-
- News
- Books
Featured Books
- pcb007 Magazine
Latest Issues
Current IssueInventing the Future with SEL
Two years after launching its state-of-the-art PCB facility, SEL shares lessons in vision, execution, and innovation, plus insights from industry icons and technology leaders shaping the future of PCB fabrication.
Sales: From Pitch to PO
From the first cold call to finally receiving that first purchase order, the July PCB007 Magazine breaks down some critical parts of the sales stack. To up your sales game, read on!
The Hole Truth: Via Integrity in an HDI World
From the drilled hole to registration across multiple sequential lamination cycles, to the quality of your copper plating, via reliability in an HDI world is becoming an ever-greater challenge. This month we look at “The Hole Truth,” from creating the “perfect” via to how you can assure via quality and reliability, the first time, every time.
- Articles
- Columns
- Links
- Media kit
||| MENU - pcb007 Magazine
Estimated reading time: 3 minutes
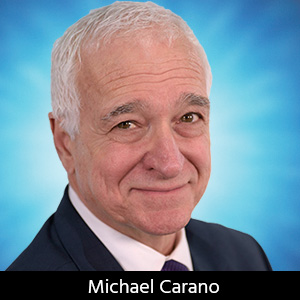
Contact Columnist Form
Trouble in Your Tank: Revisiting the Art and Science of Photoresist Stripping
Considerable progress has been made in the field of consumer and industrial electronics; today’s devices are reasonably priced and efficient, yet small and portable. However, these advances create challenges for the manufacturers of the components necessary to produce these smaller, more portable devices.
PCB designers, for example, must attempt to squeeze increasingly more amounts of information onto a smaller board. In practical terms, this means that circuits are becoming more compact; circuit lines and the spaces between them are becoming finer. As the distances between these lines decrease, copper overplating is more likely to have a deleterious effect on photoresist stripping. The number of unstripped residues tends to increase at the very small distances between conductor lines on these new circuits. Under these conditions, conventional photoresist strippers are ineffective and the amount of photoresist remaining on the substrate after stripping increases. Complete photoresist stripping is needed to avoid shorts on costly fine-line PCBs. In addition, some fabricators lack proper control of the plating process. Coupled with thinner resist film, this leads to overplating—and overplated copper and/or tin will entrap resist under the heavily plated features.
Overplating and Entrapped Resist
An example of overplating is shown in Figure 1. The overplated condition, coupled with tight spacing, will make clean resist stripping a major concern.
Another example of overplating and entrapped resist is shown is Figure 2. Of course, part of the issue here is tighter line-and-space requirements. This issue appears primarily in higher-density circuit designs driven by miniaturization. These difficult circuit geometries can result in overplating the copper, which increases the instances of resist residues. This in turn leads to various defects. If the photoresist stripping is incomplete, the photoresist left behind will protect the underlying copper from etch. This results in a circuitry “short,” where copper bridges an area between two circuit lines that were meant to be isolated from each other, leading to PCB failure and reduced yields. More effective photoresist stripping is needed to avoid these manufacturing pitfalls.
One way to remove these entrapped particles is to employ a phase-transfer catalyst (PTC). Quaternary ammonium salts (quats) are the compounds most commonly used as PTCs. These compounds transport free hydroxide ions (OH-) into the photoresist polymeric structure, network, or interphase boundary with the liquid medium of the solvated catalyst. The hydroxide ions then serve to chemically break the photoresist network apart. Concentrations are critical, as are the selection of the additives to break up the resist into small particles. Thus, optimizing the resist stripper formulation is essential to ensure a smaller particle size. Regardless, overplated circuit traces will present a significant challenge in clean removal of entrapped resist. More on this later.
Perhaps high spray pressures in the resist stripping chamber or the final rinse will improve one’s chances of entrapped resist particle removal. Other remedies (not necessarily recommended by the author) include a double pass through the stripper solution or having a separate offline tank with a resist stripping formulation capable of solvating small entrapped particles. Employing a plasma etch to successfully remove these particles is also an option. But due to the additional process times required to deploy these methods, there is a risk of attacking the tin etch resist, as presented in Part 2 of this series on resist stripping.
As for resist stripping effectiveness, effective stripping of a photoresist implies the chemical destruction of the photoresist’s polymeric network. Through this chemical dislodging of chemical structures, removal of small photoresist particulates becomes feasible.
Most of today’s photoresist strippers are water-based and contain multiple components, such as amines, solvents, and quaternary compounds. Many of these off-the-shelf products were developed prior to the need for these higher density designs. Most will deliver large particulates or lead to a sheeting of the resist. Because of this characteristic, they fail to strip photoresist from difficult geometries and cause an overall decrease of yields in PCB production.
We have found that it is possible to achieve such a dislodgment down to very small particulates with a water-extended concentrate. This involves the following:
A specific ratio of quat and solvent is necessary to achieve outstanding results. At the same time, the presence of amine in a specific range will facilitate very good results as well. Thereby, a PTC situation is achieved in the attacked polymeric structures of the photoresist, giving cause to an especially effective attack on the polymer network. This action allows for the exposed resist film to break up into finer particles. The spray action within the resist chamber and subsequent rinses help to further dislodge particles, effecting a clean removal.
This column originally appeared in the December 2022 issue of PCB007 Magazine.
More Columns from Trouble in Your Tank
Trouble in Your Tank: Metallizing Flexible Circuit Materials—Mitigating Deposit StressTrouble in Your Tank: Can You Drill the Perfect Hole?
Trouble in Your Tank: Yield Improvement and Reliability
Trouble in Your Tank: Causes of Plating Voids, Pre-electroless Copper
Trouble in Your Tank: Organic Addition Agents in Electrolytic Copper Plating
Trouble in Your Tank: Interconnect Defect—The Three Degrees of Separation
Trouble in Your Tank: Things You Can Do for Better Wet Process Control
Trouble in Your Tank: Processes to Support IC Substrates and Advanced Packaging, Part 5