-
-
News
News Highlights
- Books
Featured Books
- pcb007 Magazine
Latest Issues
Current IssueThe Hole Truth: Via Integrity in an HDI World
From the drilled hole to registration across multiple sequential lamination cycles, to the quality of your copper plating, via reliability in an HDI world is becoming an ever-greater challenge. This month we look at “The Hole Truth,” from creating the “perfect” via to how you can assure via quality and reliability, the first time, every time.
In Pursuit of Perfection: Defect Reduction
For bare PCB board fabrication, defect reduction is a critical aspect of a company's bottom line profitability. In this issue, we examine how imaging, etching, and plating processes can provide information and insight into reducing defects and increasing yields.
Voices of the Industry
We take the pulse of the PCB industry by sharing insights from leading fabricators and suppliers in this month's issue. We've gathered their thoughts on the new U.S. administration, spending, the war in Ukraine, and their most pressing needs. It’s an eye-opening and enlightening look behind the curtain.
- Articles
- Columns
- Links
- Media kit
||| MENU - pcb007 Magazine
A Tour of the New Isola Factory: Investing in North America
December 23, 2021 | Barry Matties, I-Connect007Estimated reading time: 5 minutes
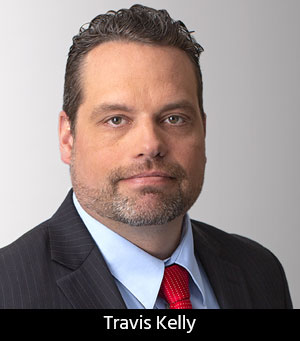
I recently toured Isola’s new 118,000-square-foot low-volume, high-mix manufacturing facility in Chandler, Arizona. The facility’s construction began in 2020 and, like many building projects, was delayed because of the COVID-19 pandemic. Building a new factory during the pandemic was certainly a challenge but the team persevered and the new greenfield facility is now operating to meet the needs of the North American market.
During the tour, I met with Travis Kelly, Ed Kelley, Sean Mirshafiei, Jenny Inocencio, and Walt Niziolek. We covered a range of topics, including lab operations, hiring, the supply chain, R&D, and the concept of the new facility. The factory was designed to extensively utilize automation to improve efficiencies and, as Travis Kelly stated, “to de-risk the labor shortage issue.” As we walked through the facility, it was clear that automation efficiencies were in action as material moved from one process to the next with well-orchestrated choreography.
However, automation does not handle every step in the process. There is a vibrant workforce, and their contributions are highly valued. The following are excerpts from this wide-ranging, daylong tour.
Barry Matties: Travis, in our past interviews we talked a lot about your commitment to a strong culture. This new facility is a positive reflection of that, for sure.
Travis Kelly: Yes. We spend a lot of time showing our employees that we care because obviously they are the most valuable resource at Isola. We want to provide a nice environment. We’re always doing new things that reinforce to our employees that they are appreciated. The employees really like it and understand that we care about them.
Matties: How does this new lab compare to your previous facility?
Ed Kelley: In our previous building, it was mostly a manufacturing area, so we had to squeeze the R&D labs into that building. This new building was designed to specifically allocate space for R&D purposes.
Matties: What is the R&D team focused on now?
Ed Kelley: Historically, a lot of laminate suppliers relied on outside suppliers of resins; we continue to do so, but we’re also looking at tailoring certain polymers for our own purposes. Many of the resins we buy can be used in all sorts of applications. We might want to take some of these commercially available resins and formulate them with something that we’ve developed to give us some unique properties specific to our applications. So, we are doing some of our own polymer synthesis work which is supported by equipment such as our nuclear magnetic resonance (NMR) unit.
Much of our product development work today is focused around 5G and automotive market needs, where electrical, thermal, and CAF resistance properties are critical. With 5G, of course, every component of the product is critical—the resin system, the glass cloth that’s reinforcing it, as well as copper foils. We are very focused on combining these raw materials in ways that meet the OEMs’ requirements while also providing a product that is as easy to use as possible for our PCB manufacturing customers.
Matties: What about halogen-free products?
Ed Kelley: Historically, Isola hasn’t had many halogen-free products; that’s been a more recent focus. If you look at the wired telecom space, for example, there are needs in different loss segments, and therefore different levels of electrical performance for our products. We have a complete portfolio of the non-halogen-free materials, and now we’re looking at filling in the halogen-free offering. Very soon we will be introducing an extremely low loss product called TerraGreen 400G, which is also halogen-free.
As these extremely low-loss materials are more costly, we are seeing an increase in hybrid PCB stackups where PCB designers use the extremely low loss materials in critical layers and use less expensive materials in other layers. Since we want to keep the whole stackup halogen-free, we need to have halogen-free products that have different loss characteristics. Much of our recent work has been on filling in those halogen-free segments.
Matties: What customer interactions do you have here with the lab? Are they coming in, and what are their needs?
Ed Kelley: There were a lot more coming in prior to COVID, but we still do a lot of testing. For example, we have a Technical Program Management (TPM) group. Some of our applications engineering support people who are customer-facing will help, not just with evaluations of our materials, but also in looking at PCB designs and recommending stackups and process parameters. We take a very holistic view. It’s easy to get focused on just getting the best electrical performance, for example, and lose sight of the other requirements of our product—thermal reliability, CAF resistance, etc. At each stage of our development process, we make sure we’re checking all the boxes of requirements, not just, say, electrical performance.
Matties: One of those areas tends to be more important to the industry at any given time, I would think.
Ed Kelley: Yes. 5G, for example, is all about low loss. Everybody wants the best possible electrical performance, which has driven the use of very smooth copper foils that have quickly changed customer specifications on peel strength. The question becomes, if the right measure is not peel strength, how do you assess the reliability? While the focus is certainly on the electrical performance, it creates other concerns. With these very smooth copper foils, the risk of delamination in assembly thermal cycles can increase, and we have also seen cases where CAF growth occurs at the bond line between etched laminate surface and the prepreg bonded to it. So, we work very closely with our suppliers to make sure that the copper profiles and treatments match well with our dielectric material, and we follow a strict test protocol to make sure we are getting reliable adhesion and excellent CAF resistance even though it is the electrical performance that is driving the industry requirement.
To read this entire conversation, which appeared in the December 2021 issue of PCB007 Magazine, click here.
Suggested Items
The Evolution of Picosecond Laser Drilling
06/19/2025 | Marcy LaRont, PCB007 MagazineIs it hard to imagine a single laser pulse reduced not only from nanoseconds to picoseconds in its pulse duration, but even to femtoseconds? Well, buckle up because it seems we are there. In this interview, Dr. Stefan Rung, technical director of laser machines at Schmoll Maschinen GmbH, traces the technology trajectory of the laser drill from the CO2 laser to cutting-edge picosecond and hybrid laser drilling systems, highlighting the benefits and limitations of each method, and demonstrating how laser innovations are shaping the future of PCB fabrication.
Day 2: More Cutting-edge Insights at the EIPC Summer Conference
06/18/2025 | Pete Starkey, I-Connect007The European Institute for the PCB Community (EIPC) summer conference took place this year in Edinburgh, Scotland, June 3-4. This is the third of three articles on the conference. The other two cover Day 1’s sessions and the opening keynote speech. Below is a recap of the second day’s sessions.
Day 1: Cutting Edge Insights at the EIPC Summer Conference
06/17/2025 | Pete Starkey, I-Connect007The European Institute for the PCB Community (EIPC) Summer Conference took place this year in Edinburgh, Scotland, June 3-4. This is the second of three articles on the conference. The other two cover the keynote speeches and Day 2 of the technical conference. Below is a recap of the first day’s sessions.
Preventing Surface Prep Defects and Ensuring Reliability
06/10/2025 | Marcy LaRont, PCB007 MagazineIn printed circuit board (PCB) fabrication, surface preparation is a critical process that ensures strong adhesion, reliable plating, and long-term product performance. Without proper surface treatment, manufacturers may encounter defects such as delamination, poor solder mask adhesion, and plating failures. This article examines key surface preparation techniques, common defects resulting from improper processes, and real-world case studies that illustrate best practices.
RF PCB Design Tips and Tricks
05/08/2025 | Cherie Litson, EPTAC MIT CID/CID+There are many great books, videos, and information online about designing PCBs for RF circuits. A few of my favorite RF sources are Hans Rosenberg, Stephen Chavez, and Rick Hartley, but there are many more. These PCB design engineers have a very good perspective on what it takes to take an RF design from schematic concept to PCB layout.