Averatek Moves Ahead With A-SAP™, ASAP
November 4, 2021 | I-Connect007 Editorial TeamEstimated reading time: 13 minutes
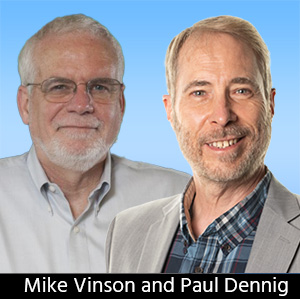
During DesignCon, the I-Connect007 Editorial Team spoke with Mike Vinson and Paul Dennig of Averatek. They discussed the company’s latest advances in air cavities and semi-additive processes, and what this new technology will mean to the industry, especially PCB designers.
Andy Shaughnessy: Mike, good to see you again. Paul, nice to meet you. How are things going?
Mike Vinson: Really well. With all of the challenges that we had through the pandemic, and still have today, we’ve been pushing forward a lot of new technologies, including the one that we introduced today, the AirGuide technology. We’re also continuing work on rolling out our semi-additive process, the A-SAP™ process, to several licensees. All throughout this time, it’s been challenging. It’s caused some delays, but all together we’ve been moving forward.
Shaughnessy: What is your role, Paul?
Paul Dennig: I’m the director of technical product marketing, and I support multiple efforts, both helping with the existing technology and bringing up some new technologies and exploring new markets for them.
Shaughnessy: Let’s talk about your role for a little bit, and then let’s move over and talk about what’s going on with the rollouts. So, in your role, you’re supporting a lot of different programs.
Dennig: Right. I support AirGuide. That’s a principal project that Mike and I are pursuing together. We incorporate air cavities into a lot of the radio frequency, microwave, millimeter-wave band types of new devices that can be made with these cavities. So, for example, Mike presented today, our patch antennas. We’re able to go from the standard construction techniques, at about 70% efficiency up to now measured, not just simulated, but measured, at over 96% efficiency. So, this could mean for example, to someone with a cell phone, or equivalent device that they could run their rig for 20% longer time or go maybe 25% farther distance. So, that’s quite an exciting development for us.
Shaughnessy: Because the signal travels faster in the air, correct?
Dennig: Well, we’re comparing waves traveling through air to waves traveling through solid dielectric. In the latter case, you would be making patch antennas with standard printed circuit board dielectric. In our case, with this new development, we have an air dielectric underneath and on top of the antenna. We have a proprietary way to construct the antennas, and that is what results in a novel behavior.
Shaughnessy: Paul, you’re relatively new to the company. What’s in your background?
Dennig: Well, I have a long-story career in many different industries. I’m a veteran of the semiconductor industry, where I did processes and design. I’ve been in the hard disk drive arena where I worked on the development of substrates for hard disk drives. So, looking at everything all together, with components, power electronics, and nanotech, these all fit very well with my background. Plus, I’ve done a lot of work in the marketing area for the last 10 years.
Shaughnessy: Great. So, tell us about how the air cavity works.
Vinson: We’ve named it AirGuide. We came up with it when we were talking with some people trying to develop technologies for the RF market, and they were trying to figure out how to build lower cost wave guides using air as a dielectric, which most wave guides do that today. They’re big metal boxes; you mill out the insides and put a very precise shape in there. They wanted to know if they could reproduce that air cavity with that very precise shape and embed it in a printed circuit board and do it with printed circuit board materials and printed circuit board costs.
So, after talking to them, we came up with this AirGuide technology in which we can now plate the copper up on a form, embed that form in the printed circuit board, and then just have air left behind when we’re finished. All of the electrical connections, the RF connections through the printed circuit board interconnect type technologies like vias and that sort of thing, and then have a printed circuit board that we can mount other components like amplifiers and circulators. You could even mount antennas on there, similar to the ones we demonstrated today, and then have a complete system on a single printed circuit board.
Shaughnessy: How is that going to change the designer's job? It sounds like they’re going to have to learn a few new tricks.
Vinson: It does a little bit—there will be a few new tricks to this. Today, designers are embedding parts in printed circuit boards, and there are plenty of techniques available for this. We didn’t really get too far afield from those. But the big trick that people are learning today is how to design RF circuits that are efficient and practical for the low-cost applications that they’re pursuing. So, everything from 5G towers to radar on automotive applications we’re seeing now can benefit from these kinds of advances.
Shaughnessy: Right. It’s different than additive and semi-additive…
Vinson: But it leverages off those same technologies that we developed from the semi-additive processes.
Nolan Johnson: Speaking of which, how’s that going?
Vinson: Semi-additive is going great. We have three licensees now ready to support the market demand. We have several others that are now evaluating the technology, and we expect to have a few on board by the end of the year. The developments in the area continue to move forward as we test different types of substrate materials from the low loss materials that we’re working with, and some showing extremely good performance that we have, and then just the regular FR-4 type materials that we’re also working with. As well as flex materials in everything from RF to medical.
Johnson: We’ve talked about these products and processes, as you were bringing them out a couple of years ago, and ongoing from there. What’s emerging from the fabricator’s point of view? What’s the benefit to them in these processes, and has there been anything that was unexpected, but a pleasant surprise?
Vinson: I can’t think of anything unexpected in the last two years, but before that there were a lot of surprises. We’ve basically been in a rollout of the technology that we’ve anticipated. But the licensees are finding that they can do many things with this technology in terms of reducing the size of the circuits, reducing the number of layers required to make a particular function and a printed circuit board, and the ability to shrink everything down to smaller size. So, if you’re building things, and you’re basing your costs on the size of a panel, and the number of layers in that panel, and you’re reducing all of that down to a much smaller size, and fewer layers, you not only have a higher value product when you finish, but it’s one that costs you less to build. And that’s the things that they’re discovering in their endeavors and pushing the technology forward even faster.
Johnson: Right. Did I just hear you say that they can accomplish this in fewer layers?
Vinson: Yes.
Johnson: That sets up a different behavior for the designer themselves.
Vinson: Exactly, it does, and that’s another key point. We’re also working here today with other designers to educate them on the advantages that they can achieve with this new technology and the things that enables in the design so that they can then extract the value that we’re seeing from this new technology.
Johnson: There’s so much going on right now in the sense of to be a designer. You have to basically be an engineer now.
Vinson: Almost. It seems it’s no longer just drafting out, connecting things. You must understand all of the interactions between your circuitry, and the circuitry that you’re implementing on the board, and it’s getting complex, especially as speeds go up.
Johnson: We’re starting to have to pay attention to electromagnetic fields in a way that we never did before. This becomes a key issue for the design team to understand, along with even the chemical processes. Do you see from your perspective that this could maybe push more toward an increase in captive facilities to connect up with an OEM’s particular design requirements?
Vinson: That’s a fascinating concept, and that’s counter to where the market’s going now. We see all of these non-captive third-party type manufacturers merging and growing larger in their entities themselves instead of joining directly up to the OEM. What it seems that we’ve found in terms of implementing our technology in the stream is that instead of being a material supplier to the third party, we need to be an implementation of innovation between the OEM and the third-party supplier.
So, we’re trying to provide that link between the OEM and their design resources and the third-party supplier and the PC board to provide that knowledge that they need to go from what the OEM would really like to have, and the kind of profits that the supplier would really like to have and enabling all of that through our technology.
Johnson: Maybe I’m oversimplifying, but there’s a sense of educating the designer so that by doing so you end up driving business to the fabricators that are using your process.
Vinson: It does. But the other issue is that’s a little bit of a chicken and egg, and during that chicken and egg period we need a lot of support from both sides, and we’re getting that because there is such an interest in achieving what we can do with this technology.
Johnson: That’s a really intriguing situation to be in.
Vinson: It is, and it’s very exciting. These are really exciting times right now.
Johnson: Look ahead over the next 12 months or so. How will that play out?
Vinson: Over the next 12 months, I think you’ll see more involvement from a number of areas—everything from sensors to the actual printed circuit boards themselves and miniaturization. This technology can enable the more advanced packages and the smaller components to be used on the printed circuit board without a great deal of expensive modification, and I think that will drive down costs all around to be able to use commercial packages with specialty applications. In the next 12 months, I think we’ll see a lot of things, like representative boards being built for certain products and using those boards as a reference design for the designers going forward. And at that point, that’s when we’ll see that technology take off.
Shaughnessy: Does IPC have existing standards for additive and semi-additive?
Vinson: They’re working on them, and they’re working on the higher-density aspects of it as well. We’re looking forward to seeing how those different standards can be applied here, as well as to semi-additive, and looking at how they treat vias and specify them.
Shaughnessy: Are the EDA tools adaptable for this sort of thing, or do the designers have to tweak it in any way?
Vinson: We’re working with them in both cases. I believe it was Altium that we did the reference design with. We were looking at one of their reference designs in a conventional design role, and then with the A-SAP™ design rules, so that their tool can then be adapted to it. We do see a few shortcomings, but not really. It can all be easily worked around, but it’s not as automatic when you go to the higher density.
Johnson: Where does a PCB designer go to get started with this technology, and understanding how this can be used in their job?
Vinson: They can contact us, and we can help steer them. We’ve also got a couple of consulting designers and universities working on the different design rules used in designing these kinds of circuits, both for RF and high-speed digital.
Dennig: We plan to roll out some application notes along the way that will highlight where A-SAP™ can be beneficial, and how it can be integrated with standard processes all on the same board.
Shaughnessy: Is this more attuned with certain materials than with others?
Vinson: We’re testing a broad spectrum of materials and it works very well with a broad spectrum of materials. There are some materials that this just doesn’t work with quite as well with as others. But for the most part, it’s been applied across just about every performance type of material that there is out there. We’ve had some surprisingly strong results from materials like LCP, and some of the Pyralux products from DuPont, and then we’ve had some surprisingly strong performances from the Rogers 3000 series of materials that we’ve been working with, which are all very supportive of these higher performance designs and criteria.
Dennig: So, some of those advances lead us to biomedical applications, which we are involved with, and I’d like Mike to say something about that.
Vinson: Yes. With the A-SAP™ process, we can use metal systems that aren’t harmful to the inside of the body. We don’t require copper and/or nickel to execute a fine line circuit. We can make these with gold and other noble metals that won’t be harmful to the body, gold and platinum, mainly. And things like LCP, which were difficult to work with in this area before, are now just a brave new world for us in that area.
Johnson: This is really exciting, then.
Shaughnessy: What’s the limit on that? Does Moore’s law even apply at this level?
Vinson: The A-SAP™ technology we designed primarily to go down to around 15-micron space and trace but can go further, and we’re working on other technologies that will take us down into the five-micron range with the similar proprietary chemistries that were used for A-SAP™. So, we don’t really see that we’re going to run out of the Moore’s Law. What we have seen in the past is that Moore’s law is applied to ICs. When you looked at packaging, semiconductors, and the printed circuit board area outside of the chip itself, they lagged behind. So, like Moore’s law, I believe that we’re going to start catching up with these other interconnect areas.
Shaughnessy: Are there any fabricators who are doing additive, and semi-additive? I imagine we’ll see some.
Vinson: I’m sure you will, but I can’t think of any right now.
Dennig: You hit on a really key point. I think that besides increasing performance and doing smaller feature sizes and higher speeds, addressing the types of things that you were talking about with the transmission lines, and being intimately tied to circuitry, we see some evidence that we can minimize environmental footprint. We can shrink circuits, use fewer layers, and we have other products, product lines, that will also help similarly with the environment. So, we’re also looking into what is our effect on the environmental footprint.
Shaughnessy: It’s a fairly green process, right? Green is a great marketing tool too, in addition to being a good thing.
Johnson: This is why I can’t help but think about new captive facilities when talking about your process.
Vinson: Well, that is certainly something that could happen. We don’t necessarily promote it or push it. But, it’s certainly an avenue that could come on.
Johnson: Right. Well, why design for past processes when you’re doing something for future processes?
Vinson: So, there’s a lot of economy in this, and we’re working on getting to the economies of scale.
Johnson: No, that’s great. Anything else you’d like to mention?
Vinson: Have you guys have heard of our Mina product?
Dennig: We’re looking at putting components on aluminum on PET (Al-PET) substrates. This plastic is similar to what you have in a plastic water bottle. The product that enables soldering is called Mina, and it’s quite exciting.
Vinson: There’s an additional thing we’re doing with some full-additive products and 3D printing. We did a cylindrical antenna for GPS where we 3D printed the pattern around a cylindrical ceramic rod and did that fully additive as well.
Shaughnessy: Very good. Thanks for your time today.
Vinson: Thank you.