-
-
News
News Highlights
- Books
Featured Books
- pcb007 Magazine
Latest Issues
Current IssueThe Hole Truth: Via Integrity in an HDI World
From the drilled hole to registration across multiple sequential lamination cycles, to the quality of your copper plating, via reliability in an HDI world is becoming an ever-greater challenge. This month we look at “The Hole Truth,” from creating the “perfect” via to how you can assure via quality and reliability, the first time, every time.
In Pursuit of Perfection: Defect Reduction
For bare PCB board fabrication, defect reduction is a critical aspect of a company's bottom line profitability. In this issue, we examine how imaging, etching, and plating processes can provide information and insight into reducing defects and increasing yields.
Voices of the Industry
We take the pulse of the PCB industry by sharing insights from leading fabricators and suppliers in this month's issue. We've gathered their thoughts on the new U.S. administration, spending, the war in Ukraine, and their most pressing needs. It’s an eye-opening and enlightening look behind the curtain.
- Articles
- Columns
- Links
- Media kit
||| MENU - pcb007 Magazine
Forming Standards for Ultra HDI
October 25, 2022 | Andy Shaughnessy, Design007 MagazineEstimated reading time: 3 minutes
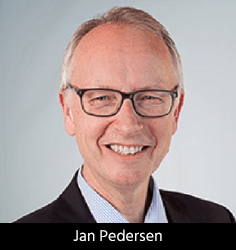
To get the latest news about ultra high-density interconnections (UHDI), we checked in with Jan Pedersen, NCAB Group’s director of technology. Jan is co-chair of IPC D-33AP, and a great source of overall DFM expertise as well. We asked him to give us a snapshot of UHDI in the industry, where we’re headed, and what this means to PCB designers.
Q: How do you define ultra HDI? What is the cutoff in mils or microns?
A: UHDI is defined in the IPC UHDI task group as a PCB design with lines and spaces below 50 microns, dielectric thickness below 50 microns, and microvias below 75 microns. These are attributes beyond the existing IPC-2226 Producibility level C.
Q: Tell us about your work on IPC’s UHDI committee. What are you working on right now? Are the standards keeping up with UHDI technology?
A: The UHDI task group has now developed a basic description and parameters. We are ready to hand over our work to the next group at IPC to start building the standards structure, starting with design, followed by performance and acceptance standards.
The standards will keep up with UHDI technology, but this will need our full attention for the standard to reflect current production capabilities globally.
Q: Much of the ultra HDI we see involves semi-additive technology. Can you clear up the differences between mSAP and A-SAP, and what it means to designers and design engineers?
A: SAP stands for semi-additive processes, and there are a few versions out there such as mSAP and A-SAP. We call them semi-additive because they all start with a thin layer of copper before creating the circuitry. This can be either from a copper-clad material, similar to what we use in traditional PCB manufacturing but with thinner copper, or a non-clad material where the PCB factory plates the seed layer. The difference between mSAP and A-SAP is the thickness of the seed layer where mSAP starts with a copper layer, typically 3–4 microns, while A-SAP starts from an unclad material activating the surface, adding a very thin chemical copper layer of less than 1 micron. Then both processes use photolithographic methods to plate up copper traces to around 20-micron thickness before flash etching the seed layer. Basically, the thickness of the seed layer, as we see with A-SAP, is the main factor for the process to create thinner traces.
Q: How is designing in the ultra HDI arena different from designing a typical PCB? What are some of the hurdles?
A: Designing ultra HDI is a challenge today because of a lack of standards, both for PCB production and material availability. The big hurdle today is fabrication availability. There are processes and some materials available, but very few PCB factories can offer anything below 40-micron trace and space. Some factories claim to offer UHDI, but that is very often only down to 35- to 40-micron traces, while the components you want to use requires traces and spaces below 30 microns.
Q: Are there any resources—books, websites, instructors, etc.—for UHDI design techniques?
A: For designers who want to learn more about UHDI, there are a limited number of resources. I would start with Tara Dunn’s Altium blogs and her I-Connect007 columns, which often cover semi-additive and UHDI. Anyone considering moving into ultra HDI should follow the NCAB blogs, available on our website and on LinkedIn. Read everything that you can.
Q: What advice would you give designers who are considering moving into UHDI?
A: The best advice I can offer is to find a supplier and be sure that you design within their capabilities. NCAB has a plan to be providing high-mix, low-volume UHDI starting as early as 2023. Today all factories that offer less than 35-micron traces have extremely long lead times. Not to sound commercial, but NCAB Group has a clear plan to change that. We are not there yet but will be very soon.
I am leading the NCAB Technical Council, and one of the focus teams is working actively with ultra HDI. As soon as we have a factory that can offer shorter lead times on UHDI, we will develop design guidelines and webinars, and provide workable parameters for designers. We need safe parameters to secure manufacturing yields and product quality from the start. It is paramount for NCAB Group to be transparent about what we can offer and how ready we are with new technologies.
This interview originally appeared in the October 2022 issue of Design007 Magazine.
Suggested Items
The Evolution of Picosecond Laser Drilling
06/19/2025 | Marcy LaRont, PCB007 MagazineIs it hard to imagine a single laser pulse reduced not only from nanoseconds to picoseconds in its pulse duration, but even to femtoseconds? Well, buckle up because it seems we are there. In this interview, Dr. Stefan Rung, technical director of laser machines at Schmoll Maschinen GmbH, traces the technology trajectory of the laser drill from the CO2 laser to cutting-edge picosecond and hybrid laser drilling systems, highlighting the benefits and limitations of each method, and demonstrating how laser innovations are shaping the future of PCB fabrication.
Day 2: More Cutting-edge Insights at the EIPC Summer Conference
06/18/2025 | Pete Starkey, I-Connect007The European Institute for the PCB Community (EIPC) summer conference took place this year in Edinburgh, Scotland, June 3-4. This is the third of three articles on the conference. The other two cover Day 1’s sessions and the opening keynote speech. Below is a recap of the second day’s sessions.
Day 1: Cutting Edge Insights at the EIPC Summer Conference
06/17/2025 | Pete Starkey, I-Connect007The European Institute for the PCB Community (EIPC) Summer Conference took place this year in Edinburgh, Scotland, June 3-4. This is the second of three articles on the conference. The other two cover the keynote speeches and Day 2 of the technical conference. Below is a recap of the first day’s sessions.
Preventing Surface Prep Defects and Ensuring Reliability
06/10/2025 | Marcy LaRont, PCB007 MagazineIn printed circuit board (PCB) fabrication, surface preparation is a critical process that ensures strong adhesion, reliable plating, and long-term product performance. Without proper surface treatment, manufacturers may encounter defects such as delamination, poor solder mask adhesion, and plating failures. This article examines key surface preparation techniques, common defects resulting from improper processes, and real-world case studies that illustrate best practices.
RF PCB Design Tips and Tricks
05/08/2025 | Cherie Litson, EPTAC MIT CID/CID+There are many great books, videos, and information online about designing PCBs for RF circuits. A few of my favorite RF sources are Hans Rosenberg, Stephen Chavez, and Rick Hartley, but there are many more. These PCB design engineers have a very good perspective on what it takes to take an RF design from schematic concept to PCB layout.