Web vs. Direct Imaging
November 22, 2022 | I-Connect007 Editorial TeamEstimated reading time: 3 minutes
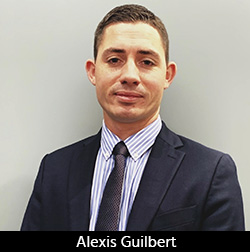
As flexible printed circuits (FPC) continue making waves in PCB manufacturing, the Altix team of Alexis Guilbert, Damien Boureau, and Alexandre Camus look at today’s use cases for FPCs, and detail the finer points of roll-to-roll technology vs. direct imaging. For example, how long can a flexible circuit be? Which technology works best with extremely long circuits, and how does a customer know which one to use? The I-Connect007 Editorial Team explores these trending topics and what it means for PCB manufacturers.
Nolan Johnson: We’re here to learn more about Altix’s continued work on roll-to-roll technologies. What do you see as the market drivers for roll-to-roll?
Alexis Guilbert: One booming market is automotive. More specifically, it’s the electric vehicle battery manufacturing market, which is enjoying tremendous growth. One report I read mentioned a $7 billion growth in market size by this year. I believe the flexible printed circuit segment is growing in the industry because it replaces wires, for example, which used to always be wire harnesses. Now it’s FPC, which saves assembly time and space as well as space and weight in the vehicle. You divide those by approximately two compared to normal wires. Of course, it’s an FPC, so you will have data like temperature, voltage, and everything else.
Alexandre Camus: The main drivers will be, for example, battery packs, interconnects, some sensors, and wire harness replacements. I want to stress that for battery pack interconnects, it will mostly be for electric vehicles but there will always be more FPC in traditional ICE vehicles. The EV and autonomous vehicles are growing domains. It’s a really dynamic market.
Johnson: For the automotive sector specifically, it sounds like this is replacing some wire harnesses.
Guilbert: Yes, it’s basically a wire harness replacement. That’s one of the main drivers for both our roll-to-roll contact printers and direct imager (DI).
Johnson: What’s the value-add for moving to flex over the wire harness? Why is flex better than a traditional wire harness?
Guilbert: It saves space and reduces weight. For a vehicle, that’s tremendously important as those are critical features. It saves part count and assembly time. In electric vehicles, it gives data to the battery management system (BMS), such as the temperatures or voltage. If I go a bit deeper, you have a thermal management system for the batteries, and you need to send this data as well to the BMS. A lot of data needs to be transmitted—and not only to the BMS as you have the communication between the BMS and the dashboard. This is incorporated for the driver to look at.
Johnson: By using flex circuits, in this case, you can get more data channels into a smaller space?
Camus: It’s a win-win because you save space, and you get more out of the product. It’s a clear upgrade. No downsides.
Barry Matties: Is there an advantage for eliminating crosstalk or noise compared to the wire harness?
Guilbert: Yes. There is less noise concern when you have an FPC compared to a wire harness. That is also true.
Matties: That’s probably one of the big advantages in design as well. We’re talking automotive, but are you seeing any trends into perhaps the commercial or military aircraft spaces as well?
Camus: Yes. I’ve definitely seen cases for unmanned aerial vehicles (UAVs) in both military and civilian applications. We haven’t seen the end of the market yet. It’s still growing.
Matties: With the roll-to-roll technology, there’s no limit to the length, correct?
Guilbert: That’s correct.
Damien Boureau: In fact, this is part of what we are bringing together with our contact printer or direct machine units in roll-to-roll. We can bring options to help our customer produce something like an unlimited flexible circuit. We added some functions, like stitching images all together over the web, or clipping a very long image so that we can recompose it at the end.
To read this entire conversation, which appeared in the October 2022 issue of PCB007 Magazine, click here.
Testimonial
"Advertising in PCB007 Magazine has been a great way to showcase our bare board testers to the right audience. The I-Connect007 team makes the process smooth and professional. We’re proud to be featured in such a trusted publication."
Klaus Koziol - atgSuggested Items
Meet the Author Podcast: Martyn Gaudion Unpacks the Secrets of High-Speed PCB Design
07/16/2025 | I-Connect007In this special Meet the Author episode of the On the Line with… podcast, Nolan Johnson sits down with Martyn Gaudion, signal integrity expert, managing director of Polar Instruments, and three-time author in I-Connect007’s popular The Printed Circuit Designer’s Guide to... series.
Intervala Hosts Employee Car and Motorcycle Show, Benefit Nonprofits
08/27/2024 | IntervalaIntervala hosted an employee car and motorcycle show, aptly named the Vala-Cruise and it was a roaring success! Employees had the chance to show off their prized wheels, and it was incredible to see the variety and passion on display.
KIC Honored with IPC Recognition for 25 Years of Membership and Contributions to Electronics Manufacturing Industry
06/24/2024 | KICKIC, a renowned pioneer in thermal process and temperature measurement solutions for electronics manufacturing, is proud to announce that it has been recognized by IPC for 25 years of membership and significant contributions to electronics manufacturing.
Boeing Starliner Spacecraft Completes Successful Crewed Docking with International Space Station
06/07/2024 | BoeingNASA astronauts Barry "Butch" Wilmore and Sunita "Suni" Williams successfully docked Boeing's Starliner spacecraft to the International Space Station (ISS), about 26 hours after launching from Cape Canaveral Space Force Station.
KIC’s Miles Moreau to Present Profiling Basics and Best Practices at SMTA Wisconsin Chapter PCBA Profile Workshop
01/25/2024 | KICKIC, a renowned pioneer in thermal process and temperature measurement solutions for electronics manufacturing, announces that Miles Moreau, General Manager, will be a featured speaker at the SMTA Wisconsin Chapter In-Person PCBA Profile Workshop.