-
-
News
News Highlights
- Books
Featured Books
- pcb007 Magazine
Latest Issues
Current IssueThe Hole Truth: Via Integrity in an HDI World
From the drilled hole to registration across multiple sequential lamination cycles, to the quality of your copper plating, via reliability in an HDI world is becoming an ever-greater challenge. This month we look at “The Hole Truth,” from creating the “perfect” via to how you can assure via quality and reliability, the first time, every time.
In Pursuit of Perfection: Defect Reduction
For bare PCB board fabrication, defect reduction is a critical aspect of a company's bottom line profitability. In this issue, we examine how imaging, etching, and plating processes can provide information and insight into reducing defects and increasing yields.
Voices of the Industry
We take the pulse of the PCB industry by sharing insights from leading fabricators and suppliers in this month's issue. We've gathered their thoughts on the new U.S. administration, spending, the war in Ukraine, and their most pressing needs. It’s an eye-opening and enlightening look behind the curtain.
- Articles
- Columns
- Links
- Media kit
||| MENU - pcb007 Magazine
PCB Technologies Sees Substrates as a Foundation
October 27, 2022 | Nolan Johnson, I-Connect007Estimated reading time: 5 minutes
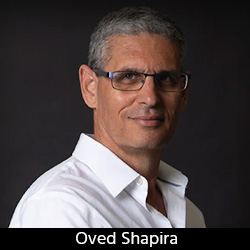
In this interview, PCB Technologies CEO Oved Shapira discusses the company's move into advanced packaging and heterogenous integration. Shapira explains how substrates and advanced packaging fit into the PCB fab and assembly ecosystem, and makes the argument that an all-inclusive fabrication and assembly supplier can be of great value to customers in product development and small scale production.
AUDIO TRANSCRIPT
Nolan Johnson: Hi, Nolan Johnson here for I-Connect007, and I have the pleasure right now of speaking with Oved Shapira. He is the Chief Operating Executive for PCB Technologies. Oved, welcome!
Oved Shapira: Thank you, Nolan.
Johnson: Give an update with what's going on with PCB Technologies.
Shapira: It's a very interesting time for us because we have created for our customers in the last year and a half a very unique solution of all in one. We can provide today with the recent launching of our new fab for assembly of advanced packaging, basically a solution from PCB level all the way to box building with a unique solution of advanced packaging and system in package. We can start from low- to mid-volume from NPI and prototype all the way to high volume, and we are also producing for our customer or doing the design of the substrate, which has come to be a very limited resource for different reasons, some of them political. As you know, there is some restriction about sourcing from the Far East, and the Western manufacturers are looking for local manufacturing or Western manufacturers with ITAR approval for substrates and for advanced packaging. This is something that you hardly can find in the Western manufacturer.
PCB today is an enabler basically for 1 mil line and space with a unique solution on package-on-package and 3D solution. Again, together with our heterogeneous engineering from PCB boards all the way to assembly of electronic components, it gives a unique solution to our customers. Just to give you an idea today, if you want to develop a model of advanced packaging with a multichip system, it will take an average of about two years from scratch all the way to production that can be commercial. We believe that because we have everything under the same umbrella, in the same place, with such advanced engineering capabilities, you can do it in half, and on top of that, it gives you maximum flexibility.
Today, if you need to go to different vendors, one of them will be the substrate, another one will be the packaging, another one will do the PCB, and the last one will do the assembly. You will always be forced to compromise on the very low common ground, and what we offer to our customers is no compromise to reach the potential of the technology. May I say the highest level of common craft you need to compromise today because say you need to take into consideration the design for manufacturing guidelines of each vendor, and of course, each vendor is not synchronized with the other vendors. Here at PCB Technologies, we are fully synchronized, and we give the solution, like I said, from A to Z, a full heterogeneous engineering view.
Johnson: From two years to six months is a significant acceleration of the development schedule, for sure.
Shapira: Yeah, and this is not just the time to mount and the cost involved, it's also the ease of designing and innovation process. PCB DNA is akin to attitude. Instead of getting very inflexible guidelines for design, you can get almost endless possibilities for a solution. Obviously, we prefer to meet our customer near to the design board on the drawing board earlier if possible and make sure that we understand the pain and the unmet need of the customer from an engineering standpoint, and then what is the design-to-cost guidelines we put together and I think that the outcome is very impressive.
Johnson: Oved, what sorts of quantities can a customer start with if they're looking at substrates and heterogeneous integration? I know that in the research I've done recently, some of the more common Asia-based manufacturers are looking for very large quantities in the large tens of thousands at a minimum.
Shapira: It's a very good question and let me give you the figures. First, let's talk about Asia. As you said, most of the time you have two factors when you want to develop a new model. First, the NRE probably will be in the vicinity of a million dollars for a multichip system, 20 x 20 with four or five elements will be no less than a million dollars. Definitely, if you need to go for a very high-density line and space. The MOU most of the time will be at the vicinity of the high level of hundreds of thousands or millions per month or even sometimes per week; it depends on the design.
In PCB, definitely we don't talk about $1 million for NRE, we are talking about the low hundred or thousands of dollars to develop a new model, and the starting point will be sometimes thousands, hundred thousands, 10,000, all the way to the possibility to produce millions if you need at the end of the road. If you need to have a dedicated assembly line for a few million models, we don't have a problem establishing this line for you, but the starting point will not be millions or a high level number of hundreds of thousands per month. It will be a few dozen that you can consume over a year without a problem.
Johnson: PCB Technologies is currently in production for substrates?
Shapira: We are in full production of substrates, and we are now in full production of advanced packaging. Of course, we’re going to share all this information with our customers, but we invite customers to come and visit and see what level of facility we build here. There is another big advantage that we can discuss here. It's panel level packaging, meaning that you don't do the packaging on the module level, but on the panel level, and the level of efficiency is much higher. Because we produce the panel in the fab of the PCB, we have the ability to do the panel level packaging, which is very unique as well, and we build the line for the panel level packaging.
Johnson: This is great news to know that there are additional resources coming on board for the industry in advanced packaging heterogeneous integration, especially with you at PCB Technologies. Thanks for taking the time to talk with us about this.
Shapira: Thank you for the opportunity to talk with you, and we welcome all customers in the U.S. market and Europe to visit our website and in any digital platform or contact person in the region and get more information, and I'm sure that it'll be an opportunity for them.
Johnson: I've been speaking with the chief operating executive for PCB Technologies, Oved Shapira. Thanks for listening.
Suggested Items
DownStream Acquisition Fits Siemens’ ‘Left-Shift’ Model
06/26/2025 | Andy Shaughnessy, I-Connect007I recently spoke to DownStream Technologies founder Joe Clark about the company’s acquisition by Siemens. We were later joined by A.J. Incorvaia, Siemens’ senior VP of electronic board systems. Joe discussed how he, Rick Almeida, and Ken Tepper launched the company in the months after 9/11 and how the acquisition came about. A.J. provides some background on the acquisition and explains why the companies’ tools are complementary.
Elementary Mr. Watson: Retro Routers vs. Modern Boards—The Silent Struggle on Your Screen
06/26/2025 | John Watson -- Column: Elementary, Mr. WatsonThere's a story about a young woman preparing a holiday ham. Before putting it in the pan, she cuts off the ends. When asked why, she shrugs and says, "That's how my mom always did it." She asks her mother, who gives the same answer. Eventually, the question reaches Grandma, who laughs and says, "Oh, I only cut the ends off because my pan was too small." This story is a powerful analogy for how many PCB designers approach routing today.
Connect the Dots: The Future of PCB Design and Manufacturing
07/02/2025 | Matt Stevenson -- Column: Connect the DotsFor some time, I have been discussing the increasing complexity of PCBs and how designers can address the constantly evolving design requirements associated with them. My book, "The Printed Circuit Designer’s Guide to… Designing for Reality," details best practices for creating manufacturable boards in a modern production environment.
Siemens Turbocharges Semiconductor and PCB Design Portfolio with Generative and Agentic AI
06/24/2025 | SiemensAt the 2025 Design Automation Conference, Siemens Digital Industries Software today unveiled its AI-enhanced toolset for the EDA design flow.
Cadence AI Autorouter May Transform the Landscape
06/19/2025 | Andy Shaughnessy, Design007 MagazinePatrick Davis, product management director with Cadence Design Systems, discusses advancements in autorouting technology, including AI. He emphasizes a holistic approach that enhances placement and power distribution before routing. He points out that younger engineers seem more likely to embrace autorouting, while the veteran designers are still wary of giving up too much control. Will AI help autorouters finally gain industry-wide acceptance?