Isola Brings Broad Range of Circuit Material Solutions to Electronica 2022
November 2, 2022 | Isola GroupEstimated reading time: 2 minutes
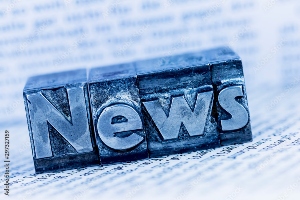
Isola Group is coming to Munich, Germany and Electronica 2022 with an assortment of circuit materials expected to meet or exceed the needs of the broad range of markets the international event serves. Set for November 15-18, 2022 in the Trade Fair Center, Messe Munchen, Electronica 2022 is the world’s leading conference and exhibition for the design and production of all things electronic, from consumer products to long-lasting assemblies built for space. Isola Group will be in Hall B1, Booth #422 at the show. Isola’s material experts will welcome visitors with advice and guidance on optimum use of the company’s most popular laminates and prepregs.
Like Electronica 2022, Isola’s circuit materials cover a broad spectrum of markets, for printed circuit boards (PCBs) in everything from portable electronic devices and automotive safety systems to Fifth Generation (5G) base stations and small cells and satellite communications (satcom) systems. The materials are “made for manufacturing,” formulated with characteristics that enable different circuit materials to be fabricated with compatible processes, even when they are used to form multilayer, multiple-signal PCBs with a blend of analog, digital, and power circuitry. Isola’s materials on display will include I-Tera® MT40, I-Tera® MT40 (RF/MW), Astra® MT77, Tachyon® 100G, TerraGreen®, TerraGreen® (RF/MW), and TerraGreen® 400G.
These high-performance circuit materials feature key parameters, such as high glass transition temperature (Tg) and decomposition temperature (Td) to encourage compatibility of processing. The materials offer circuit designers and PCB fabricators a wide choice of circuit performance parameters, including permittivity (Dk) and dissipation factor or loss (Df), with behavior that remains stable over wide operating temperature ranges, making them suitable choices for many growing electronic applications including Advanced Driver Assistance Systems (ADAS) and their 77 GHz mmWave radar circuits, 5G wireless communications networks, and smart energy systems.
I-Tera MT40, which is a good starting point for many high-speed digital (HSD) circuits and RF/microwave PCBs, is RoHS, lead-free process compatible and FR-4 process compatible. With a Dk that is stable with frequency (3.45 through 10 GHz) and over wide temperature ranges, it forms reliable PCBs for HSD and also microwave applications. For higher microwave frequencies, I-Tera MT-40 (RF/MW) offers Dk tailored to a user’s requirements but boasts performance consistent with time, temperature, and frequency, which is true for the general-purpose/HSD versions of the material as well.
When circuit loss is a concern, few circuit materials can match the performance of Isola’s Astra MT77 laminates (also available as prepregs without copper cladding) and their low Df of 0.0017. Also, FR-4 process compatible, these materials are ideal candidates for the mmWave portions of 5G networks and the 77 GHz radar circuits in ADAS systems. For mmWave frequency coverage where low z-axis (thickness) coefficient of thermal expansion (CTE) is required, Isola’s Tachyon 100G provide extremely high stability over frequency and temperature through 100 GHz analog frequencies and 100 Gb/s digital rates. And for designers and PCB producers in need of high-performance, halogen-free circuit materials, Isola’s TerraGreen, TerraGreen (RF/MW), and TerraGreen 400G provide lead-free RoHS-compliant solutions usable for PCBs operating through high microwave frequencies and high-speed digital rates. Visitors to Electronica 2022 are welcome to visit Booth #422 to learn more.
Testimonial
"Advertising in PCB007 Magazine has been a great way to showcase our bare board testers to the right audience. The I-Connect007 team makes the process smooth and professional. We’re proud to be featured in such a trusted publication."
Klaus Koziol - atgSuggested Items
Trouble in Your Tank: Minimizing Small-via Defects for High-reliability PCBs
08/27/2025 | Michael Carano -- Column: Trouble in Your TankTo quote the comedian Stephen Wright, “If at first you don’t succeed, then skydiving is not for you.” That can be the battle cry when you find that only small-diameter vias are exhibiting voids. Why are small holes more prone to voids than larger vias when processed through electroless copper? There are several reasons.
The Government Circuit: Navigating New Trade Headwinds and New Partnerships
08/25/2025 | Chris Mitchell -- Column: The Government CircuitAs global trade winds continue to howl, the electronics manufacturing industry finds itself at a critical juncture. After months of warnings, the U.S. Government has implemented a broad array of tariff increases, with fresh duties hitting copper-based products, semiconductors, and imports from many nations. On the positive side, tentative trade agreements with Europe, China, Japan, and other nations are providing at least some clarity and counterbalance.
How Good Design Enables Sustainable PCBs
08/21/2025 | Gerry Partida, Summit InterconnectSustainability has become a key focus for PCB companies seeking to reduce waste, conserve energy, and optimize resources. While many discussions on sustainability center around materials or energy-efficient processes, PCB design is an often overlooked factor that lies at the heart of manufacturing. Good design practices, especially those based on established IPC standards, play a central role in enabling sustainable PCB production. By ensuring designs are manufacturable and reliable, engineers can significantly reduce the environmental impact of their products.
50% Copper Tariffs, 100% Chip Uncertainty, and a Truce
08/19/2025 | Andy Shaughnessy, I-Connect007If you’re like me, tariffs were not on your radar screen until a few months ago, but now political rhetoric has turned to presidential action. Tariffs are front-page news with major developments coming directly from the Oval Office. These are not typical times. President Donald Trump campaigned on tariff reform, and he’s now busy revamping America’s tariff policy.
Global PCB Connections: Understanding the General Fabrication Process—A Designer’s Hidden Advantage
08/14/2025 | Markus Voeltz -- Column: Global PCB ConnectionsDesigners don’t need to become fabricators, but understanding the basics of PCB fabrication can save you time, money, and frustration. The more you understand what’s happening on the shop floor, the better you’ll be able to prevent downstream issues. As you move into more advanced designs like HDI, flex circuits, stacked vias, and embedded components, this foundational knowledge becomes even more critical. Remember: the fabricator is your partner.