-
- News
- Books
Featured Books
- pcb007 Magazine
Latest Issues
Current IssueInventing the Future with SEL
Two years after launching its state-of-the-art PCB facility, SEL shares lessons in vision, execution, and innovation, plus insights from industry icons and technology leaders shaping the future of PCB fabrication.
Sales: From Pitch to PO
From the first cold call to finally receiving that first purchase order, the July PCB007 Magazine breaks down some critical parts of the sales stack. To up your sales game, read on!
The Hole Truth: Via Integrity in an HDI World
From the drilled hole to registration across multiple sequential lamination cycles, to the quality of your copper plating, via reliability in an HDI world is becoming an ever-greater challenge. This month we look at “The Hole Truth,” from creating the “perfect” via to how you can assure via quality and reliability, the first time, every time.
- Articles
- Columns
- Links
- Media kit
||| MENU - pcb007 Magazine
Estimated reading time: 4 minutes
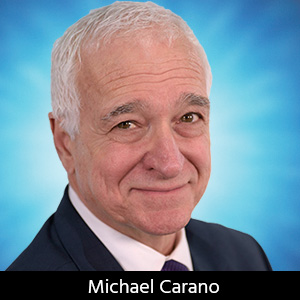
Contact Columnist Form
Trouble in Your Tank: Plating Anomalies and Defects, Part 2
Introduction
One of the most difficult things about troubleshooting PCB defects is getting to and understanding the root cause of defects. Many of these defects can have multiple origins, and many may not manifest themselves in the process where the defect occurred. Thus are the perils of jumping to conclusions about the defect.
Often, I get involved in solving technical issues and the engineer at the board fabricator or OEM calls the defect an “anomaly.” Not really a good idea to go off trivializing the purported anomaly. Failure to understand the true genesis of the defect will lead to incorrect remedies to these issues. I will now present some of these defects and the possible remedies.
Copper Plating Separation
The common complaint one hears is “the copper plating is peeling.” Okay, but where? From the surface or from within the via? Did one perform a proper microsection? Is there an actual separation or is it debris lodged between the substrate and plating copper? And is the separation between the electroless copper and the electrolytic copper, or is it the electroless copper from the base copper? How often does this problem continue due to an inability to get to the root cause? These are the questions one must answer in order to work properly. Figure 1 shows a real example of a blistered or peeling deposit. The question is, what is the actual separation? Is it really a loss of adhesion of the plated deposit to the substrate or is it an inclusion of some sort? How about debris, drill dust, or dry film chips?
In this situation, there could be debris on the surface of the copper foil or residues left behind from insufficient surface preparation or problems in developing the photoresist. In addition, these separations may be caused by drill dust due to poor vacuum draw in the drilling operation. The cross-section in Figure 2 depicts another issue. Is this a plating blister or separation? Or another type of defect?
Is the genesis of the bulging copper anything to be concerned with? Thinking this through a bit, there are a few points to consider. First, it is possible that during the electroless copper process, the copper deposit blistered or separated in mid-cycle. This can happen for several reasons:
- Excessive plating rate of the electroless copper
- Highly stressed copper deposit
- Laminate/resin either has smear remaining or hole wall not sufficiently micro-roughened from the desmear/etchback process
- Possibility of drill dust/debris in via
Now the question is, where is the origin of the blister? The electrolytic copper has been applied, apparently encapsulating the blistered deposit. There have been past occasions such as this described above whereby the fabricator will say all is okay with this since the blister has been covered by the electrodeposited copper. This, of course, is wrong. A blister can fracture or break off in mid-stream plating and cause at the very least a voided via.
So, don’t confuse a blistered deposit that fractures or breaks away with another defect known as hole wall pullaway (HWPA).
Hole Wall Pullaway (HWPA)
While several of the root causes of HWPA apply as well to a blistered copper deposit, there are significant differences. HWPA is a loss of adhesion of the plated deposit from the hole wall surfaces (Figure 3).
A more typical example of HWPA is depicted in Figure 3. The deposit pulled away from the hole wall but did not fracture or flake off. Nonetheless, this is a defect and must be remedied. The root cause of HWPA is very similar to those that lead to flaking and blistering. I consider this at the very least a “process indicator.” This means that the desmear and metallization processes need attention. Of course, if the hole wall pullaway causes a violation of hole wall minimum diameter or leads to other violations in hole diameter dimensional requirements, then this is a cause of concern and will result in non-conformance.
So, one is dealing with the origin of the blister or peeling deposit prior to electrolytic copper plating. Table 1 lists the most common causes for this type of defect.
A precautionary note: Don’t confuse HWPA with resin recession (Figure 4). Resin recession is a material-related issue where the resin has recessed or shrunk back away from the plating. This is evident generally after thermal stress. According to the IPC 600 H, resin recession is permissible.
I am a true believer in the inter-relatedness of processes and the origin of process-related defects. It is helpful to keep a few things in mind when troubleshooting a process issue. To be successful at troubleshooting a problem, common sense usually applies. Basically, one must first:
- Identify the problem or problems (be as specific as possible)
- Determine possible causes (look for links to those other less obvious processes)
- Methods and procedures to test to see which causes apply
- Test the assumptions
- Implement corrective action
While this sounds like an oversimplification, this approach is required to properly identify and attack the problem at hand. A structured routine is really what is required. Remember the most critical success factor is being able to get to the root cause of the problem. Stop the finger pointing and get the different process teams to work together.
This column originally appeared in the December issue of PCB007 Magazine.
More Columns from Trouble in Your Tank
Trouble in Your Tank: Metallizing Flexible Circuit Materials—Mitigating Deposit StressTrouble in Your Tank: Can You Drill the Perfect Hole?
Trouble in Your Tank: Yield Improvement and Reliability
Trouble in Your Tank: Causes of Plating Voids, Pre-electroless Copper
Trouble in Your Tank: Organic Addition Agents in Electrolytic Copper Plating
Trouble in Your Tank: Interconnect Defect—The Three Degrees of Separation
Trouble in Your Tank: Things You Can Do for Better Wet Process Control
Trouble in Your Tank: Processes to Support IC Substrates and Advanced Packaging, Part 5