-
-
News
News Highlights
- Books
Featured Books
- pcb007 Magazine
Latest Issues
Current IssueThe Hole Truth: Via Integrity in an HDI World
From the drilled hole to registration across multiple sequential lamination cycles, to the quality of your copper plating, via reliability in an HDI world is becoming an ever-greater challenge. This month we look at “The Hole Truth,” from creating the “perfect” via to how you can assure via quality and reliability, the first time, every time.
In Pursuit of Perfection: Defect Reduction
For bare PCB board fabrication, defect reduction is a critical aspect of a company's bottom line profitability. In this issue, we examine how imaging, etching, and plating processes can provide information and insight into reducing defects and increasing yields.
Voices of the Industry
We take the pulse of the PCB industry by sharing insights from leading fabricators and suppliers in this month's issue. We've gathered their thoughts on the new U.S. administration, spending, the war in Ukraine, and their most pressing needs. It’s an eye-opening and enlightening look behind the curtain.
- Articles
- Columns
- Links
- Media kit
||| MENU - pcb007 Magazine
EIPC: Europe’s Energy Disadvantage
December 15, 2022 | Nolan Johnson, I-Connect007Estimated reading time: 10 minutes
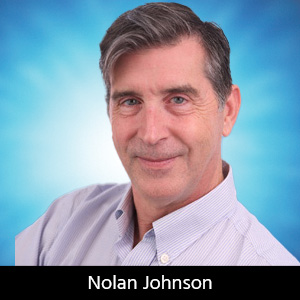
EIPC’s Alun Morgan details the unsettling realities facing the European PCB industry due to the current war in Ukraine, and outlines steps that the EIPC plans to take to help raise awareness of the possible perils the industry might face as a result.
Nolan Johnson: Alun, you just did a presentation for EIPC on the impact of energy costs, etc., in Europe. Tell us about that.
Alun Morgan: In Europe, we are in a rather special situation right now. We entered 2022 with great expectations and hopes. Then, of course, we had the invasion of Ukraine. This had a huge impact on energy security and supply. I looked at data for last year, as much as I could get, and I established that if you put energy costs in kWh and compared those figures across European countries, there’s a range of different costs. Compare the average, though, with that of the USA or China in 2021, and Europe was significantly higher in energy costs than those regions. So that was our baseline. Since then, of course, the world has undergone some drastic changes, and people now tell me energy costs have risen by a factor of three from where they were. This is a uniquely European burden, and it is actually a very difficult burden to carry.
Europe has around €1.8 billion to €1.9 billion worth of PCB production left. This number has been pretty stable the last few years. Of course, there was a drop down to about €1.5 billion during the pandemic; we came back down to the equivalent of the last 10-year average, more or less. The problem we face now is that, if energy costs continue to rise, the industrial electronics sector will be adversely affected. Not the high-tech end, but the tier 1 sector of industrial electronics—what accounts for the majority of our business in Europe—will be the most impacted. If things carry on this way, we could lose some more players—we will lose a few more shops. Even though the turnovers been consistent for Europe, the number of board shops has declined over time, and I feel there could be another step down in the total supply in Europe.
The problem there is that the supply chain has fewer customers to serve, so we’ve lost more of the supply chain as well. We already lost a lot in the year 2000; now, the supply chain for our business is primarily in Asia. So far, the PCB side is still here.
Not only that, but consider what’s going on with government. People are asking whether we should bring home some production. This is a current trend running across North America and Europe. It’s understandable why this would be the case: we have the American CHIPS Act; we have initiatives now in Europe in the EU to bring some chip manufacturing back into Europe for many reasons. The problem is, if we bring the silicon back, where are the boards? Where are the PCBs? If you have no PCBs, what’s the point? You still have to send the silicon to Asia to be packaged and assembled and brought back again.
My point is this: If we’re going to be serious about this and truly want to protect what we have—never mind growing it—we’ve got to have to consider the PCB side as well. Without PCBs, there’s no reason to make silicon in Europe. You can imagine different sectors that need supply, but the one that first comes to mind is the defense sector. Out of all the things that are going in our world, defense is something that we have to take very seriously.
I heard from one of the major users of defense equipment just a couple of days ago, and he said that even today, there are not enough qualified suppliers for defense electronics, particularly for flex material. Flex material is quite high tech, but it’s also high reliability, so they need reliability data to know the boards are going to work. Even today, he said, there aren’t enough suppliers for him. He’s one of the major consumers; can you imagine if we were to lose a few more suppliers?
We need to be careful. There’s a level below which we should not go. There’s a line we should not cross, and that line is probably the defense requirements that we have. It will make no sense at all to allow the supply level to below the level we need for our own defense.
Considering all this, we’ve decided to put some information together. I already have some data from last year, and we are working on gathering this year’s data to see how our industries in Europe are being impacted. And by Europe, I am mainly referring to the EU, as well as the UK and Switzerland—Europe as a region. Once we have this data, we’ll go to whoever will listen to us and tell our story. We’ll send the message that, “If you let things continue in this way, there’s a very good chance that we will take another step downwards by losing even more business.”
We can also discuss tariffs on imported materials, circuit boards, and raw materials. Our tariff structure is set up completely wrong. We are encouraging the importation of final PCBs, but we are penalizing the importation of materials to make those PCBs. How is that right? Especially in our current climate, where we are trying to reshore again?
Johnson: Did I hear you mention earlier that there’s a 5% tariff on materials?
Morgan: I think it depends on the product you’re bringing in, but yes, around 5%. If you’re going to build PCBs here, you’ll take a 5% hit against those who want to make the PCBs elsewhere. Well, that is something; 5% doesn’t solve all our problems, but it’s something. Twenty-three years ago, doing this made more sense; we've discussed it since then, but we couldn’t get any real movement on it. I think this setup really goes against our current climate. The sentiment now is that we should make it easier to make locally produced materials, and I the think tariff system is going against that entirely. I think the argument against that system is a good one, so we’ll start with that and see how we how we manage.
Johnson: You have quite a few dynamics to manage if you want to encourage industry growth to avoid sliding below critical mass. But you have some strong headwinds: energy costs are a problem, tariffs are an issue, expertise is an issue. Making sure you’ve got customers in the ecosystem—that’s another issue.
Morgan: There are customers here. Europe is still a huge consumer of electronics, second only to North America, and we are one of the two biggest consumer markets in the world by far. The big problem we have here is access to capital. In Asia, accessing capital is far easier. We don’t have capital structures in Europe to support business in the same way Asia does. I think that’s a shame. Companies, typically in the West, are taking a fairly short-term view of their return on investments. And when I say “short term,” I mean single-digit yearly numbers. From my experiences with Asian companies, they’re thinking in double digits—very long periods. I think that’s an important distinction.
A big problem now is, if you can get access to capital, what interest rate do you pay? Inflation is rising; you can’t get 1% rates any longer. In the UK, inflation has now hit 11% in the latest figures. It’s running in the high single digits in the rest of Europe, so 9% to 10% is quite normal now. Now, we all know that government actions will bring this inflation rate down, because they’re targeting exactly that, and U.S. policy is doing precisely that, and all those policies will have an effect. In the meantime, though, if you want to borrow money today, you borrow at today’s rates. A few weeks ago, I was at a big plant in Germany that chose to make a very a big investment; people are still doing it, but the access to that capital is not so easy anymore.
Of course, we want to grow. But I’ll be happy when we really shore up what we have. That should be our priority. Europe has some special sectors—I mentioned defense already—but medical is also very well established and of interest to the industry, as are antenna technology and high frequency. We have some very specialized companies in Europe that are very competent in doing this work. We have lots of great things, but we also need somebody behind this, making sure the supply chain stays in place.
We can’t afford to lose the low end either. The high end will stay; the high end is doing great. But the low end we need also, because we have to have their volume to keep the supply chain in place.
Johnson: How do you expect to raise the visibility of this issue in the next 12 months?
Morgan: I’m talking less than 12 months. Twelve months will already be too late. We’ve already talked to some politicians; the next stage is accessing the data we need to tell our story. We’re already commissioning someone to get that data for us, and when we have it, we’ll share it.
I’ve been talking to suppliers, customers, and board shops around Europe these last few days, and everybody has been very supportive, including people offering help from the U.S. We have really great commitments from everybody: suppliers, board shops, everyone has the same story. After we lock those in, we’ll get in front of politicians. I already have some people lined up; we’re working primarily in the UK, France, and Germany, though I want to get through to someone here in the EU.
The EIPC is not a lobbying body—that’s not what we do. But I do think this issue requires intervention, and I think that EIPC is in the right place and is the right organization to do it on behalf of fabricators. There are other organizations working mainly with the assemblers, OEMs, and other parts of the supply chain. We really support the PCB industry; that’s entirely our focus. It’s at the heart of what we do, and I really believe the PCB is at the heart of electronics. That’s why we’re doing it and that’s why we’ve got to do it.
Johnson: What do you need to accomplish in the next 12 months to be successful in this enterprise?
Morgan: If we a get tariff reverse, that will be a success. Who knows when the war in Ukraine will end. It may go on for another two days, two weeks, two years—nobody knows. There will come a time when the war ends. I want to make sure that when we get to that point, we haven’t lost another big chunk of our business. For me, I want to keep us around €2 billion of turnover. It’s lovely to think about growth but, realistically, I think we have to focus on both maintaining what we have and not losing any more of the supply chain.
It's possible that we may get more supply chain back in Europe, but that won’t happen overnight. Building, for example, an expansion to a copper foil facility, takes not days, weeks, or months—it takes years. To even get the drums takes years, so we cannot do this in a one-year time frame. It’s not possible. It doesn’t matter how much money you have, it’s impossible. You cannot get the equipment. We have to be practical. It’s great to have lofty ambitions, but our ambitions are quite modest. We are focusing on what we can deliver.
Suggested Items
The Evolution of Picosecond Laser Drilling
06/19/2025 | Marcy LaRont, PCB007 MagazineIs it hard to imagine a single laser pulse reduced not only from nanoseconds to picoseconds in its pulse duration, but even to femtoseconds? Well, buckle up because it seems we are there. In this interview, Dr. Stefan Rung, technical director of laser machines at Schmoll Maschinen GmbH, traces the technology trajectory of the laser drill from the CO2 laser to cutting-edge picosecond and hybrid laser drilling systems, highlighting the benefits and limitations of each method, and demonstrating how laser innovations are shaping the future of PCB fabrication.
Day 2: More Cutting-edge Insights at the EIPC Summer Conference
06/18/2025 | Pete Starkey, I-Connect007The European Institute for the PCB Community (EIPC) summer conference took place this year in Edinburgh, Scotland, June 3-4. This is the third of three articles on the conference. The other two cover Day 1’s sessions and the opening keynote speech. Below is a recap of the second day’s sessions.
Day 1: Cutting Edge Insights at the EIPC Summer Conference
06/17/2025 | Pete Starkey, I-Connect007The European Institute for the PCB Community (EIPC) Summer Conference took place this year in Edinburgh, Scotland, June 3-4. This is the second of three articles on the conference. The other two cover the keynote speeches and Day 2 of the technical conference. Below is a recap of the first day’s sessions.
Preventing Surface Prep Defects and Ensuring Reliability
06/10/2025 | Marcy LaRont, PCB007 MagazineIn printed circuit board (PCB) fabrication, surface preparation is a critical process that ensures strong adhesion, reliable plating, and long-term product performance. Without proper surface treatment, manufacturers may encounter defects such as delamination, poor solder mask adhesion, and plating failures. This article examines key surface preparation techniques, common defects resulting from improper processes, and real-world case studies that illustrate best practices.
RF PCB Design Tips and Tricks
05/08/2025 | Cherie Litson, EPTAC MIT CID/CID+There are many great books, videos, and information online about designing PCBs for RF circuits. A few of my favorite RF sources are Hans Rosenberg, Stephen Chavez, and Rick Hartley, but there are many more. These PCB design engineers have a very good perspective on what it takes to take an RF design from schematic concept to PCB layout.