-
-
News
News Highlights
- Books
Featured Books
- pcb007 Magazine
Latest Issues
Current IssueThe Hole Truth: Via Integrity in an HDI World
From the drilled hole to registration across multiple sequential lamination cycles, to the quality of your copper plating, via reliability in an HDI world is becoming an ever-greater challenge. This month we look at “The Hole Truth,” from creating the “perfect” via to how you can assure via quality and reliability, the first time, every time.
In Pursuit of Perfection: Defect Reduction
For bare PCB board fabrication, defect reduction is a critical aspect of a company's bottom line profitability. In this issue, we examine how imaging, etching, and plating processes can provide information and insight into reducing defects and increasing yields.
Voices of the Industry
We take the pulse of the PCB industry by sharing insights from leading fabricators and suppliers in this month's issue. We've gathered their thoughts on the new U.S. administration, spending, the war in Ukraine, and their most pressing needs. It’s an eye-opening and enlightening look behind the curtain.
- Articles
- Columns
- Links
- Media kit
||| MENU - pcb007 Magazine
Essemtec: Manufacturing Moves In-house
December 28, 2022 | Pete Starkey, I-Connect007Estimated reading time: 6 minutes
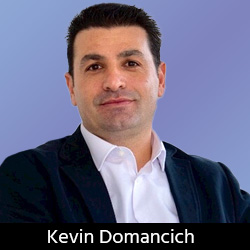
Pete Starkey talks with Kevin Domancich at Essemtec about the company integration within Nano Dimension and how the two companies have pioneered an exciting new end-to-end manufacturing solution that helps customers speed up production, cut costs, and keep their proprietary materials secure. In a world where time to market has become a priority consideration, this universal system has the potential to revolutionize the industry.
Pete Starkey: I’m Pete Starkey at electronica, and I’m delighted to meet Kevin Domancich, the manager of customer application engineering at Essemtec. Kevin, it’s a great pleasure to meet you. Thank you for finding the time to speak with us.
Kevin Domancich: Thank you, it’s my pleasure as well.
Starkey: We are all familiar with the company Essemtec as a Swiss-based manufacturer of versatile surface mount equipment. And we’re all familiar with Nano Dimension as a supplier of equipment for additive manufacturing. The merging between your two companies is a very exciting one; you’re now in a position to offer equipment that’s been jointly developed, which will present a complete end-to-end, fast turn manufacturing solution. Can you give us a little bit of information on this?
Domancich: Nano Dimension pioneers an in-house method of fabricating printed circuit boards (PCBs) and other electronic devices. Thanks to the strategic acquisition of Essemtec, our 3D-printing capabilities are now integrating with the most advanced technology in hardware and software.
Now, you can design your concept on your computer and send it from a CAD drawing directly into the machine. The machine will then automatically print your PCB. Once the PCB is printed, it will be sent through the Essemtec machine, where we can easily dispense and populate your product. With this new technology, we are going to reduce overall production time by cutting out that middle step where you’d normally have to wait for someone to fabricate your PCB.
Now, everything remains at your plant, and you have a fully functional product on your hands. This process is therefore unique.
Starkey: Can you give us an estimate of how long it would take to complete the turnaround process under normal circumstances—from the input of the design information to the delivery of the finished assembly?
Domancich: It depends on the complexity of your PCB. On average, it can take about a day, because 3D printing takes some time to complete. On the other hand, the dispensing and pick and place process take less time based on the number of components to be populated.
Starkey: Depending on the complexity, I assume that most of that time would be spent creating the substrate. Everything else would be set up in advance—the right components, the right feeders. Then typically how long would it take to complete the assembly?
Domancich: For the population of the PCB, Essemtec provides an advanced jetting technology enhanced with pick and place solutions in one machine. Depending on how many components you have—let’s say we have 100 components, we can easily dispense solder jet and pick and place within minutes. The timing varies on the type of medium you are using.
It all depends on the medium used and how populated your PCB is. This process is quite fast because the Essemtec pick and place machine is equipped with combined processes. The machine can easily handle solder jetting of the 01005 component. For the 01005, we can jet a solder dot of 280 to 300 microns. This is equivalent to around 3 nL of volume.
Starkey: So, this system is based on long-established skill and expertise. It’s the integration of your technology with the Nano Dimension technologies to make this complete solution.
Domancich: Yes. Actually, with Nano Dimension, we’ve enlarged our portfolio beyond just populating on PCBs; now we can produce a PCB, dispense, and populate on a combined solution.
Starkey: Finding solutions to shorten the time to market is critical in today’s environment.
Domancich: Exactly. And it’s more important than ever to make sure your proprietary materials are not exposed to the outside world. A lot of customers nowadays are exposing their technology intelligence by sending documents or specifications to third parties. Unfortunately, information could leak uncontrolled. By keeping the assembly capabilities in your company, your information remains secure.
Starkey: What sort of companies are excited about this system?
Domancich: We have a range of companies that have shown interest in this combined solution of a 3D printer and an all-in-one solution (dispensing and pick and place). This type of solution is mainly used for academia, research, and development. On the other hand, the dispensing and pick and place solutions are largely used for high mix low volume to medium volume applications. With big companies, we’re able to offer a scalable solution.
For big companies, we can provide inline assembly solutions that can be adapted to various market specifications. Our equipment was recently IPC CFX certified, which enables it to perform Industry 4.0 standards.
Starkey: I was going to ask what market sectors this technology would fit into, but from what you’ve said, it’s universal. It could fit anywhere.
Domancich: Exactly, we can fit in any market sector from small companies to large OEMs, for low, medium, and high volume. We have proven solutions in medical, aerospace, automotive, and smart concepts applications, to name just a few of them.
Nolan Johnson: I can’t help but think that the entire production process could easily fit inside the shipping time that you have in the normal outsourcing model.
Domancich: Correct, you’re going to be faster. Using our equipment with combined processes will reduce the time to market, optimize your production costs, and maintain the assembly flexibility.
Johnson: Now you can do it all from start to finish in the time that you would have had set aside just to send your boards and your components to the appropriate outsourced companies. The time it would spend on the UPS truck is now in manufacturing.
Domancich: That’s correct.
Johnson: I get the sense also from what you’re describing that this sort of looks like a return to what we would call a “captive facility” for an OEM. Is this the kind of customer you tend to sell to? You mentioned large companies and small companies, but are they mostly contract manufacturing type companies? Or are you actually selling into OEMs so that they have a captive facility?
Domancich: We have a diverse range of customers, but yes, we are working with more and more OEMs. The appeal of this technology is getting more contract manufacturing and more OEMs. The agility of our equipment enables an incredibly large number of applications fitted into various assembly lines.
Johnson: That makes sense, considering the security aspect.
Domancich: Yes, correct, the entire process remains within the company.
Starkey: Certainly, when it comes to validating a new design, you can save a lot of time on a prototype with this system. If at the end of the process you power up the assembly and think it’s not quite what you wanted, you’ll be able to go back to the loop and make the necessary changes with a slight modification to the design. With a more traditional route, doing that would put days or weeks onto the lead time; with this system, you can you easily produce version 2 by the next day.
Domancich: Correct, our system is offering an agile combined process that enables easy changes or adjustments based on specifications or requests. The user-friendly software enables to do easy correction and monitor the process according to standards.
Starkey: Well, I think the prospect is very exciting and I thank you for the thorough overview of this new all-in-one system. We’ve covered a lot of a lot of ground in a very short time, Kevin. Thank you very much indeed.
Domancich: Thank you very much for your time.
Suggested Items
Driving Innovation: Direct Imaging vs. Conventional Exposure
07/01/2025 | Simon Khesin -- Column: Driving InnovationMy first camera used Kodak film. I even experimented with developing photos in the bathroom, though I usually dropped the film off at a Kodak center and received the prints two weeks later, only to discover that some images were out of focus or poorly framed. Today, every smartphone contains a high-quality camera capable of producing stunning images instantly.
Hands-On Demos Now Available for Apollo Seiko’s EF and AF Selective Soldering Lines
06/30/2025 | Apollo SeikoApollo Seiko, a leading innovator in soldering technology, is excited to spotlight its expanded lineup of EF and AF Series Selective Soldering Systems, now available for live demonstrations in its newly dedicated demo room.
Indium Corporation Expert to Present on Automotive and Industrial Solder Bonding Solutions at Global Electronics Association Workshop
06/26/2025 | IndiumIndium Corporation Principal Engineer, Advanced Materials, Andy Mackie, Ph.D., MSc, will deliver a technical presentation on innovative solder bonding solutions for automotive and industrial applications at the Global Electronics A
Fresh PCB Concepts: Assembly Challenges with Micro Components and Standard Solder Mask Practices
06/26/2025 | Team NCAB -- Column: Fresh PCB ConceptsMicro components have redefined what is possible in PCB design. With package sizes like 01005 and 0201 becoming more common in high-density layouts, designers are now expected to pack more performance into smaller spaces than ever before. While these advancements support miniaturization and functionality, they introduce new assembly challenges, particularly with traditional solder mask and legend application processes.
Knocking Down the Bone Pile: Tin Whisker Mitigation in Aerospace Applications, Part 3
06/25/2025 | Nash Bell -- Column: Knocking Down the Bone PileTin whiskers are slender, hair-like metallic growths that can develop on the surface of tin-plated electronic components. Typically measuring a few micrometers in diameter and growing several millimeters in length, they form through an electrochemical process influenced by environmental factors such as temperature variations, mechanical or compressive stress, and the aging of solder alloys.