-
- News
- Books
Featured Books
- pcb007 Magazine
Latest Issues
Current IssueSales: From Pitch to PO
From the first cold call to finally receiving that first purchase order, the July PCB007 Magazine breaks down some critical parts of the sales stack. To up your sales game, read on!
The Hole Truth: Via Integrity in an HDI World
From the drilled hole to registration across multiple sequential lamination cycles, to the quality of your copper plating, via reliability in an HDI world is becoming an ever-greater challenge. This month we look at “The Hole Truth,” from creating the “perfect” via to how you can assure via quality and reliability, the first time, every time.
In Pursuit of Perfection: Defect Reduction
For bare PCB board fabrication, defect reduction is a critical aspect of a company's bottom line profitability. In this issue, we examine how imaging, etching, and plating processes can provide information and insight into reducing defects and increasing yields.
- Articles
- Columns
- Links
- Media kit
||| MENU - pcb007 Magazine
Real Time with… IPC APEX EXPO 2023: Jesse Session Talks R&D at Taiyo
January 11, 2023 | Nolan Johnson, I-Connect007Estimated reading time: 6 minutes
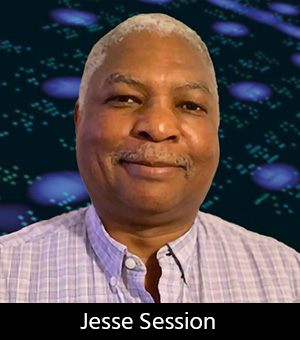
Nolan Johnson checks in with Taiyo America’s Technical Manager, Jesse Session, about the new and exciting developments cooking in Taiyo’s R&D department. The company’s groundbreaking inkjet solder mask product line is expanding to meet the needs of customers looking for updated color options that retain the same quality standards and reliability that have come to define Taiyo’s offerings. But why stop there? Taiyo is also whipping up its own flavor of thermal management products to help turn down the heat on PCB components, as well as transitioning to more sustainable packaging.
Audio Transcript
Nolan Johnson: Nolan Johnson here for Real Time with… IPC APEX EXPO: Preview Edition. I’m talking right now with the technical manager at Taiyo, Jesse Session. Jesse, welcome; as we’re getting ready for the show and in your role as technical manager, I’ll go straight to the point: What’s new in R&D at Taiyo?
Jesse Session: Thank you. We have exciting projects right now. Number one, we’re working on—of course—new inkjet solder mask-type products. As many of you might know, we introduced inkjet solder mask a few years ago. The product line is just growing; now, we have customers who are looking for inkjet solder masks that are not only different colors but have the same properties and performance as our standard solder mask. From an R&D perspective, this is a big challenge. It’s very exciting. I have my staff working on it. Although we have frustrations sometimes, that end goal is right there.
Johnson: The development around things like new formulations has got to be a lot like Edison’s approach to inventing: You try a lot of things and figure out what doesn’t work first.
Session: That’s right, I look at it like cooking. You have your favorite chili recipe, and it’s trial and error: You try different spices, try different salts; you keep going until you get that perfect taste, and then that’s your solid recipe that you keep forever.
Johnson: How many different formulations might you have in development?
Session: Right now, we have about 12 formulations in development, which is pretty big considering we’re a small group relative to the rest of the tile groups, which probably have hundreds of formulations in development.
Johnson: Right, that certainly can put a bunch of new inkjet solder mask products out there for you in 2023.
Session: One of the exciting projects that we’ve been working on—it’s kind of like my baby—is thermal management products. Nolan, as you know, things are starting to get smaller and smaller, and as these electronics reduce in size, they tend to generate more heat due to the power demands. Traditional methods using fans or heat sinks—they’re really not compatible with the way technology is going because they add weight to the product. Well, at Taiyo America, we developed a management product that we call “Thermal Cool,” and we introduced it, I believe, at IPC last year. Thermal Cool is actually a coating that you can put in selective areas that will draw the heat away from the components on the circuit board. What makes this important is that it’s actually a lighter weight alternative to heat sinks, and you can put it exactly where you want. We’ve achieved thermal conductivities as high as 10.2 watts per meter Kelvin. Given the fact that traditional coatings are down around 2 to 3 watts per meter Kelvin, we’re about 50 times more than the standard coating you’d find on the market. And now we’re coming out with different versions for different applications, such as for via fill, and some applications, such as microelectronics, where we can actually put small droplets in different areas. Definitely a growth for us.
Johnson: And how’s the customer acceptance for that?
Session: Right now, customers are evaluating the product and they’re finding that, yes, it’s drawing out the amount of heat that they want away from the components. I just made 20-plus samples for various customers to evaluate, which is a lot, considering I’m doing it in the lab.
Johnson: How effective is this coating in alleviating the need for a physical heat sink?
Session: Well, right now it has the possibility of eliminating the heat sink, but most of our customers—the people evaluating it—they’re looking at reducing the thickness of the heat sink as a first step, so it’s going to work in combination with the heat sink. But eventually, yeah, if we can get the thermal conductivity even higher—push the envelope—it could possibly eliminate the heat sink.
Johnson: I’m sure there’s got to be at least one more thing going on in R&D at Taiyo.
Session: Yeah, the most important thing going on right now we’re looking at is sustainability. I kind of chuckled at that because I went to a trade show for coatings earlier this year, and that was the big topic; then I come back home and all of a sudden: the topic of sustainability. It’s not only an R&D project, but it’s our entire operations group, our sales and marketing groups—we’re all collaborating on this. We’re switching our packaging from the traditional plastic containers to a metallic “bag,” similar to what you might find in the store with the drink pouches that the kids use. The best thing about these metallic bags? We can take them and have them repurposed so they can be used as something else. I don’t really want to call it “recycling,” per say, but it’s along those same lines. It’s a great concept, and we’re probably a few months away from introducing them to the marketplace. We’re going to start with our partner package, so the Part B of our solder mask package; we’ll see how that goes, and eventually we will transition the entire solder mask kit to these pouches. That’s probably going to be within the next year to year and a half that that gets taken care of, but it’s really exciting.
Johnson: What’s the impact on the customer’s usage?
Session: In actual usage, they’ll see very little impact. The amount of material that they can get out of one of these bags, they’ll find, is more than out of traditional bucket, and by “more” I’m talking about a couple of grams—I’m not talking about something that would significantly impact the performance of the solder mask. But it is a clean solution to everybody’s headache of having waste and waste disposal.
Johnson: It is a little unusual to have packaging be an interesting topic for our industry. Jesse, I assume that these topics will be a part of your presence at APEX here in January.
Session: Absolutely, you can talk to any of us at the booth about them and we’ll be happy to answer any questions or concerns. We’ll be around; it’s better to talk to customers than twiddling your thumbs.
Johnson: And will we be able to find you there at the booth at APEX?
Session: I do attend some of the committee meetings and some of the technical presentations, but if you need to talk to me, just grab one of the people in the booth and they’ll hunt me down.
Johnson: Thanks for taking the time to speak with us today.
Session: Absolutely, thank you.
Johnson: Here with Jesse Session, the technical manager at Taiyo, I’m Nolan Johnson. This is Real Time with… IPC APEX EXPO. Thanks for listening.
Testimonial
"In a year when every marketing dollar mattered, I chose to keep I-Connect007 in our 2025 plan. Their commitment to high-quality, insightful content aligns with Koh Young’s values and helps readers navigate a changing industry. "
Brent Fischthal - Koh YoungSuggested Items
Indium Corporation Promotes Two Leaders in EMEA (Europe, Middle East, and Africa) Markets
08/05/2025 | Indium CorporationWith its commitment to innovation and growth through employee development, Indium Corporation today announced the promotions of Andy Seager to Associate Director, Continental Sales (EMEA), and Karthik Vijay to Senior Technical Manager (EMEA). These advancements reflect their contributions to the company’s continued innovative efforts with customers across Europe, the Middle East, and Africa (EMEA).
MacDermid Alpha Electronics Solutions Unveils Unified Global Website to Deepen Customer, Talent, and Stakeholder Engagement
07/31/2025 | MacDermid Alpha Electronics SolutionsMacDermid Alpha Electronics Solutions, the electronics business of Elements Solutions Inc, today launched macdermidalpha.com - a unified global website built to deepen digital engagement. The launch marks a significant milestone in the business’ ongoing commitment to delivering more meaningful, interactive, and impactful experiences for its customers, talent, and stakeholders worldwide.
KOKI to Showcase Analytical Services and New HF1200 Solder Paste at SMTA Guadalajara 2025
07/31/2025 | KOKIKOKI, a global leader in advanced soldering materials and process optimization services, will exhibit at the SMTA Guadalajara Expo & Tech Forum, taking place September 17 & 18, 2025 at Expo Guadalajara, Salón Jalisco Halls D & E in Guadalajara, Mexico.
Weller Tools Supports Future Talent with Exclusive Donation to SMTA Michigan Student Soldering Competition
07/23/2025 | Weller ToolsWeller Tools, the industry leader in hand soldering solutions, is proud to announce its support of the upcoming SMTA Michigan Expo & Tech Forum by donating a limited-edition 80th Anniversary Black Soldering Set to the event’s student soldering competition.
Koh Young Appoints Tom Hattori as President of Koh Young Japan
07/21/2025 | Koh YoungKoh Young Technology, the global leader in True 3D measurement-based inspection solutions, announced the appointment of Tom Hattori as President of Koh Young Japan (JKY).