IT, Electronics Innovators Procurri and Igneo Announce Partnership
February 24, 2023 | PRNewswireEstimated reading time: 1 minute
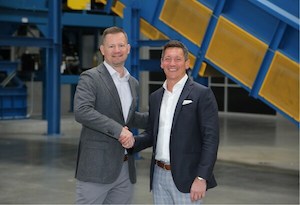
Procurri, a global leader in IT Lifecycle Services and data center hardware, has engaged Igneo Technologies, a subsidiary of Korea Zinc and a global leader in the electronics downstream space, to support Procurri's global Lifecycle Service operations, by providing end-of-life recycling and e-waste refining services. Utilizing the combined geographic footprint of Procurri, Igneo & Korea Zinc, along with other strategic partners, the two companies are uniquely positioned to provide turnkey and vertically integrated global recycling solutions for their customers and partners.
"We searched for a partner that had a global footprint, the ability to quickly scale, and who shares our core ESG values surrounding the environment and our commitment as an organization to help make the world a better place," said Evrim Eravci, Global President, Lifecycle Services at Procurri. "Igneo, and their parent company Korea Zinc, share similar core values to Procurri; are driven by providing solutions that are built around environmental stewardship, sustainability, and supporting the circular economy."
IT equipment managed by Procurri is evaluated for refurbishment and reusability, prioritizing reuse over recycle. Equipment deemed end-of-life will, where practical, now be processed by Igneo or Korea Zinc, leveraging their state-of-the-art facilities. End-of-life electronics will be separated into plastics, ferrous metals, non-ferrous metals, and precious metal bearing. Precious metals and copper-based commodities are processed at Igneo's facility in France or at Korea Zinc's Onsan smelter. Plastics, steel and aluminium are sent to end processors to create new raw products that are sold back into the global supply chain to manufacture new products.
"Our goals around the circular economy and building a best-in-class global recycling company very much align with Procurri," said Danish Mir, Igneo's Chief Executive Officer. "The core services we provide are very different but align around minimizing waste and giving resources a second, third and fourth chance as products."
Testimonial
"We’re proud to call I-Connect007 a trusted partner. Their innovative approach and industry insight made our podcast collaboration a success by connecting us with the right audience and delivering real results."
Julia McCaffrey - NCAB GroupSuggested Items
Advancing Electrolytic Copper Plating for AI-driven Package Substrates
08/05/2025 | Dirk Ruess and Mustafa Oezkoek, MKS’ AtotechThe rise of artificial intelligence (AI) applications has become a pivotal force driving growth in the server industry. Its challenging requirements for high-frequency and high-density computing are leading to an increasing demand for development of advanced manufacturing methods of package substrates with finer features, higher hole densities, and denser interconnects. These requirements are essential for modern multilayer board (MLB) designs, which play a critical role in AI hardware. However, these intricate designs introduce considerable manufacturing complexities.
Statement from the Global Electronics Association on the July 2025 Tariff on Copper Foil and Electronics-Grade Copper Inputs
07/31/2025 | Global Electronics AssociationWe are disappointed by today’s decision to impose a 50% tariff on imported copper foil and other essential materials critical to electronics manufacturing in the United States.
Trouble in Your Tank: Metallizing Flexible Circuit Materials—Mitigating Deposit Stress
08/04/2025 | Michael Carano -- Column: Trouble in Your TankMetallizing materials, such as polyimide used for flexible circuitry and high-reliability multilayer printed wiring boards, provide a significant challenge for process engineers. Conventional electroless copper systems often require pre-treatments with hazardous chemicals or have a small process window to achieve uniform coverage without blistering. It all boils down to enhancing the adhesion of the thin film of electroless copper to these smooth surfaces.
Considering the Future of Impending Copper Tariffs
07/30/2025 | I-Connect007 Editorial TeamThe Global Electronics Association is alerting industry members that a potential 50% tariff on copper could hit U.S. electronics manufacturers where it hurts.
Connect the Dots: Sequential Lamination in HDI PCB Manufacturing
07/31/2025 | Matt Stevenson -- Column: Connect the DotsAs HDI technology becomes mainstream in high-speed and miniaturized electronics, understanding the PCB manufacturing process can help PCB design engineers create successful, cost-effective designs using advanced technologies. Designs that incorporate blind and buried vias, boards with space constraints, sensitive signal integrity requirements, or internal heat dissipation concerns are often candidates for HDI technology and usually require sequential lamination to satisfy the requirements.