-
-
News
News Highlights
- Books
Featured Books
- pcb007 Magazine
Latest Issues
Current IssueThe Hole Truth: Via Integrity in an HDI World
From the drilled hole to registration across multiple sequential lamination cycles, to the quality of your copper plating, via reliability in an HDI world is becoming an ever-greater challenge. This month we look at “The Hole Truth,” from creating the “perfect” via to how you can assure via quality and reliability, the first time, every time.
In Pursuit of Perfection: Defect Reduction
For bare PCB board fabrication, defect reduction is a critical aspect of a company's bottom line profitability. In this issue, we examine how imaging, etching, and plating processes can provide information and insight into reducing defects and increasing yields.
Voices of the Industry
We take the pulse of the PCB industry by sharing insights from leading fabricators and suppliers in this month's issue. We've gathered their thoughts on the new U.S. administration, spending, the war in Ukraine, and their most pressing needs. It’s an eye-opening and enlightening look behind the curtain.
- Articles
- Columns
- Links
- Media kit
||| MENU - pcb007 Magazine
Estimated reading time: 9 minutes
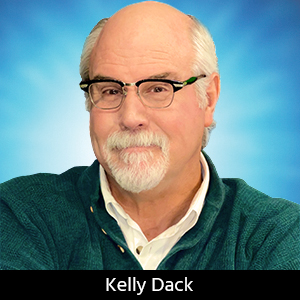
Contact Columnist Form
Target Condition: Practical Packaging Density in PCB Design
Have you ever sat in an overcrowded meeting room? For me, this is never fun. I think of elbows knocking against others and poor ventilation. My performance degrades when I’m overcrowded. Conversely, when I sit in meetings within oversized conference hall rooms containing too much empty volume, I feel uncomfortable. I can’t help being distracted by the hollow, reverberating sounds as well as thinking about the costs and waste of resources. To engage effectively, I need to be closer to my fellow attendees and the presenter.
PCB Design Agoraphobia
Just as I tend to exhibit discomfort in oversized conference halls and meeting rooms, I self-diagnose as agoraphobic when it comes to entering PCB layouts full of wasted space. Mechanical constraints which utilize the printed circuit board substrate material as a mechanical or structural “filler” within an electronic product, under-utilizing the material for its intended purpose to support conductive circuitry, grate on me like nails on a chalkboard. I’ve seen an eight-inch, triangular shaped support bracket designed out of 0.093" thick FR-4 laminate material. It was contrived and specified by an uninformed mechanical engineering overachiever who proposed transforming the original sheet metal bracket into a “dual purpose” PCB solution in order to support the electronic engineer’s connector and associated circuitry. The circuit added to this clumsy “printed circuit bracket” monstrosity occupied just over a single square inch and seemed a ghastly waste of resources.
Figure 1: 3D pic of empty boardscape.
I’ve lived through other well-intentioned mechanical engineering efforts to cut assembly costs—without scratching off my skin. Once, an uninformed mechanical engineer proposed a PCB to reduce assembly costs by eliminating connector harnessing between multi-sectioned PCB assembly sets. It did not go well. It involved creating a single piece LED board which could be installed quickly into a machine using only six fasteners—a novel requirement but without consideration of all the materials and processes associated with the design for bare board manufacturability. Each single 19-inch diameter board ring—dubbed “the panel burner”—wasted an entire, oversized panel of copper-clad FR-4 material. The board could only be processed by a custom supplier at the time.
PCB Design Claustrophobia
Sometimes, when our front-end packaging stakeholders seem to be working for “Team Crazy,” their PCB mechanical constraints can send me in an opposite direction. Over many decades we have been watching as electronic components shrink in size. Each new generation of components seems to include a smaller packaging scale which is construed to be good for shrinking products and using less material. But from an actual product design standpoint, electronic products have gone through an identity crisis with regard to packaging size. For example, all that must happen for an electronic product to be rendered obsolete and discontinued is for a competitor to come out with a smaller, more tightly packaged alternative. Industrial designers are kept busy sketching out increasingly smaller electronic products from the outside-in and passing on their concepts to the mechanical engineering teams. Mechanical engineers seem to only re-design their molds and choose higher performance materials to meet the industrial designer’s smaller constraints while electronics packaging engineers and PCB designers are often left scratching their heads trying to select available components and circuitry which can be manufactured to fit within a new, sleek, ergonomic, and attractively small product housing.
There is a classic, ongoing challenge for electronics design stakeholders today. It is commonly attributed to EEs residing at the end of the product design cycle. Creative, responsive, industrial design and mechanical engineering stakeholders are usually well on their way to offering their deliverables well before components can be found and the electronic assembly bill of materials is even finalized. Electronics packaging stakeholders are often faced with pressure to cram their circuitry onto less-than-ideal PCB real estate, robbing process efficiency from every other electronics manufacturing stakeholder involved.
As a PCB design stakeholder, I can’t tell you how many times I’ve created a PCB outline per mechanical specification only to discover there is not enough space for the component footprints to fit on the board. This condition is typically resolved, however, by a quick discussion with the project team that will need to review its whole design process and either make the PCB larger or continue to find smaller parts. We usually won’t see them back for an average of about two weeks, which frees us up to work on other, more practically dense PCB layouts. There is a more difficult condition, however, occurring from time-to-time when the parts within a design layout happen to just barely fit within a specified PCB outline. This PCB design condition is on the hairy edge of “doable.” The parts fit, but will most certainly result in an extremely dense layout with compromised design rules. While this condition is a welcome challenge to any emerging PCB design layout engineer, designs exhibiting extreme density cause me to self-diagnose as claustrophobic. It’s not because I don’t like a challenge. I’ll work overnight as hard as any PCB designer to push and shove design features to intelligently set design rule constraints. But when it comes to compromising on well-established manufacturing proximity constraints, I become anxious. These days, it makes my skin crawl to have to tighten up a tolerance or nudge a trace or component knowing that I’m pushing a systemic problem downstream which may cause a logjam of challenges for my fellow stakeholders.
Over the years there have been many logjams and I have developed special empathy for all the valuable stakeholders in our electronics industry struggling to play a part in a PCB assembly project’s success when DFM considerations are ignored. Dense packaging solutions are not easy. I seriously consider any decision moving a layout from the IPC general design producibility level A to a reduced producibility level C without substantial justification and buy-in from all project stakeholders. Sometimes though, any of us can get caught up in the shimmer of new technology without counting the project costs from a holistic viewpoint.
Feng Shui in PCB Design?
The traditional practice of feng shui claims to use energy forces to harmonize individuals with their surrounding environment. I recall hearing a production floor manager once complain about a dangerously unorganized area of a stockroom, facetiously pointing out that the room was not feng shui. Was he serious? Regardless, I’ve always wondered if there was a place for feng shui in PCB layout. Looking at a printed board assembly from a distance, one can imagine it looks much like a city with components appearing as neatly placed buildings and traces as pristine roads. A well laid out PCBA should provide a feeling of positive energy from the product. I’ve experienced this feeling many times while visiting PCB fabrication or assembly suppliers. The front lobby features an impressive glass cabinet display housing various bare printed boards or full assemblies—examples of their work—and I feel the energy of project stakeholder success. The high-tech examples in these cases radiate the case that the PCB engineering and manufacturing teams in this company have worked together to achieve the satisfaction of their customer and are proud of what they have produced.
But what happens to these designs if a part or material becomes unavailable? The design will no longer be feng shui because it has become “out of balance” and must change. Now what?
Practical Packaging Density, Plus
We see how using an abundance of material to solve a single problem can create other problems. On the other hand, we see efforts to shrink and shave every last scrap of real estate or material can cause adverse effects regarding producibility. We now consider the concept of feng shui in establishing just the right balance of PCB yin and yang to come up with an ideally balanced PCB assembly. Consider the words of Greek philosopher Heraclitus, who is credited with exclaiming: “Change is the only constant.”
Over the past few years, project stakeholders have been faced weekly with rippling pandemic effects causing severely disruptive component and material shortages. The extenuating supply chain challenges are causing perfectly performing board design layouts to require making room for substitute parts which may only be available in larger form factors or less-than-ideal packaging technologies which do not match the “qi”—the vital life force—of the PCB design. Argh! Enough on the philosophies already. What can be done to fix this?
I’ve actually been incorporating a PCB design concept of my own for quite a while. I call it practical packaging density, plus (or PPDP). It’s rather simple.
First, packaging density for electronics has long been considered an essential measurement for determining ease or difficulty of manufacturing, reworking, or even re-designing a product. Packaging density can have a monumental effect on electronic performance. We should strive to start our electronics product design methodology by considering all materials, manufacturing, and performance constraints from the inside out for a product, to establish a practical packaging density for our PCBs. This means that the design layout will be stakeholder friendly and priced right for all project stakeholders, including the customer, throughout its design cycle. This means a project team will have to spend a lot more time on the front end of a project researching availability, manufacturing constraints and, most importantly, dialing design rule settings away from limited IPC class C producibility to achieve the definition of practical packaging density.
However, I’ve met too many designers who are in the habit of calling up a local PCB prototype shop to ask about pushing the shop’s capabilities: How small holes can be drilled, how close copper images can be spaced and etched, and how tight solder mask patterns can be registered. They ask and are typically given minimum producibility requirements. Upon receiving the values, they go right to the design constraint settings in their layout tools and enter the (minimum) values given. This philosophy is counter-productive for all. Designing to minimum manufacturing constraint capability is like continually red lining a running motor. It’s hard on the systems, which are bound to break down.
The final step in the PPDP concept is to incorporate some extra space. To move toward successful packaging design, designers need to reverse thrusters by adding more space and clearance to what is already considered practical. This is the plus in PPDP. It is the plus that will end up helping reduce the domino effect of component placement if your team cannot find drop-in replacements for those components which have gone EOL (end-of-life). It is the plus that will help out that tech who needs just a bit of extra clearance to rework that component. It is the plus that is very minor regarding increasing material costs but can save countless dollars in time and effort in manufacturing, rework, test, and re-redesign.
Regardless of our viewpoints on metaphysics, feng shui, or any unfamiliar cultural traditions involving proximity, energy, crystals, harmonic forces, and even a little “black magic,” it may be surprising for us to realize that creating a holistically successful printed circuit assembly already includes most all these ancient ingredients plus a little bit more.
This column originally appeared in the August 2022 issue of Design007 Magazine.
More Columns from Target Condition
Target Condition: Are Autorouters Friend or Foe?Target Condition: From Dream House to Drill Files
Target Condition: Designing vs. Inventing
Target Condition: ‘Boomer to Zoomer: Do You Copy?’
Target Condition: Advanced Packaging Technologies—Look Before You Leap
Target Condition: My Anti-venom to PCB Cost Adders
Target Condition: Taking the Stand at Your Own Design Review
Target Condition: Designing Unconventional Geometries