Catching Up with Allen Keeney of Johns Hopkins University
December 16, 2021 | Dan Beaulieu, D.B. Management GroupEstimated reading time: 7 minutes
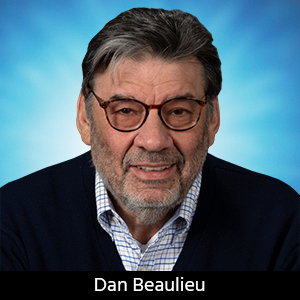
I have always been fascinated by research labs, especially those tied to major universities. These are the true leaders of innovation and invention and at the very top of the PCB industry. So, when I met Allen Keeney, chief engineer of the Advanced Electrical Fabrication Group at the Johns Hopkins Applied Physics Laboratory (APL) in Laurel, Maryland, I jumped at the chance to talk with him. You will enjoy this look at another facet of our PCB industry.
Dan Beaulieu: Allen, thanks for talking with me. What is your background, how did you get to APL, and what do you do there?
Allen Keeney: I grew up wanting to build stuff, specifically for space. While working on my master’s degree in physics at Johns Hopkins, I was exposed to APL and applied for a job as a chemist in the electronics fabrication area. I then spent a decade working with microelectronic substrates and helping out occasionally in the PCB fabrication shop. During a reorganization, I was appointed as supervisor of the PCB fabrication shop; several years later, I became a supervisor of the electronics fabrication area (PCB fabrication, assembly, and microelectronics). A decade later, I turned it over to someone else and became the chief engineer for the area, where I focus on improvements (quality, capability, schedule, and cost) for the group.
Beaulieu: What kind of work is done in the lab? Is it primarily research?
Keeney: APL works on government missions with the goal to make critical contributions by responding to critical challenges. We solve complex research, engineering, and analytical problems that present challenges to our nation. The expertise here at the lab is broad and focuses on innovation and systems engineering solutions to large problems. In our electronics group, we are focused on providing capabilities to build the hardware needed to solve these issues, whether it’s critical national security prototypes, critical hardware for a NASA mission, or the development of prosthetic limbs.
The lab as a whole does a lot of things, but specifically our groups provide design, fabrication, and assembly services for the missions at the laboratory as well as those of agencies of the U.S. government as called upon. About 50% of our work goes to building hardware for scientific space missions. Spacecraft or instruments built at APL have visited every planet in the solar system, as well as Pluto and some asteroids. The other 50% of our electronics fabrication goes toward missions for other government agencies; we do lots of other cool things.
Beaulieu: Can you talk about your technology? What technology of PCBs do you produce?
Keeney: Sure. There are two primary foci for PCBs that we build at APL. The primary one is high reliability boards for spacecraft. Boards are built and assembled to IPC specs with the space addendums. We also get involved in evaluating boards from other vendors to ensure the specifications are met. The other focus is on prototype boards, often designs pushing the use of 01005 components and thin substrates.
Beaulieu: Is much of it experimental or built to design?
Keeney: Most are built to design; however, we are usually only building a few of the design, so no large quantities here. There are some experimental designs that push sizes (small or large) or use more exotic materials for RF or other applications.
Beaulieu: Tell me more about the history of APL and some of the interesting projects you have worked on.
Keeney: APL was founded in March 1942 as part of a federal government effort to mobilize scientific resources to address wartime challenges. APL was assigned the task of finding a more effective way for ships to defend themselves against enemy air attacks. The laboratory designed, built, and tested a radar proximity fuse (known as the VT fuse) that significantly increased the effectiveness of anti-aircraft shells in the Pacific—and, later, ground artillery during the invasion of Europe. The product of the laboratory’s intense development effort was later judged to be, along with the atomic bomb and radar, one of the three most valuable technology developments of the war.
In fact, this project is widely considered to be the first to use a modern printed circuit board. The success of that mission during the war, lead to future funding and new projects. By the 1960s, the lab was involved in NASA’s space missions as well. I’ve been personally involved in many space missions. Many looked at the Earth’s local environment such as TIMED (thermosphere, ionosphere, mesosphere, energetics and dynamics), STEREO (Solar Terrestrial Relations Observatory), or the Van Allen Probes. Others investigated the sun such as ACE (Advanced Composition Explorer) and the Parker Solar Probe. And still others have investigated other planets such as Messenger (Mercury), Juno (Jupiter), and New Horizons (Pluto). We are currently working on missions to Europa (Europa Clipper), Titan (Dragonfly), and DART (Double Asteroid Redirection Test) to divert an asteroid. While it is hard for me to pick a favorite, the successful Pluto Flyby by New Horizons nine years after it launched and about 12 years after I helped build the hardware was of particular excitement and pride for me.
Beaulieu: Tell me about the PCB shop in the lab. Please describe how it is set up.
Keeney: Our PCB fabrication shop is about eight people working a day shift, so everyone does multiple jobs. Our CAM people also run the electrical tester and the drill. Our innerlayer engineer also runs the AOI and the plating line. You get the idea. It’s great to be involved in so many areas, but you get pulled in different directions, especially when someone is on vacation. As a result, members of our team are often involved in program meetings as well, so we really get to see the results of our work.
Our assembly area has about 25 engineers and technicians and again, the work is diverse. We do both tin-lead and lead-free work. In addition to PCBA, we also do cables, harnesses, and chassis work. We also do a lot of staking and coating as it is required for a lot of our customers. We have a good amount of equipment, but the focus is on precision and measurements, not pure speed.
Beaulieu: What type of people are on your team?
Keeney: In general, it is about a 50/50 mix of degreed engineers and technicians. That said, our engineers do a lot of hands-on work. So, they will develop an experiment and run it themselves. They are usually running the “production” work as well, while working with the whole team.
Beaulieu: And how do you fit in the PCB industry?
Keeney: We are a captive shop and are focused on providing high reliability circuits for our internal customers. In addition to making the prototypes ourselves, we often get involved in troubleshooting or evaluating other vendors for our programs. There is no substitute to running your own shop to understand the challenges of board designs and fabrication.
Beaulieu: Who are your customers?
Keeney: Our APL customers are ultimately all working on government work, either NASA, the U.S. Navy, or any number of other agencies.
Beaulieu: Do you do any commercial work at all?
Keeney: No, not at all. University affiliated research centers (UARCs), such as APL, are independent, not-for-profit organizations that conduct essential research, development, and systems engineering to support national security needs. The centers serve strategic national priorities, free from conflicts of interest or competition with commercial industry. Collaboration with leading research universities allows these organizations to provide the U.S. government with access to our nation’s most highly skilled scientists, engineers, and analysts to tackle vital national security and scientific challenges.
Beaulieu: How do you work with the rest of the university?
Keeney: APL can collaborate with our Johns Hopkins colleagues at the university and Johns Hopkins Medicine on various projects. In my area, we don’t do that collaboration directly very much, though our colleagues we’re working with may be.
Beaulieu: What do you see is the future technology of PCB technology going forward?
Keeney: Electronics certainly aren’t going away anytime soon. When I started in the industry, we were making MCM-D on silicon substrates, and they were going to replace all PCBs. As is often the case, that was exaggerated. I expect that 3D printed electronics will become increasingly popular for certain applications and designs, but I expect traditional boards, albeit with increasingly smaller geometries, will continue to be a major product.
Beaulieu: Allen, I know you’re a very busy guy, so I really appreciate you taking the time to talk to me today.
Keeney: No problem, Dan. My pleasure.
Suggested Items
NEPCON ASIA 2025: Innovating Smart Manufacturing Ecosystems and Bridging Global Opportunities
07/11/2025 | PRNewswireTaking place from October 28 to 30, 2025 at the Shenzhen World Exhibition & Convention Center (Bao'an), NEPCON ASIA is the premier platform to discover the latest technologies and market trends, connect with new suppliers and products, and explore potential partnerships and distribution opportunities.
Mycronic Delivers Strong Q2 Performance and Raises 2025 Outlook to SEK 7.5 Billion
07/11/2025 | MycronicMycronic reported a 35% increase in Q2 net sales and a 27% EBIT margin, prompting an upward revision of its full-year 2025 revenue forecast to SEK 7.5 billion.
Kitron Reports Strengthening Momentum in Q2 2025
07/10/2025 | KitronKitron reported solid quarterly sales and profits, particularly driven by the Defence & Aerospace market sector.
Seeing a Future in Mexico
07/09/2025 | Michelle Te, I-Connect007The Global Electronics Association (formerly known as IPC) has been instrumental in fostering a partnership with Guanajuato, a state north of Mexico City with 12 industrial clusters and close to 150 companies involved in electronics. This past spring, Alejandro Hernández, the undersecretary for investment promotion in Guanajuato, attended IPC APEX EXPO 2025 at the invitation of IPC Mexico Director Lorena Villanueva, where he met with several companies to discuss the opportunities available in Mexico. He is inviting electronics-related companies seeking long-term investment in a centrally located area with access to highways, railways, and ports.
Webinar Review: A Global Trade and Economy in Flux
07/09/2025 | I-Connect007 Editorial TeamIn a July 8 webinar, Global Electronics Association Chief Economist Shawn DuBravac provided a comprehensive analysis of the evolving international trade environment, its implications for inflation, monetary policy, and labor dynamics, and a sober assessment of market valuations. In “Navigating a Shifting Landscape” DuBravac painted a picture of a global economy in flux, where shifting trade alliances and tariff structures are redrawing the supply chain map and influencing the broader economic landscape, while also conveying an overall bullish market outlook.