DFM Analysis for Flex and Rigid-flex Design, Part 1
April 17, 2023 | Mark Gallant, DownStream TechnologiesEstimated reading time: 3 minutes
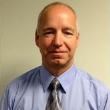
Introduction
Flex and rigid-flex PCB constructions are not new concepts. It has become commonplace as engineers look for alternative circuit packaging for ever-shrinking electronic products. A flat, one-sheet schematic for a straight ribbon cable is analogous to its physical flat substrate. A flat, multi-sheet schematic that details circuitry for a rigid-flex design bears little visual resemblance to its three-dimensional, variable material rigid-flex assembly. However, in both schematic examples, schematic-based analysis tools are applied equally. This same truth also applies to common FR-4-based two-layer or multilayer PCBs.
Today’s PCB analysis tools are applicable across all combinations of rigid PCBs regardless of layer count or size. However, due to the unique properties of flexible substrates and combined flexible and rigid substrates, flexible designs require a specific collection of analysis both functional and manufacture oriented.
Signal integrity analysis such as impedance, coupling, crosstalk and noise is complicated by variable stackups across flexible designs. A single transmission line can be stripline in a rigid-flex area and microstrip in a flex area. Material types and dielectric constants above or below a trace as it traverses a design also vary. While the challenges for signal integrity analysis for flexible designs is worthy of conversation, this article will focus on the current challenges to design-for-manufacture analysis of flex and rigid-flex designs.
Contrasting Rigid PCBs With Flex and Rigid-flex
Some designers design flexible PCBs as simple bendable circuit boards, but there are vast differences between rigid and flexible. Both technologies produce an electrical interconnect function, but are manufactured using different types of materials and processes. They also have varying applications. No need to design a rigid-flexible PCB for the motherboard of a desktop PC, but rigid-flex is required for most medically implanted devices.
A typical rigid PCB is comprised of electrodeposited copper-clad fiberglass substrates bonded together. While there are variations on materials used to bond substrates, it is commonly sheets of cloth pre-impregnated with uncured epoxy. This bonding material composition is not engineered to be flexible. The copper is chemically etched to create a circuit pattern. The hardness of the bonded substrates requires mechanical routing to trim the raw PCBs. All layers of the PCB are commonly identical in size and shape unless cavities, embedded components, or other such exotic construction is present. The rigid PCB layer stackup is identical across the entire PCB area. Solder mask and legend are almost always applied.
Flexible PCBs are comprised of rolled annealed copper over flexible polyimide substrates. Flexible layers or cores are produced with or without adhesives. Adhesiveless flex is prevalent in applications requiring higher performance, while those with adhesives are often found in low layer-count applications. The most common usage is copper foil laminated to a substrate with epoxy or acrylic adhesive. Both substrate material and adhesive are engineered for bending to minimize trace fracture. Like rigid PCBs, a chemical etching process is used to create a circuit pattern. The flexible nature of the materials requires die cutting or “blanking” rather than mechanical routing. Each layer of a flexible double-sided core has an identical shape.
However, multilayer flex is likely to have variations in shape for each layer or core. Flexible PCBs require a thin film insulator over the conductors know as a coverlay. Unlike rigid PCB solder masks, coverlays are die cut much like the flexible layers they insulate. The stackup of a multi-layer flexible PCB can vary across the PCB area. This is especially true with multilayer flex where layer shape varies among the collection of layers or cores. A flexible ground or power plane area is typically crosshatched versus solid for rigid PCBs. The crosshatch reduces potential for fracture of conductors. Alternatively, flexible layers can be shielded with a layer of copper or silver foil. Masking and screening over flexible layers is not rare, but uncommon.
To read this entire article, which appeared in the April 2023 issue of Design007 Magazine, click here.
Testimonial
"The I-Connect007 team is outstanding—kind, responsive, and a true marketing partner. Their design team created fresh, eye-catching ads, and their editorial support polished our content to let our brand shine. Thank you all! "
Sweeney Ng - CEE PCBSuggested Items
Indium Corporation Promotes Two Leaders in EMEA (Europe, Middle East, and Africa) Markets
08/05/2025 | Indium CorporationWith its commitment to innovation and growth through employee development, Indium Corporation today announced the promotions of Andy Seager to Associate Director, Continental Sales (EMEA), and Karthik Vijay to Senior Technical Manager (EMEA). These advancements reflect their contributions to the company’s continued innovative efforts with customers across Europe, the Middle East, and Africa (EMEA).
MacDermid Alpha Electronics Solutions Unveils Unified Global Website to Deepen Customer, Talent, and Stakeholder Engagement
07/31/2025 | MacDermid Alpha Electronics SolutionsMacDermid Alpha Electronics Solutions, the electronics business of Elements Solutions Inc, today launched macdermidalpha.com - a unified global website built to deepen digital engagement. The launch marks a significant milestone in the business’ ongoing commitment to delivering more meaningful, interactive, and impactful experiences for its customers, talent, and stakeholders worldwide.
KOKI to Showcase Analytical Services and New HF1200 Solder Paste at SMTA Guadalajara 2025
07/31/2025 | KOKIKOKI, a global leader in advanced soldering materials and process optimization services, will exhibit at the SMTA Guadalajara Expo & Tech Forum, taking place September 17 & 18, 2025 at Expo Guadalajara, Salón Jalisco Halls D & E in Guadalajara, Mexico.
Weller Tools Supports Future Talent with Exclusive Donation to SMTA Michigan Student Soldering Competition
07/23/2025 | Weller ToolsWeller Tools, the industry leader in hand soldering solutions, is proud to announce its support of the upcoming SMTA Michigan Expo & Tech Forum by donating a limited-edition 80th Anniversary Black Soldering Set to the event’s student soldering competition.
Koh Young Appoints Tom Hattori as President of Koh Young Japan
07/21/2025 | Koh YoungKoh Young Technology, the global leader in True 3D measurement-based inspection solutions, announced the appointment of Tom Hattori as President of Koh Young Japan (JKY).