-
-
News
News Highlights
- Books
Featured Books
- pcb007 Magazine
Latest Issues
Current IssueThe Hole Truth: Via Integrity in an HDI World
From the drilled hole to registration across multiple sequential lamination cycles, to the quality of your copper plating, via reliability in an HDI world is becoming an ever-greater challenge. This month we look at “The Hole Truth,” from creating the “perfect” via to how you can assure via quality and reliability, the first time, every time.
In Pursuit of Perfection: Defect Reduction
For bare PCB board fabrication, defect reduction is a critical aspect of a company's bottom line profitability. In this issue, we examine how imaging, etching, and plating processes can provide information and insight into reducing defects and increasing yields.
Voices of the Industry
We take the pulse of the PCB industry by sharing insights from leading fabricators and suppliers in this month's issue. We've gathered their thoughts on the new U.S. administration, spending, the war in Ukraine, and their most pressing needs. It’s an eye-opening and enlightening look behind the curtain.
- Articles
- Columns
- Links
- Media kit
||| MENU - pcb007 Magazine
Focus Tech Announces New Website and Product Showcase
March 28, 2023 | Focus TechEstimated reading time: 1 minute
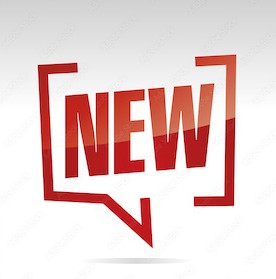
Tempe, Arizona based Focus Tech announces a new website that focuses on its offering in specialty chemical and process control system manufacturing for the printed circuit board and general metal finishing industries. Focus Tech is the only supplier to the PCB industry that designs and manufactures both process chemicals and control systems.
“Focus Tech is proud to roll-out a new company website this week,” commented Scott Campbell, Focus Tech founder and president. “The site www.focustechchem.com features over 50 product pages for a variety of chemicals we manufacture for a variety of applications. In two clicks, viewers will find technical information on what we offer. We designed it from the ground up to make it easy to access and navigate all our information.”
Focus Tech product lines include anti-foam, anti-tarnish, copper cleaners, etch chemicals, developers, strippers, as well as others commonly used in the manufacture of printed circuit boards and general metal finishing. Focus Tech also manufactures process control equipment and offers a variety of services to PCB fabricators.
Focus Tech is known for responding quickly to customer needs and evolving technology by providing custom chemical formulations and controller designs tailored to the specific requirements of a given process.
Campbell added, “Last year, we moved to a new 47,000 square-foot facility with significant capital investment to improve and streamline all operational, research & development, and manufacturing processes. This has allowed Focus Tech to expand its capabilities particularly in toll blending capabilities. One click on the website will take viewers to a robust overview of what we can do in chemical blendings, custom process controls, and services.
“Our new R&D laboratory allows various types of testing including wet titration, atomic absorption and UV/VIS spectroscopy, and cross sections. Our access to a scanning electron microscope and energy dispersive x-ray analysis equipment round out our test services.”
A part of The Redfern Companies, Focus Tech’s products, equipment, and services are distributed by Insulectro leveraging the distributor’s sales team and 11 stocking locations in North America.
Suggested Items
The Evolution of Picosecond Laser Drilling
06/19/2025 | Marcy LaRont, PCB007 MagazineIs it hard to imagine a single laser pulse reduced not only from nanoseconds to picoseconds in its pulse duration, but even to femtoseconds? Well, buckle up because it seems we are there. In this interview, Dr. Stefan Rung, technical director of laser machines at Schmoll Maschinen GmbH, traces the technology trajectory of the laser drill from the CO2 laser to cutting-edge picosecond and hybrid laser drilling systems, highlighting the benefits and limitations of each method, and demonstrating how laser innovations are shaping the future of PCB fabrication.
Day 2: More Cutting-edge Insights at the EIPC Summer Conference
06/18/2025 | Pete Starkey, I-Connect007The European Institute for the PCB Community (EIPC) summer conference took place this year in Edinburgh, Scotland, June 3-4. This is the third of three articles on the conference. The other two cover Day 1’s sessions and the opening keynote speech. Below is a recap of the second day’s sessions.
Day 1: Cutting Edge Insights at the EIPC Summer Conference
06/17/2025 | Pete Starkey, I-Connect007The European Institute for the PCB Community (EIPC) Summer Conference took place this year in Edinburgh, Scotland, June 3-4. This is the second of three articles on the conference. The other two cover the keynote speeches and Day 2 of the technical conference. Below is a recap of the first day’s sessions.
Preventing Surface Prep Defects and Ensuring Reliability
06/10/2025 | Marcy LaRont, PCB007 MagazineIn printed circuit board (PCB) fabrication, surface preparation is a critical process that ensures strong adhesion, reliable plating, and long-term product performance. Without proper surface treatment, manufacturers may encounter defects such as delamination, poor solder mask adhesion, and plating failures. This article examines key surface preparation techniques, common defects resulting from improper processes, and real-world case studies that illustrate best practices.
RF PCB Design Tips and Tricks
05/08/2025 | Cherie Litson, EPTAC MIT CID/CID+There are many great books, videos, and information online about designing PCBs for RF circuits. A few of my favorite RF sources are Hans Rosenberg, Stephen Chavez, and Rick Hartley, but there are many more. These PCB design engineers have a very good perspective on what it takes to take an RF design from schematic concept to PCB layout.