-
- News
- Books
Featured Books
- pcb007 Magazine
Latest Issues
Current IssueInventing the Future with SEL
Two years after launching its state-of-the-art PCB facility, SEL shares lessons in vision, execution, and innovation, plus insights from industry icons and technology leaders shaping the future of PCB fabrication.
Sales: From Pitch to PO
From the first cold call to finally receiving that first purchase order, the July PCB007 Magazine breaks down some critical parts of the sales stack. To up your sales game, read on!
The Hole Truth: Via Integrity in an HDI World
From the drilled hole to registration across multiple sequential lamination cycles, to the quality of your copper plating, via reliability in an HDI world is becoming an ever-greater challenge. This month we look at “The Hole Truth,” from creating the “perfect” via to how you can assure via quality and reliability, the first time, every time.
- Articles
- Columns
- Links
- Media kit
||| MENU - pcb007 Magazine
Estimated reading time: 7 minutes
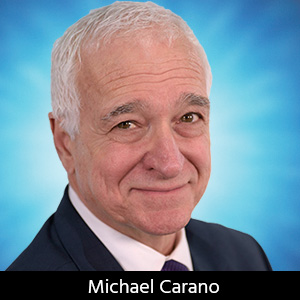
Contact Columnist Form
Trouble in Your Tank: Training Your Team and Tools for Success
Introduction
While this month’s column departs somewhat from my usual topics, the subject matter is no less critical. As someone who has been troubleshooting and problem solving for many years, I have found that the process and tools are extremely important.
I was asked to consider addressing the topics of optimizing business processes and strategy, process optimization, and training your team. I believe developing critical thinking skills will help engineers troubleshoot technical issues and bring them to a quick resolution as this is certainly a good lead-in to training your team.
Troubleshooting 101
This should come as no surprise to those of you who read my monthly columns or have met me in your circuit board facility: Remember, time is money. The longer a problem goes unresolved the more money, and certainly future customer goodwill, can be lost. When being called on to solve technical issues—whether it be a delamination situation, copper plating failures, or solderability defects—I stress a few simple rules:
- Walk the line and watch the operators in action.
- Review documented work procedures.
- Check rinse water quality and dwell times—are you rinsing away the contaminants or simply dragging them along with the boards to the next critical process?
- And the biggest sin: “Yes, everything in the chemistry is being controlled per datasheet.”
6S methodology is not new. The process is focused and disciplined. The process is DMAIC[1]: Define–Measure–Analyze–Improve–Control.
Use various tools, including Pareto charts, histograms, process control charts, and fish-bone diagrams. Use logic; think critically and strategically. Basically, it is quite simple: Develop the troubleshooting skills necessary to solve process problems efficiently.
The rule of thumb is to keep the troubleshooting project as manageable as possible. Brainstorm to understand the linkages in the upstream and downstream processes and potential effects of process variation in these process steps. Gather all pertinent information including SPC charts, temperature logs, analysis records (including records of calibration and analytical standards), and the like. Then develop a cause-and-effect diagram. Fishbone diagrams serve this purpose well. At the risk of having hundreds of factors to investigate, only the most likely causes should be investigated first. This is where experience and critical thinking skills come into play. This will serve to weed out those processes that are not contributing to the defect.
When was the process audit performed, and on what operations within the PWB fabrication operation? Ongoing process audits jointly and separately performed by your supplier and designated individuals in the fabricator’s facility should be standard operating procedure. Process audits alert the manufacturer if a process is “drifting” out of the control window. Suggest your company select an experienced group of operators, engineers, and other science disciplines to be trained in the art of conduct a process audit.
Table 1 shows an example of one such checklist.
A fishbone diagram is another extremely useful tool to conduct root cause analysis of the problem[2]. Your team can use the fishbone diagram (Ishikawa diagram) to explore the potential causes of a particular issue or defect. After brainstorming some ideas and looking for possible linkages, sort them into groupings to better understand the root cause of the problem. A fishbone diagram is particularly useful when you don’t have very much quantitative data available, and can only rely on your team’s experience. Fishbone diagrams show possible linkages among the critical aspects of machines, materials, people. See an example of a fishbone diagram in Figure 1.
Once the team has set up its test plan based on a narrowing of potential causes, the divide-and-conquer approach will aid in the efforts. For example, if one suspects that thin plating of copper in the hole is caused by problems associated with the electrodeposition process, simply processing the PCB in the acid copper plating solution for the required time and current density should tell whether the copper plating process or the equipment (copper plating anodes, rectifier, or electrical connections, etc.) are the cause. If not, then one must examine the previous steps. Did anyone check the cables leading from the power supply to the plating cell? Are there resistance issues with the plating racks or other connections that may cause less current to flow into the cell (Figure 2)? Are there discontinuities in electroless copper deposit or direct metallization process causing thin plating? Are there voids in the vias that have not yet been detected? These are just some of the questions to be asked. Only a systematic approach will help solve problems expeditiously.
Other Essential Skills
There are a few other skills (what we call soft skills) that I see as being absent in many of the facilities I visit. Here are a few of these critical soft skills that one needs to learn:
Design of Experiments
First and foremost, understand how to design an experiment (DOE). This requires brainstorming and certainly a team approach to solving the problem. DOE methods are for engineers to employ during experimentations. Whether it is “problem solving” or “process development,” the DOE experimental methods provide the most efficient means of determining the correct answers, and it is critical for troubleshooting. It also helps one understand those variables that are weighing more heavily on the issue and those that are of little consequence.
Start with a brainstorming session and construct a fishbone diagram or something similar. This will help put in perspective the possible causes of the problem you are seeing. From there, focus on the most likely causes of the defect, then design the experiment to investigate the most likely causes.
TQC/Six-Sigma/Statistics/Curve Fitting
Total Quality Control and Six-Sigma (6S) is the philosophy of continuous improvement through statistical techniques and a commitment to excellence. The PDCA process (Plan-Do-Check-Act) is a central theme using the nine basic tools (cause-effect, process flow, Pareto, scatter, histograms, process capability index, control charts, time-series, and check sheets). A useful book is the free Statistical Engineering Handbook available for download from NIST[3]. A fundamental place to start is with "Select the Right Statistical Tools" (Measurement System Analysis, SPC, Comparative Methods or DOE).
FMEA
FMEA is the failure mode effect analysis[4] and is critical for problem solving. The link in the reference provides an in-depth overview of FMEA.
An example of just one failure mode related to use of an innerlayer bonding process is shown in Table 2. Of course, there are multiple process steps to consider. Here for purposes of illustration, we only show issues related to lack of uniformity of the coating appearance. Note that the higher the value in the severity column, the greater the effect on the defect.
Certainly, there are additional skills I would recommend, including improving one’s technical writing skills. However, what about acquiring additional skills related to PCB fabrication and assembly? This is where IPC comes in.
IPC Standards and Certification
Preparing your workforce to successfully face challenges inherent in today’s complex manufacturing environment may be the most important investment management makes. Certainly, equipment and automation are significant investments. However, without a well-trained workforce, these investments will be very slow to pay off.
This all starts with the standards. Why use IPC standards? First, adoption of IPC standards across the electronics industry supply chain enhances the quality and the reliability of electronics products. Adoption and use of IPC standards drive quality of the finished product as well as the consistency of the processes used in the fabrication of the device including printed circuit board and printed circuit assemblies. Train your employees in the understanding and use of these workmanship standards. When you build product to IPC standards, there are several other quantifiable benefits to your business. These include:
- Increased customer satisfaction
- Improved production efficiencies
- Improved final yields
- Improved workforce performance
A hidden benefit of improved workforce performance is that the employees associated with the process gain a deeper connection to their job and gain additional pride in what they are doing. When you have a high-quality and consistent manufacturing process, yields go up, product is delivered to the customer on time and in full, and rework is minimized.
IPC has multiple workforce training programs available in various formats including in-person training and through IPC Edge[5] (the online educational and training portal of IPC).
While this article only brings to light several of the critical skills and tools required for optimizing performance, there are other skills and tools that at some point should be considered. However, if one can acquire or improve on the skills we outlined here, one will achieve a much deeper understanding of critical aspects of the printed circuit board fabrication process and in turn ensuring the product is of the highest reliability. As always, understanding linkages between processes, materials, and manufacturing operations will provide the team with more effective and efficient problem-solving resolution.
References
- https://www.leanscape.io/dmaic-model/
- The Fishbone Diagram (Ishikawa Diagram)
- Statistical Engineering Handbook
- Failure Mode Effect Analysis
- Homepage | IPC Edge Training
This column originally appeared in the May 2021 issue of PCB007 Magazine.
More Columns from Trouble in Your Tank
Trouble in Your Tank: Metallizing Flexible Circuit Materials—Mitigating Deposit StressTrouble in Your Tank: Can You Drill the Perfect Hole?
Trouble in Your Tank: Yield Improvement and Reliability
Trouble in Your Tank: Causes of Plating Voids, Pre-electroless Copper
Trouble in Your Tank: Organic Addition Agents in Electrolytic Copper Plating
Trouble in Your Tank: Interconnect Defect—The Three Degrees of Separation
Trouble in Your Tank: Things You Can Do for Better Wet Process Control
Trouble in Your Tank: Processes to Support IC Substrates and Advanced Packaging, Part 5