SEHO: New Functions Increase Cost-Efficiency and Energy-Efficiency in Wave Soldering Processes
January 27, 2023 | SEHOEstimated reading time: 1 minute
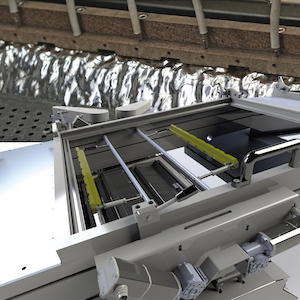
SEHO North America, Inc., a worldwide leading supplier of complete solutions for soldering processes and automated production lines, is one of the most innovative companies in the industry. Some of these innovations are aimed at taking cost-efficiency and energy-efficiency in the wave soldering process to a new level.
New pulsar emitters allow remarkably higher flexibility in the preheat area. Configuring emitters individually instead of using entire segments helps to realize the shortest distances between assemblies. Thus, there is virtually no wait time required between assemblies with different heat energy demands, ensuring highest energy-efficiency. This preheating concept allows for the cost-efficient and sustainable manufacture of large series as well as a batch size of one.
SEHO’s new automatic nozzle height adjustment provides higher flexibility in the soldering area of wave solder systems, particularly if a large number of different variants are to be manufactured. The height of each solder nozzle can be adjusted via the software, which allows creating the optimal product-specific distance between the circuit board and solder nozzle. This innovative function provides independence from the workpiece carrier or assembly design, a remarkably larger process window, maximum flexibility and process reliability.
Consistent height of the solder wave is crucial for wave soldering processes. SEHO provides the first automatic wave height measurement, built into the soldering section of the MWS 2300. This feature is based on a contact measurement that produces reliable results and processes for laminar as well as turbulent solder waves. Based on the measuring results, the wave height is automatically regulated within adjustable tolerances. The system thereby ensures the same height across the entire wave width at any time. The complete logging of all measured values and parameters also provides a proof of quality of the manufactured products.
Suggested Items
Driving Innovation: Direct Imaging vs. Conventional Exposure
07/01/2025 | Simon Khesin -- Column: Driving InnovationMy first camera used Kodak film. I even experimented with developing photos in the bathroom, though I usually dropped the film off at a Kodak center and received the prints two weeks later, only to discover that some images were out of focus or poorly framed. Today, every smartphone contains a high-quality camera capable of producing stunning images instantly.
Hands-On Demos Now Available for Apollo Seiko’s EF and AF Selective Soldering Lines
06/30/2025 | Apollo SeikoApollo Seiko, a leading innovator in soldering technology, is excited to spotlight its expanded lineup of EF and AF Series Selective Soldering Systems, now available for live demonstrations in its newly dedicated demo room.
Indium Corporation Expert to Present on Automotive and Industrial Solder Bonding Solutions at Global Electronics Association Workshop
06/26/2025 | IndiumIndium Corporation Principal Engineer, Advanced Materials, Andy Mackie, Ph.D., MSc, will deliver a technical presentation on innovative solder bonding solutions for automotive and industrial applications at the Global Electronics A
Fresh PCB Concepts: Assembly Challenges with Micro Components and Standard Solder Mask Practices
06/26/2025 | Team NCAB -- Column: Fresh PCB ConceptsMicro components have redefined what is possible in PCB design. With package sizes like 01005 and 0201 becoming more common in high-density layouts, designers are now expected to pack more performance into smaller spaces than ever before. While these advancements support miniaturization and functionality, they introduce new assembly challenges, particularly with traditional solder mask and legend application processes.
Knocking Down the Bone Pile: Tin Whisker Mitigation in Aerospace Applications, Part 3
06/25/2025 | Nash Bell -- Column: Knocking Down the Bone PileTin whiskers are slender, hair-like metallic growths that can develop on the surface of tin-plated electronic components. Typically measuring a few micrometers in diameter and growing several millimeters in length, they form through an electrochemical process influenced by environmental factors such as temperature variations, mechanical or compressive stress, and the aging of solder alloys.