-
-
News
News Highlights
- Books
Featured Books
- pcb007 Magazine
Latest Issues
Current IssueThe Hole Truth: Via Integrity in an HDI World
From the drilled hole to registration across multiple sequential lamination cycles, to the quality of your copper plating, via reliability in an HDI world is becoming an ever-greater challenge. This month we look at “The Hole Truth,” from creating the “perfect” via to how you can assure via quality and reliability, the first time, every time.
In Pursuit of Perfection: Defect Reduction
For bare PCB board fabrication, defect reduction is a critical aspect of a company's bottom line profitability. In this issue, we examine how imaging, etching, and plating processes can provide information and insight into reducing defects and increasing yields.
Voices of the Industry
We take the pulse of the PCB industry by sharing insights from leading fabricators and suppliers in this month's issue. We've gathered their thoughts on the new U.S. administration, spending, the war in Ukraine, and their most pressing needs. It’s an eye-opening and enlightening look behind the curtain.
- Articles
- Columns
- Links
- Media kit
||| MENU - pcb007 Magazine
Happy’s Design Tips for Material Conservation
August 25, 2022 | Happy Holden, I-Connect007Estimated reading time: 1 minute
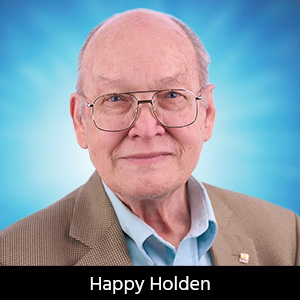
Note: For this issue, Happy Holden provided a range of options for designers who are seeking to conserve materials in their next design. He also offered an example of the relative cost index, or RCI, that he developed at HP exclusively for PCB design. With this RCI, designers can figure out the relative cost of a new design compared to an eight-layer through-hole board.
- Consider making the board thinner; eliminate prepregs
- Design to HDI for smaller board or fewer layers (Figure 1 and Reference 1)
- Design inner layers with 1 to 2 mil smaller traces/spaces
- Swing vias for BGA breakout can reduce layer count
- Nesting and rotation on panels
- Using HDI “skip vias” to eliminate a build-up layer
Consider using new technologies:
- VeCS can reduce layer count (Figure 2 and Reference 2)
- Additive creates more routing per layer and smaller boards
- Switch HDI layers to RCF (RCC)
- Power mesh can yield fewer layers (Reference 3)
- Landless vias on the surface can mean higher routings (Figure 3 and Reference 4)
- Smaller panel peripheral border
- Different panel sizes for higher utilization
- Add-on 0.062" gold fingers as components
- Board replacement for X-outs and repanelization (Reference 5)
- Inkjet solder mask just on traces/pads
Figure 1: Replacement chart for through-hole to HDI with Relative Cost Index. Note: RCI = the relative cost compared to an eight-layer through-hole board (RCI=1.0). DEN = total wiring in inches per square inch (diagonals of equivalent density).
Figure 2: VeCS (Vertical Conductive Structures) is a licensed technology using low-footprint vertical controlled impedance interconnect with low-leakage ground shielding capable of matching interconnect impedance with SE and differential microstrip and striplines. VeCS also provides high-density differential routing solutions in =/< 1.0 mm BGA area. Unique “anti-pad” layers provide a higher cross-section area for power and heat dissipation.
Figure 3: A variety of examples of landless vias on the outer layers of a PCB.
References
- The HDI Handbook, by Happy Holden, et al, BR Publishing, Salem, Oregon, 2009.
- Happy’s TechTalk #1: Vertical Conductive Structures (VeCS), by Happy Holden, PCB007 Magazine, October 2021.
- “Innovative Use of Vias for Density Improvements,” by Happy Holden, The PCB Magazine, November 2016.
- “Against the Density Wall: Landless Vias Might be the Answer,” by Happy Holden, The PCB Magazine, June 2016.
- Happy’s TechTalk #6: Looking at the Process of Repanelization, by Happy Holden, PCB007 Magazine, March 2022.
This article originally appeared in the August issue of Design007 Magazine, here.
Suggested Items
Driving Innovation: Direct Imaging vs. Conventional Exposure
07/01/2025 | Simon Khesin -- Column: Driving InnovationMy first camera used Kodak film. I even experimented with developing photos in the bathroom, though I usually dropped the film off at a Kodak center and received the prints two weeks later, only to discover that some images were out of focus or poorly framed. Today, every smartphone contains a high-quality camera capable of producing stunning images instantly.
Hands-On Demos Now Available for Apollo Seiko’s EF and AF Selective Soldering Lines
06/30/2025 | Apollo SeikoApollo Seiko, a leading innovator in soldering technology, is excited to spotlight its expanded lineup of EF and AF Series Selective Soldering Systems, now available for live demonstrations in its newly dedicated demo room.
Indium Corporation Expert to Present on Automotive and Industrial Solder Bonding Solutions at Global Electronics Association Workshop
06/26/2025 | IndiumIndium Corporation Principal Engineer, Advanced Materials, Andy Mackie, Ph.D., MSc, will deliver a technical presentation on innovative solder bonding solutions for automotive and industrial applications at the Global Electronics A
Fresh PCB Concepts: Assembly Challenges with Micro Components and Standard Solder Mask Practices
06/26/2025 | Team NCAB -- Column: Fresh PCB ConceptsMicro components have redefined what is possible in PCB design. With package sizes like 01005 and 0201 becoming more common in high-density layouts, designers are now expected to pack more performance into smaller spaces than ever before. While these advancements support miniaturization and functionality, they introduce new assembly challenges, particularly with traditional solder mask and legend application processes.
Knocking Down the Bone Pile: Tin Whisker Mitigation in Aerospace Applications, Part 3
06/25/2025 | Nash Bell -- Column: Knocking Down the Bone PileTin whiskers are slender, hair-like metallic growths that can develop on the surface of tin-plated electronic components. Typically measuring a few micrometers in diameter and growing several millimeters in length, they form through an electrochemical process influenced by environmental factors such as temperature variations, mechanical or compressive stress, and the aging of solder alloys.