-
- News
- Books
Featured Books
- pcb007 Magazine
Latest Issues
Current IssueInventing the Future with SEL
Two years after launching its state-of-the-art PCB facility, SEL shares lessons in vision, execution, and innovation, plus insights from industry icons and technology leaders shaping the future of PCB fabrication.
Sales: From Pitch to PO
From the first cold call to finally receiving that first purchase order, the July PCB007 Magazine breaks down some critical parts of the sales stack. To up your sales game, read on!
The Hole Truth: Via Integrity in an HDI World
From the drilled hole to registration across multiple sequential lamination cycles, to the quality of your copper plating, via reliability in an HDI world is becoming an ever-greater challenge. This month we look at “The Hole Truth,” from creating the “perfect” via to how you can assure via quality and reliability, the first time, every time.
- Articles
- Columns
- Links
- Media kit
||| MENU - pcb007 Magazine
Estimated reading time: 5 minutes
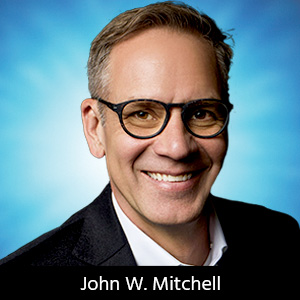
One World, One Industry: Working Together to Address Workforce Challenges
While the conflict in Ukraine has captured headlines for the past several weeks, the challenges facing companies on the workforce front have not abated. When I speak with executives around the world, they are singing the same song in two-part harmony: supply chain and people.
Let’s talk a little about the people challenges that are keeping management up many nights. Even though we say there is a workforce problem, it is not just one problem. This obstacle is multifaceted.
Some of the Challenges
Let’s first examine the factory floor. There are several facets to this challenge. First, there is the challenge of finding people, any people, who are willing to work in the industry. It is not that the electronics manufacturing industry isn’t attractive; it is that, due to the downward pressure on electronics, the operator roles don’t tend to pay as much as the Amazon factory down the road. This kind of competition makes it very difficult to find people. Our industry is not the only industry looking for people; practically every industry is looking and trying to make deals to woo employees into their locations. Some of these enticements, such as providing tuition toward a degree if you come to work for their factory, are things that have never been considered at this level of employment.
The other challenge that has come about due to COVID-19 is that of the virtual workforce. During the pandemic, many of the operators were able to experience getting paid while not going to the factory. This presented a different way of life that had not been considered previously. At the operator and inspector levels, this really isn’t an option. It is almost impossible to build, inspect, test, and verify the electronics coming off the line without being present in the factory. With the ever-changing technology being built and being used to build, the skill set of the workforce in the factory needs to be continually advanced to meet the needs of the business.
The workforce shortage is not limited to just the factory. The dearth of engineers has continued for over a decade, making it critical for us to get engineers aware and interested in the challenging and rewarding career path of electronics manufacturing. The IPC Education Foundation (ipcef.org) is striving diligently to do this at the college level with competitions, awareness campaigns, chapters, and interactions with local electronics shops to help engineers and technicians gain awareness of the interesting and exciting work that is happening, in many cases, right under their noses.
In addition, we are starting to see executives move around the industry as well. The challenges facing operators, technicians, and engineers have escalated in discussion over the past six months, and now seems to be affecting executive positions. As the “Great Resignation” envelops much of the world, opportunities are abounding, and with opportunities comes movement. This is a relatively new phenomenon. These movements are happening both within the industry and with people moving outside of the industry.
Okay, enough of the doom and gloom. We know we have challenges. What are we to do about it?
What Should Be Done?
Let’s talk about potential solutions to each category mentioned above: factory line, technicians, engineers, and executives.
Factory Line
First, we must do what we are good at—we need to innovate. We need to look for people in different ways and in different spaces. I have seen job fairs work to good effect. Now, I know you’re thinking that job fairs are old school. But these latest job fairs are bringing in people, providing tours of the facility, teaching them about the company, interviewing them, and offering them jobs to start as soon as the next Monday—all in the same morning. That is a very different job fair from what we have seen in the past. Another innovation is to look in places we haven’t looked before. I have seen groups approaching families with graduating seniors—not to hire the graduate, but to make an offer to the parent who will no longer have a reason to stay at home. Other innovative sources include the military, prisons, high schools (no, I am not equating high schools to prisons), etc. Look in places where most people don’t look. If you are at a restaurant, for example, and your server is competent, invite them to come to your factory for an interview. Finally, utilize modern skills training programs like the Electronics Assembly for Operators (AEO) and Wiring Harness for Operators (WHO) to bring new talent off the bench and onto the line within hours instead of weeks.
Stay tuned for a new industry-developed program on the inspector front coming later this year from IPC to help on this increasingly needed (especially with automation increasing) area of expertise.
Engineering
I have already mentioned the efforts of the IPC Education Foundation. If you really want to leverage that, I urge you to get involved. You will find internship opportunities and first-hand interactions to give you a leg up on bringing new graduates into your organization. One other solution that IPC has developed along with the industry, to ensure that new engineers are ready to work in the factory, is the Electronics for Assembly Engineers course. This online course brings novice engineers rapidly up to speed on all the basics of electronics manufacturing. This course is ideal is for new engineers who haven’t had enough exposure to the specifics of our industry. Now they can get that at their own pace and in a consistent manner.
Executives
My best suggestion is one that has been used to great effect in some companies. Just like other industries are looking to poach from our industry, we can look at new sources to pull in from other industries. This opens a whole new pool of people to consider. There are many kinds of manufacturing experts who can translate what they know and have done into our industry, whether at the general manager level, supply chain, procurement, human resources, development, engineering management, or financial. The added benefit of bringing in someone from outside is that you will also get new ideas and approaches. I call it diversity of thought. This is a competitive advantage and not something to be dismissed lightly.
The workforce challenges will continue. We need to continue to do what we do to solve problems: work together and innovate.
This column originally appeared in the April 2022 issue of PCB007 Magazine.
More Columns from One World, One Industry
One World, One Industry: IPC APEX EXPO 2025 Marks a Special Anniversary YearOne World, One Industry: Mapping the Future of the Electronics Workforce
One World, One Industry: Mastering Technology Prognostication
One World, One Industry: To Thrive, Surround Yourself with Good People
One World, One Industry: Sustainability Challenges—A Collaborative Approach
One World, One Industry: What’s Next Becomes Now at IPC APEX EXPO 2024
One World, One Industry: ‘Blocking and Tackling’ During Tough Economic Times
One World, One Industry: Developing Your Team to Become Great Implementors