-
- News
- Books
Featured Books
- pcb007 Magazine
Latest Issues
Current IssueInventing the Future with SEL
Two years after launching its state-of-the-art PCB facility, SEL shares lessons in vision, execution, and innovation, plus insights from industry icons and technology leaders shaping the future of PCB fabrication.
Sales: From Pitch to PO
From the first cold call to finally receiving that first purchase order, the July PCB007 Magazine breaks down some critical parts of the sales stack. To up your sales game, read on!
The Hole Truth: Via Integrity in an HDI World
From the drilled hole to registration across multiple sequential lamination cycles, to the quality of your copper plating, via reliability in an HDI world is becoming an ever-greater challenge. This month we look at “The Hole Truth,” from creating the “perfect” via to how you can assure via quality and reliability, the first time, every time.
- Articles
- Columns
- Links
- Media kit
||| MENU - pcb007 Magazine
Estimated reading time: 3 minutes
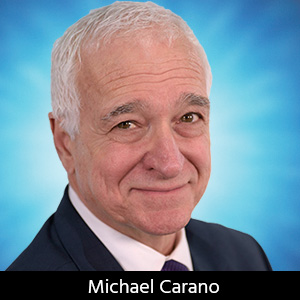
Contact Columnist Form
Trouble in Your Tank: Electrodeposition of Copper, Part 4—Addition Agents
I’ve spent a good part of my career working on disciplines such as process control and technology management, and troubleshooting complex issues in electronics manufacturing. I also spent quite a bit of time formulating chemical processes and understanding the underlying principles of what makes these processes function the way they do. Everything is connected. It’s all about the entire process and its various constituents.
When I first started on this, there were no microvia designs, and most through-hole ratios were easily manageable at 6:1 to 8:1. However, that began to change with the advent of more complex interconnect designs and the requirement of much higher reliability. Soon, we began using insoluble anodes, periodic pulse reverse plating, and new solution additives, and looking differently at solution agitation.
Adding to the complexity of high-end, high reliability printed wiring boards were organic addition agents and their functions related to the physical properties of the electroplated copper deposit. These addition agents are often referred to as leveling agents and brighteners.
The Critical Role of Addition Agents
It is no mystery that without these specially formulated additives, the grain structure and physical properties of the electroplated copper would be less than stellar. You also can assume that without additives, the copper deposit would not be able to withstand the high temperature and mechanical stresses subjected to the board during assembly and service in harsh use environments.
What functions do these additives perform? Are they simple? The short answer is “no.” As stated earlier, the complexity of circuit board designs today, and certainly in the future, requires new and improved plating additives, as well as methods to control them. Traditional through-hole via (direct current) plating parameters and chemistries are not optimal for these more complex structures. Worse yet, metallization of boards with blind and through-hole vias require trade-offs in plating conditions and chemistries to achieve acceptable results on through-holes and in the blind vias.
The additives, which are sometimes referred to as brighteners (for the cosmetic effect on the copper), are formulated with multiple components that can be blended into a single container or added individually as needed. (The latter is recommended for tighter control of the process.) So, what are these components, and what functions do they perform?
In the absence of these organic additives, copper grains grow preferentially on surface defect sites. The copper then grows along preferred copper crystal planes. The plated copper does not exhibit the fine-grained equiaxed structure that is beneficial in providing ductility and tensile strength to the deposit. Under these conditions, the plated copper is dull (matte) and brittle or non-ductile. This causes the plated copper to fracture when stressed, due to the deposit’s poor ductility. In general, additive-free or low-additive plating solutions typically produce deposits with columnar structure, which can lead to cracking in solder float tests (Figure 1).
Copper grows faster on protruding topographies (high spots on the surface), as well as high spots in the via caused by poor drilling. These high spots typically form because of higher primary current density (Figure 2). The primary current distribution is mostly dependent on the board geometry and position in the plating cell, as well as on the absence of properly formulated organic addition agents or low concentration of the addition agents. Fortunately, the function of the organic addition agents, when at the optimum concentration in the electrolyte, mitigates primary current distribution and shifts the plating to secondary current distribution. These addition agents suppress plating on the high-current density areas, which then shifts more of the copper deposition to low-current density areas, such as through-hole and blind vias.
As the defects in Figure 2 show, the plating is primarily being attracted to high spots on the surface, which then adversely affects uniform plating distribution. In summary, organic addition agents are complex and perform critical functions related to the plating process. It is very critical for the process engineer to understand the role of organic addition agents and how they affect plating quality and reliability.
This column originally appeared in the May 2023 issue of PCB007 Magazine.
More Columns from Trouble in Your Tank
Trouble in Your Tank: Metallizing Flexible Circuit Materials—Mitigating Deposit StressTrouble in Your Tank: Can You Drill the Perfect Hole?
Trouble in Your Tank: Yield Improvement and Reliability
Trouble in Your Tank: Causes of Plating Voids, Pre-electroless Copper
Trouble in Your Tank: Organic Addition Agents in Electrolytic Copper Plating
Trouble in Your Tank: Interconnect Defect—The Three Degrees of Separation
Trouble in Your Tank: Things You Can Do for Better Wet Process Control
Trouble in Your Tank: Processes to Support IC Substrates and Advanced Packaging, Part 5