-
- News
- Books
Featured Books
- pcb007 Magazine
Latest Issues
Current IssueInventing the Future with SEL
Two years after launching its state-of-the-art PCB facility, SEL shares lessons in vision, execution, and innovation, plus insights from industry icons and technology leaders shaping the future of PCB fabrication.
Sales: From Pitch to PO
From the first cold call to finally receiving that first purchase order, the July PCB007 Magazine breaks down some critical parts of the sales stack. To up your sales game, read on!
The Hole Truth: Via Integrity in an HDI World
From the drilled hole to registration across multiple sequential lamination cycles, to the quality of your copper plating, via reliability in an HDI world is becoming an ever-greater challenge. This month we look at “The Hole Truth,” from creating the “perfect” via to how you can assure via quality and reliability, the first time, every time.
- Articles
- Columns
- Links
- Media kit
||| MENU - pcb007 Magazine
Purdue Defense Research Focuses on Expanding Knowledge of Nontoxic Alternatives for Circuit Boards
November 10, 2022 | Purdue UniversityEstimated reading time: 3 minutes
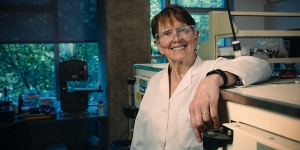
Carol Handwerker’s life’s work is aimed at increasing reliability in everything from the largest Navy carrier to the family car. She does it by researching probably the most inconspicuous material: solder.
Handwerker, the Reinhardt Schuhmann Jr. Professor of Materials Engineering at Purdue University, has tested and researched materials for almost 30 years to determine the best options for solder that connects electronic components to circuit boards, focusing on almost any physical condition that a circuit board could encounter.
In today’s evolving era of microelectronics, green polymer circuit boards are among the most important factors. Without these functioning circuit boards – that can range from the size of a fist to a large photo frame – even a lot of the cars on the road today would stay parked.
“In today’s boards, there are so many interconnects,” Handwerker said. “There are thousands, if not millions, of solder joints in a single circuit board. If a solder joint fails, the system is compromised. So, it’s important that solder is reliable.”
Tin-lead solder was the mainstay for more than 50 years. But environmental and health concerns brought about the evolution of a new generation of solders that are lead-free and use alloys that are a better, nontoxic alternative to tin-lead.
One of more than 60 kinds of solder on the market today, tin-lead solder was banned by the European Union in 1999 for use in consumer electronics because of toxicity concerns. Handwerker, also a professor of environmental and ecological engineering at Purdue, was part of four years of research in the 1990s that preceded that ban, setting a baseline for possible replacement alloys. She worked closely with industry in the 2000s to transition to the new standard lead-free alloy for consumer electronics worldwide.
The only industries still exempted by the EU are defense, aerospace and implantable medical devices.
Handwerker’s current research is part of the U.S. Partnership for Assured Electronics (USPAE) and is backed by a $40 million U.S. Department of Defense contract. The work is in concert with defense companies and experts from the University of Maryland, Auburn University and Binghamton University and focuses on determining when lead-free solders might be as reliable or more so than tin-lead when used in defense systems.
“We’re providing options in a way that gives all of us confidence in our solder choices,” Handwerker said. “Solder is used in Department of Defense systems everywhere there are circuit boards, from handheld communication devices and battleships to helicopters and missiles. We are working to quantify how different lead-free solders behave in various highly demanding environments compared with tin-lead.”
Now in its second year, the five-year project has developed the first edition of the Solder User’s Handbook, which was recently approved by the Department of Defense. Handwerker said the project also is developing specifications and underlying scientific analysis allowing researchers to extrapolate to more extreme defense environments.
Handwerker is joined in her solder project by three other Purdue professors – Ganesh Subbarayan, professor of mechanical engineering; John Blendell, professor of materials engineering; and Nikhilesh Chawla, the Ransburg Professor of Materials Engineering – and Harvey Abramowitz, a professor of mechanical engineering at Purdue University Northwest.
As the inconspicuous glue that holds the components of circuit boards together, solder has a litany of microelectronics uses in Department of Defense vehicles and equipment. Jets face thermal cycling issues in which systems must function through high heat, then cold temperatures and back to high heat. Vibration and shock impact scenarios are shared by the solder used in circuit boards for planes, naval vessels and missiles.
Current experimentation at Purdue is focused on data analysis, solder reliability testing and process testing that confirms what the melting temperatures are for the solders. An in-depth testing plan is being developed.
Purdue is a national leader in microelectronics devices and packaging research, spanning the semiconductor ecosystem in software and hardware.
Purdue already has established excellence in key research areas considered critical to national security, including microelectronics. The area is among the critical topics under Purdue’s Next Moves, strategic initiatives that will advance the university’s competitive advantage.
A recent agreement with MediaTek, a leading global chipmaker, partnerships for future workforce development and the establishment of a semiconductor degrees program are the latest pieces of Purdue’s continually expanding research and development efforts in the field of microelectronics and semiconductors.
Here is more on Purdue’s leadership in the area of microelectronics.
Testimonial
"Our marketing partnership with I-Connect007 is already delivering. Just a day after our press release went live, we received a direct inquiry about our updated products!"
Rachael Temple - AlltematedSuggested Items
Indium Corporation Promotes Two Leaders in EMEA (Europe, Middle East, and Africa) Markets
08/05/2025 | Indium CorporationWith its commitment to innovation and growth through employee development, Indium Corporation today announced the promotions of Andy Seager to Associate Director, Continental Sales (EMEA), and Karthik Vijay to Senior Technical Manager (EMEA). These advancements reflect their contributions to the company’s continued innovative efforts with customers across Europe, the Middle East, and Africa (EMEA).
MacDermid Alpha Electronics Solutions Unveils Unified Global Website to Deepen Customer, Talent, and Stakeholder Engagement
07/31/2025 | MacDermid Alpha Electronics SolutionsMacDermid Alpha Electronics Solutions, the electronics business of Elements Solutions Inc, today launched macdermidalpha.com - a unified global website built to deepen digital engagement. The launch marks a significant milestone in the business’ ongoing commitment to delivering more meaningful, interactive, and impactful experiences for its customers, talent, and stakeholders worldwide.
KOKI to Showcase Analytical Services and New HF1200 Solder Paste at SMTA Guadalajara 2025
07/31/2025 | KOKIKOKI, a global leader in advanced soldering materials and process optimization services, will exhibit at the SMTA Guadalajara Expo & Tech Forum, taking place September 17 & 18, 2025 at Expo Guadalajara, Salón Jalisco Halls D & E in Guadalajara, Mexico.
Weller Tools Supports Future Talent with Exclusive Donation to SMTA Michigan Student Soldering Competition
07/23/2025 | Weller ToolsWeller Tools, the industry leader in hand soldering solutions, is proud to announce its support of the upcoming SMTA Michigan Expo & Tech Forum by donating a limited-edition 80th Anniversary Black Soldering Set to the event’s student soldering competition.
Koh Young Appoints Tom Hattori as President of Koh Young Japan
07/21/2025 | Koh YoungKoh Young Technology, the global leader in True 3D measurement-based inspection solutions, announced the appointment of Tom Hattori as President of Koh Young Japan (JKY).