to electrolytic copper plating. Table 1 lists the most common causes for this type of defect.
Table 1: The most common causes for this type of defect.
A precautionary note: Don’t confuse HWPA with resin recession (Figure 3). Resin recession is a material-related issue where the resin has recessed or shrunk back away from the plating. This is evident generally after thermal stress. According to the IPC-A600K, resin recession is permissible. Resin systems, for lack of a better term, will “shrink.”
Keep in mind that there is no substitute for process control. The operators should have a basic understanding of why certain processes must be controlled within the stated limits. This will go a long way in preventing costly rejects.
I am a true believer in the inter-relatedness of processes and the origin of process-related defects. It is helpful to keep a few things in mind when troubleshooting a process issue.
To be successful at troubleshooting a problem, common sense usually applies. Basically, one must first:
Identify the problem or problems (be as specific as possible)
- Determine possible causes (looks for links to those other less obvious processes)
- Methods and procedures to test to see which causes are most likely
- Test the assumptions
- Implement corrective action
While this sounds like an oversimplification, this approach is required to properly identify and attack the problem at hand. A structured routine is really what is required. Remember the most critical success factor is being able to get to the root cause of the problem. Stop the finger pointing and get the different process teams to work together.
In these columns we will attempt to provide some insight as to the cause or causes of these non-conforming defects and the potential solutions. We will discuss process parameters and the importance of control of the processes.
This column originally appeared in the April 2021 issue of PCB007 Magazine.
More Columns from Trouble in Your Tank
Trouble in Your Tank: Metallizing Flexible Circuit Materials—Mitigating Deposit StressTrouble in Your Tank: Can You Drill the Perfect Hole?
Trouble in Your Tank: Yield Improvement and Reliability
Trouble in Your Tank: Causes of Plating Voids, Pre-electroless Copper
Trouble in Your Tank: Organic Addition Agents in Electrolytic Copper Plating
Trouble in Your Tank: Interconnect Defect—The Three Degrees of Separation
Trouble in Your Tank: Things You Can Do for Better Wet Process Control
Trouble in Your Tank: Processes to Support IC Substrates and Advanced Packaging, Part 5