-
- News
- Books
Featured Books
- pcb007 Magazine
Latest Issues
Current IssueInventing the Future with SEL
Two years after launching its state-of-the-art PCB facility, SEL shares lessons in vision, execution, and innovation, plus insights from industry icons and technology leaders shaping the future of PCB fabrication.
Sales: From Pitch to PO
From the first cold call to finally receiving that first purchase order, the July PCB007 Magazine breaks down some critical parts of the sales stack. To up your sales game, read on!
The Hole Truth: Via Integrity in an HDI World
From the drilled hole to registration across multiple sequential lamination cycles, to the quality of your copper plating, via reliability in an HDI world is becoming an ever-greater challenge. This month we look at “The Hole Truth,” from creating the “perfect” via to how you can assure via quality and reliability, the first time, every time.
- Articles
- Columns
- Links
- Media kit
||| MENU - pcb007 Magazine
Estimated reading time: 5 minutes
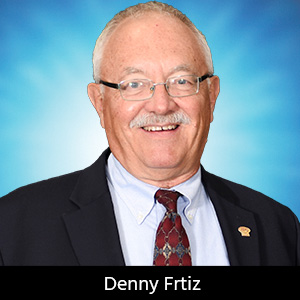
Defense Speak Interpreted: The ‘Trouble’ With Obsolescence
How could a simple word like obsolescence stir up so much trouble within the Defense Department? The dictionary defines obsolescence as the process of becoming obsolete or the condition of being nearly obsolete.
Within Defense, there are two distinct reasons for obsolescence:
- Newer technology has replaced the part, assembly, system, or the weapon with something far more advanced. It is judged that replacement would be far better. Frequently a cost/benefit analysis is used to make this decision.
- The factors of Diminishing Manufacturing Sources and Materials Shortages (DMSMS) comes in to play. That is, it is just no longer possible to get replacement parts or assemblies for a fully functioning weapon system for a variety of reasons.
Let’s discuss those in reverse order, just to emphasize the problems for Defense Department. In fact, Defense has a 191-page guidebook for managing DMSMS, called the SD-221.
Page 120 of SD-22 states:
Obsolescence is not synonymous with DMSMS. Instead, it is less definitive and is situationally dependent in that an item can be obsolete from one perspective, but not from another. In the context of DMSMS management, an item is obsolete if it is out-of-date and superseded by something new. Below are key underlying causes of an item being out-of-date:
- Technology
- Function
- Regulation
- Supportability
- Market Demand
However, obsolescence and DMSMS overlap to a great extent. SD-22 is full of examples where there is overlap and a few cases where they are exclusive. Let’s look at these from the Defense systems’ perspective, rather than from circuit board technology, which we will discuss later.
- Technology: The way the U.S. has fought wars has evolved. In the 1960s and ‘70s, Defense planned for “great power conflicts”; that is, among a very few nations with huge militaries. Then, “asymmetric warfare” was the target with small bands of guerilla fighters causing the most damage to enemies. Small jeeps and trucks were subject to roadside bombs, so mine-resistant vehicles replaced jeeps. Now, manned vehicles may be overtaken by robot controlled unmanned vehicles
- Function: Artillery has been the heavy firepower weapon since the Middle Ages. Now, artillery puts soldiers too close to the enemy, and missiles and bombs threaten to replace artillery.
- Regulation: Chemical weapons were used in World War I. However, treaties after that conflict outlawed their use in future conflicts. Granted, some rogue states have developed and tried these “weapons of mass destruction,” but that has caused international alarm and was a listed cause of the second war in Iraq.
- Supportability: This entails many materiel aspects—ammunition, spare parts, required facilities, trained personnel, etc. There are many cost/benefit relationships that must be explored before a switch is made to newer weapons systems. The U.S. Marines have recently decided that they will abandon tanks and replace that firepower with missiles and smaller infantry carrying vehicles. Landing tanks, spare parts, fuel, and trained personnel are all factors in the Marine decision.
- Market demand: While it is hard to think of weapons systems going to “a market.” it is possible to look at this aspect of product management. The demand for diesel/electric submarines has dropped off and replaced by nuclear subs. The recent Australian cancellation of a diesel electric program with France and the order of nuclear subs from Great Britain and the United States caused international friction in the last month.
Now, let us look at a technology-based obsolescence closer to home: the bare board and board assembly level. Most of the commercial electronics world started to change to Pb-free constructions with the advent of Restriction of Hazardous Substances (RoHS) starting around 2006. This triggered a change in solders, assembly temperatures, component surface finishes, higher temperature laminates, and complete separation of assembly lines as Pb-containing or Pb-free. The mixing of Pb-free component and board finishes with Pb-containing solder, or vice versa, has been shown to produce inconsistent solder joint performance. And, there is one thing demanded of Defense electronics: consistent performance.
At the time of RoHS implementation, most commercial electronics switched to solders based on tin/silver/copper compositions; the SAC solders are based on the first letter of their chemical designation – Sn/Ag/Cu. This family provided a narrow melting temperature, relatively low cost, and performance that met moderate swings in operating temperatures, say 0 to 100°C. However, Defense electronics must perform over a wider range, typically -55 to 125°C. Over this range, eutectic SnPb solder shows better elasticity and hence fatigue life. My own summary in plain words is that Pb-free solder is stronger and more brittle while SnPb is more elastic, but weaker. So, Defense electronics pretty much stayed with SnPb solder for the last 15 years.
Now, how does obsolesce enter the picture? There are many factors, including:
- Defense takes only 1-2% of the circuit components, particularly the most advanced chips for such technologies as artificial intelligence, 5G, augmented reality, and self-guided vehicles
- With this low demand for Pb containing attachment (solder balls for BGAs), semiconductor suppliers are no longer supplying Pb-containing solder ball BGAs
- Defense suppliers must have the standard commercial chips sent to service centers where Pb-free balls are removed and Pb-containing balls attached—called re-balling. This costs money and lengthens the delivery time, exacerbating the already long semiconductor lead times
- Solder suppliers have worked to develop newer solder alloys to overcome Pb-free solder brittleness with thermal cycling, better resistance to shock and vibration, and driving melt temperature down toward eutectic solder temperatures
That all gets us back to the dictionary definition I started with: Obsolescence is when newer technology has replaced the part, assembly, system, or the weapon with something far more advanced. It is judged that replacement would be far better. Frequently, a cost/benefit analysis is used to make this decision.
Many Defense contractors are now doing the cost analysis of whether to engineer their newest electronics systems as Pb-free with some electronics packaging design work to properly place components, use underfills or board stiffeners for vibration or shock, and now switch manufacturing lines to all Pb-free pastes. Those efforts will eliminate the re-balling costs with the added lead time and assure there is no redesign or re-qualification for future builds as more and more components are only supplied Pb-free.
Sadly, there is no free lunch in Defense electronics manufacture. However, many program managers, defense primes, and assembly houses are looking at the obsolescence issues with Pb-containing solder and making the choice to go Pb-free now, rather than wait for an uncertain future supply chain.
References
- Diminishing Manufacturing Sources and Material Shortages, Defense Standardization Program Office, January 2016.
Dennis Fritz was a 20-year direct employee of MacDermid Inc. and is retired after 12 years as a senior engineer at (SAIC) supporting the Naval Surface Warfare Center in Crane, Indiana. He was elected to the IPC Hall of Fame in 2012.
More Columns from Defense Speak Interpreted
Defense Speak Interpreted: JADC2—Why It’s More Relevant Than Ever in Drone WarfareDefense Speak Interpreted: Is DARPA Still Around After CHIPS?
Defense Speak Interpreted: Is There Still a CHIPS Act?
Defense Speak Interpreted: Update on the Continuing Resolution and Budget Process for Defense
Defense Speak Interpreted: It’s Time for a ‘Defense-Speak’ Update
Defense Speak Interpreted: SWaPing Nanosatellites for Defense Systems
Defense Speak Interpreted: Who Won the Project Convergence War Game—Evil Chaos or JADC2?
Defense Speak Interpreted: What Happened to Our Defense JEDI?