-
- News
- Books
Featured Books
- pcb007 Magazine
Latest Issues
Current IssueInventing the Future with SEL
Two years after launching its state-of-the-art PCB facility, SEL shares lessons in vision, execution, and innovation, plus insights from industry icons and technology leaders shaping the future of PCB fabrication.
Sales: From Pitch to PO
From the first cold call to finally receiving that first purchase order, the July PCB007 Magazine breaks down some critical parts of the sales stack. To up your sales game, read on!
The Hole Truth: Via Integrity in an HDI World
From the drilled hole to registration across multiple sequential lamination cycles, to the quality of your copper plating, via reliability in an HDI world is becoming an ever-greater challenge. This month we look at “The Hole Truth,” from creating the “perfect” via to how you can assure via quality and reliability, the first time, every time.
- Articles
- Columns
- Links
- Media kit
||| MENU - pcb007 Magazine
Production Begins at SEL’s $100M Printed Circuit Board Facility
February 27, 2023 | Schweitzer Engineering LaboratoriesEstimated reading time: 2 minutes
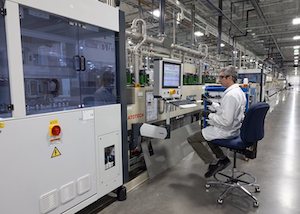
Schweitzer Engineering Laboratories will officially begin fabricating printed circuit boards in its new, state-of-the-art facility in Moscow, Idaho, next week.
The 162,000-square-foot facility, which the company began constructing in spring 2021, will house the operation to fabricate the printed circuit boards used in its products that protect, monitor, control and automate electric power systems around the world. SEL manufactures its electronic devices in Pullman, Washington; Lewiston, Idaho; Lake Zurich, Illinois; and West Lafayette, Indiana.
“SEL folks with many different backgrounds, educations, interests and experience teamed up to conceive, design, build and produce these essential components of our products—all on our own dime without any government handouts or subsidies,” said President and Chief Technology Officer Edmund O. Schweitzer, III. “We committed to each other to do it right, and now we are safely producing the highest-quality boards in the cleanest plant, using the least amount of resources that science and engineering afford us today. This is $100M of employee owners’ money well spent on creating our future right here at home. I’m proud of our entire team and grateful for the economic and political freedom we enjoy in America.”
SEL has designed a highly automated and environmentally friendly process for manufacturing printed circuit boards that is focused on the health and safety of the community. The facility features zero-discharge water recycling and air filtration technology.
“We went into this not only thinking like a manufacturer but also like community members,” said Senior Director of Vertical Integration Jessi Hall. “So much research, learning and testing has gone into designing our fabrication processes and selecting the best equipment and tools for the job. We are excited to see everything come together and to really start realizing the benefits of these investments.”
The company will employ about 60 people in the facility. The positions range from a variety of engineering roles, including chemical, mechanical, software and computer-aided manufacturing to equipment operators and maintenance workers.
The printed circuit board process begins by layering fiberglass and copper to create a rigid and conductive base. The base board is then sent through a series of automated processes that include drilling, layering, copper plating and etching. The finished boards serve as the foundation of our manufacturing process, where integrated circuits and other electrical components are mounted to the board. Ultimately, the boards and added components serve as the information centers for our SEL products.
The SEL property team served as the contractor for the construction project and partnered with multiple companies local to the Pacific Northwest. The team was able to complete the project within the expected timeline despite global supply chain challenges.
“I am so proud of SEL’s partnership with dedicated subcontractors to find solutions when materials became scarce and timelines unwieldy,” said Vice President of Property Jana Schultheis. “Our construction teams are second to none. It is a proud day to see this factory come online as a result of their ingenuity.”
SEL plans to host a grand opening for the facility later in the year.
Testimonial
"Advertising in PCB007 Magazine has been a great way to showcase our bare board testers to the right audience. The I-Connect007 team makes the process smooth and professional. We’re proud to be featured in such a trusted publication."
Klaus Koziol - atgSuggested Items
The Government Circuit: Navigating New Trade Headwinds and New Partnerships
08/25/2025 | Chris Mitchell -- Column: The Government CircuitAs global trade winds continue to howl, the electronics manufacturing industry finds itself at a critical juncture. After months of warnings, the U.S. Government has implemented a broad array of tariff increases, with fresh duties hitting copper-based products, semiconductors, and imports from many nations. On the positive side, tentative trade agreements with Europe, China, Japan, and other nations are providing at least some clarity and counterbalance.
How Good Design Enables Sustainable PCBs
08/21/2025 | Gerry Partida, Summit InterconnectSustainability has become a key focus for PCB companies seeking to reduce waste, conserve energy, and optimize resources. While many discussions on sustainability center around materials or energy-efficient processes, PCB design is an often overlooked factor that lies at the heart of manufacturing. Good design practices, especially those based on established IPC standards, play a central role in enabling sustainable PCB production. By ensuring designs are manufacturable and reliable, engineers can significantly reduce the environmental impact of their products.
50% Copper Tariffs, 100% Chip Uncertainty, and a Truce
08/19/2025 | Andy Shaughnessy, I-Connect007If you’re like me, tariffs were not on your radar screen until a few months ago, but now political rhetoric has turned to presidential action. Tariffs are front-page news with major developments coming directly from the Oval Office. These are not typical times. President Donald Trump campaigned on tariff reform, and he’s now busy revamping America’s tariff policy.
Global PCB Connections: Understanding the General Fabrication Process—A Designer’s Hidden Advantage
08/14/2025 | Markus Voeltz -- Column: Global PCB ConnectionsDesigners don’t need to become fabricators, but understanding the basics of PCB fabrication can save you time, money, and frustration. The more you understand what’s happening on the shop floor, the better you’ll be able to prevent downstream issues. As you move into more advanced designs like HDI, flex circuits, stacked vias, and embedded components, this foundational knowledge becomes even more critical. Remember: the fabricator is your partner.
MKS’ Atotech to Participate in IPCA Electronics Expo 2025
08/11/2025 | AtotechMKS Inc., a global provider of enabling technologies that transform our world, announced that its strategic brands ESI® (laser systems) and Atotech® (process chemicals, equipment, software, and services) will showcase their latest range of leading manufacturing solutions for printed circuit board (PCB) and package substrate manufacturing at the upcoming 17th IPCA Show to be held at Pragati Maidan, New Delhi from August 21-23, 2025.