Testing Flexible Circuit Assemblies
January 18, 2022 | Andy Shaughnessy, Design007 MagazineEstimated reading time: 3 minutes
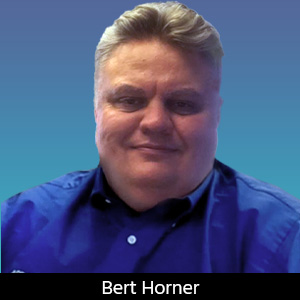
I recently spoke with Bert Horner of the Test Connection Inc., about the current state of flex and rigid-flex assembly testing. He explained some of the differences between testing flex and rigid PCBs, the requirements for testing specialties such as high-voltage flex, and the added demands of handling flexible circuits.
Andy Shaughnessy: Bert, tell us about your company and the kinds of test equipment you’ve developed for flexible and rigid-flex circuits. I understand you also provide test services too; do you offer testing for flex?
Bert Horner: The Test Connection Inc., is a full services test engineering and test service that offers different test solutions to test rigid and rigid flex circuits. For prototype or lower volume assemblies, we have flying probe and boundary scan solutions and for the production testing, we have in-circuit test and functional test solutions from partners like Teradyne, Keysight, and National Instruments. TTCI works with fixture partners to offer custom in-house solutions to support and access these challenging assemblies.
Shaughnessy: What are the most common tests for flexible circuit assemblies as well as the biggest challenges? Do high-voltage flexible circuits require a different set of tests than the rest?
Horner: For flying probe testing (FPT), in-circuit testing (ICT) and functional test (FT), the biggest challenge is the tooling for testing the assembly. For the FPT, the handling of the unit under test (UUT) is one of the biggest challenges. This can still be a challenge if the assembly is thin and flimsy, so tooling could still be required. If ICT and FT are done on a fixture or bed-of-nails (BoN), we don’t want to introduce stress to the UUT, so “zero flex” fixturing with finite element analysis (FEA) and strain gauge might be needed, which also adds time and cost. In FT, we see that in high-voltage testing, the biggest challenge is making sure the equipment that will be testing assembly can handle the proper testing requirements. This is about the same set-up as a rigid board, but we haven’t seen too many applications that have this as a requirement.
Shaughnessy: What are some of the biggest differences between testing a flexible circuit and a traditional rigid PCB?
Horner: The physical handling is the biggest challenge in testing flex or rigid-flex circuitry. We often have to develop a custom carrier or handling fixture to test flex or rigid-flex assemblies to help with stability and support.
Shaughnessy: We’ve seen flex and rigid-flex explode in the last decade, and now flex can be found in many household and handheld devices. What trends are you seeing in the world of flex?
Horner: Test access is more of a challenge with accessing the test assemblies through connectors and SMT device “toes” of the solder joints with the assemblies going into two completely different directions. The wearable, handheld, and space applications are getting smaller, but the defense backplanes are in some cases getting larger.
Shaughnessy: How much of your job involves educating new customers about flex and testing?
Horner: We are not doing much with educating the customer on how they want to test flex circuitry, but rather showing them strengths and weaknesses in the test solutions they are choosing or that they have available to test their assemblies. If we are looking at multiple test and inspection tools to get the most coverage on these assemblies, the education becomes about what is best for manufacturing. We both learn preferences of tools that are available.
Shaughnessy: Is there anything else you’d like to add?
Horner: There are more similarities of testing flex circuitry and conventional rigid circuitry, the access, and the handling are where we see the challenge.
Shaughnessy: Thanks for your time, Bert.
Horner: Thank you for the opportunity, Andy.
This interview originally appeared in the January 2022 issue of Design007 Magazine.
Testimonial
"We’re proud to call I-Connect007 a trusted partner. Their innovative approach and industry insight made our podcast collaboration a success by connecting us with the right audience and delivering real results."
Julia McCaffrey - NCAB GroupSuggested Items
Indium Corporation Promotes Two Leaders in EMEA (Europe, Middle East, and Africa) Markets
08/05/2025 | Indium CorporationWith its commitment to innovation and growth through employee development, Indium Corporation today announced the promotions of Andy Seager to Associate Director, Continental Sales (EMEA), and Karthik Vijay to Senior Technical Manager (EMEA). These advancements reflect their contributions to the company’s continued innovative efforts with customers across Europe, the Middle East, and Africa (EMEA).
MacDermid Alpha Electronics Solutions Unveils Unified Global Website to Deepen Customer, Talent, and Stakeholder Engagement
07/31/2025 | MacDermid Alpha Electronics SolutionsMacDermid Alpha Electronics Solutions, the electronics business of Elements Solutions Inc, today launched macdermidalpha.com - a unified global website built to deepen digital engagement. The launch marks a significant milestone in the business’ ongoing commitment to delivering more meaningful, interactive, and impactful experiences for its customers, talent, and stakeholders worldwide.
KOKI to Showcase Analytical Services and New HF1200 Solder Paste at SMTA Guadalajara 2025
07/31/2025 | KOKIKOKI, a global leader in advanced soldering materials and process optimization services, will exhibit at the SMTA Guadalajara Expo & Tech Forum, taking place September 17 & 18, 2025 at Expo Guadalajara, Salón Jalisco Halls D & E in Guadalajara, Mexico.
Weller Tools Supports Future Talent with Exclusive Donation to SMTA Michigan Student Soldering Competition
07/23/2025 | Weller ToolsWeller Tools, the industry leader in hand soldering solutions, is proud to announce its support of the upcoming SMTA Michigan Expo & Tech Forum by donating a limited-edition 80th Anniversary Black Soldering Set to the event’s student soldering competition.
Koh Young Appoints Tom Hattori as President of Koh Young Japan
07/21/2025 | Koh YoungKoh Young Technology, the global leader in True 3D measurement-based inspection solutions, announced the appointment of Tom Hattori as President of Koh Young Japan (JKY).