University of Illinois Researchers Create Low-cost High-Yield Plastic Microprocessors
June 28, 2022 | University of IllinoisEstimated reading time: 2 minutes
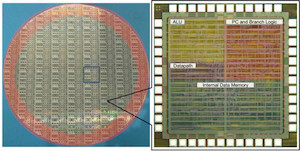
Supercomputers can crunch massive data sets and give us insights into the wonders of the universe. But a sub-penny microprocessor that flexes to fit on a beer bottle and tells you whether your brew is still cold? Creating that technology has been surprisingly more difficult to achieve.
Recently, a team of researchers from the University of Illinois Urbana-Champaign said: hold my beer. Working with British flexible electronics manufacturer PragmatIC Semiconductor, the researchers developed the first commercially viable flexible plastic microprocessor chips, called FlexiCores, that can be manufactured at scale for less than a penny per unit.
The new processors could help even everyday objects become “smart.”
“For example, you could put processors on bandages to detect whether a wound is healing, or add them to consumer goods packaging to track progress along the supply chain,” said Rakesh Kumar, a professor of electrical and computer engineering and researcher in the Coordinated Science Lab at UIUC. “The challenge has been creating a processor that can be both cheaply produced and flexible enough to fit snugly even against uneven surfaces on our body, packages, or beer bottles.”
Researchers solved the problem in part by turning to plastic, instead of silicon, as the basis of the chips. Silicon is the industry standard for semiconductors, but it has inherent limitations due to its cost and its inflexibility. Kumar and his team built the FlexiCores on thin-film transistors made with the semiconductor indium gallium zinc oxide (IGZO), which works even when bent and is compatible with plastic.
The chip design was equally important in the pursuit of sub-penny plastic processors: in this case, less was more.
“Even the simplest modern chips are overkill for what we need them to be able to do for our target applications,” Kumar said. “Our FlexiCore chips look like 1970s silicon chips because we greatly reduced the number of components on them through careful design.”
The UIUC team tested 4-bit and 8-bit processors and found that the 4-bit processors produced a yield of 81%, which is high enough for the chips to be manufactured for less than a penny each. (“Yield” refers to the percentage of chips that work.) The 4-bit processor has 2,104 devices (transistors and resistors), which is far less than the 56,000-plus devices on a plastic ARM processor that debuted last year with much fanfare, but hasn’t been shown to be manufacturable at scale and does not run multiple programs, as FlexiCore can.
The low gate count in FlexiCores improves yield and reduces the “bill of materials”—the amount of material needed to produce each chip.
Kumar noted that the semiconductor industry has mostly been concerned with improving performance and power efficiency. With this research, he and his team are pioneering flexible electronics with new application frontiers. The research will be presented at the International Symposium on Computer Architecture later this month.
“These chips combine the flexibility and cost benefits of plastic technology with the high yield and low bill of materials enabled by our architecture,” he said. “It will be interesting to see where we go from here.”
Suggested Items
Symposium Review: Qnity, DuPont, and Insulectro Forge Ahead with Advanced Materials
07/02/2025 | Barb Hockaday, I-Connect007In a dynamic and informative Innovation Symposium hosted live and on Zoom on June 25, 2025, representatives from Qnity (formerly DuPont Electronics), DuPont, and Insulectro discussed the evolving landscape of flexible circuit materials. From strategic corporate changes to cutting-edge polymer films, the session offered deep insight into design challenges, reliability, and next-gen solutions shaping the electronics industry.
Flexible Electronics Market to Reach $66.9 Billion by 2032, Growing at a CAGR of 9.2% from 2025
06/30/2025 | PRNewswireThe flexible electronics market is projected to reach $66.9 billion by 2032, up from an estimated $38.4 billion in 2025, growing at a robust CAGR of 9.2% during the forecast period.
All Flex Solutions Upgrades Lamination Layup
06/22/2025 | All Flex SolutionsAll Flex Solutions has invested in Ulrich Rotte lamination layup stations in their rigid flex layup area. The Ulrich Rotte stations automate the layup process by handling the lamination plates, which are heavy, and sequencing the layup process for the operators.
SEMI FlexTech Solicits Proposals for Advancing the Future of Flexible Hybrid Electronics
06/18/2025 | SEMIFlexTech, a SEMI Technology Community, today issued a Request for Proposals (RFP) to advance flexible hybrid electronics (FHE) technologies, including the development of advanced materials and additive processing.
Roll-to-Roll Technologies for Flexible Devices Set to Grow at 11.5% CAGR
06/11/2025 | GlobeNewswireAccording to the latest study from BCC Research, the “Global Markets for Roll-to-Roll Technologies for Flexible Devices” is expected to reach $69.8 billion by the end of 2029 at a compound annual growth rate (CAGR) of 11.5% from 2024 to 2029.