Challenges of DFM Analysis for Flex and Rigid-flex Design, Part 2
May 18, 2023 | Mark Gallant, DownStream TechnologiesEstimated reading time: 2 minutes
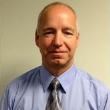
(Editor’s note: This is the second of a three-part series. To read Part 1, click here.)
Flex and Rigid-Flex: Different Layer Types
Everyday rigid FR-4 PCBs have a well-known layer stackup recipe: dielectrics, PCB conductor layers, plane layers, mask, and silkscreen (nomenclature or legend). More advanced layer types may include embedded or screened components or cavities with bonded bare die.
Flex and rigid-flex stackups include those similar to rigid PCBs, such as dielectrics, conductor, mask, and silkscreen layers, but that is where the similarity ends. There are many additional layer types present for this genre of PCB. They include types like coverlay, adhesive, conductive film, conductive foil, conductive adhesive, bondply, and stiffener.
- Coverlay: An external polyimide film that encapsulates and protects flexible conductor layers.
- Adhesive: Bonding agent used to bond copper foil to a polyimide substrate or coverlay.
- Conductive film: Transparent but electrically conductive film found in LCDs, touchscreens, and other optical applications.
- Conductive foil: Thin sheet of copper or silver commonly applied to a flexible PCB as shielding.
- Conductive adhesive: Adhesive applied for electrical interconnect, thermal or structural bonding applications.
- (Flexible) bondply: A polyimide film, coated both sides with B-staged acrylic adhesive. This is essentially a coverlay with adhesive on both sides.
- Stiffener: Blank FR-4 or other material bonded to flexible materials to add stiffness in a specific area.
These layer types are found in typical flexible PCB stackups. The presence of these layer types is not accounted for in most current DFM analysis. This is one area where specific DFM analysis is required. Rigid DFM analysis can detect issues with a solder mask but cannot be used to detect trace corners in a bend area.
Inter-layer Dependencies
While less common in rigid PCBs, flexible PCBs have many inter-layer dependencies that, if not managed well, may lead to manufacturing issues or field failures. The fabrication process used to bond rigid and flexible layers also has its inter-layer dependencies to be managed. Here are a few examples of inter-layer potential issues.
Squeeze-out
Even with best design considerations and best manufacturing practices, adhesive can “squeeze out” and bleed into unwanted areas on adjacent layers. Coverlay adhesive is a common source of squeeze-out that flows during lamination onto conductors, pads, cavities, fingers, or other features. This requires analysis that compares the size of coverlay exposure against the annular ring of adhesive below it.
To read this entire article, which appeared in the May 2023 issue of Design007 Magazine, click here.
Testimonial
"In a year when every marketing dollar mattered, I chose to keep I-Connect007 in our 2025 plan. Their commitment to high-quality, insightful content aligns with Koh Young’s values and helps readers navigate a changing industry. "
Brent Fischthal - Koh YoungSuggested Items
Indium Corporation Promotes Two Leaders in EMEA (Europe, Middle East, and Africa) Markets
08/05/2025 | Indium CorporationWith its commitment to innovation and growth through employee development, Indium Corporation today announced the promotions of Andy Seager to Associate Director, Continental Sales (EMEA), and Karthik Vijay to Senior Technical Manager (EMEA). These advancements reflect their contributions to the company’s continued innovative efforts with customers across Europe, the Middle East, and Africa (EMEA).
MacDermid Alpha Electronics Solutions Unveils Unified Global Website to Deepen Customer, Talent, and Stakeholder Engagement
07/31/2025 | MacDermid Alpha Electronics SolutionsMacDermid Alpha Electronics Solutions, the electronics business of Elements Solutions Inc, today launched macdermidalpha.com - a unified global website built to deepen digital engagement. The launch marks a significant milestone in the business’ ongoing commitment to delivering more meaningful, interactive, and impactful experiences for its customers, talent, and stakeholders worldwide.
KOKI to Showcase Analytical Services and New HF1200 Solder Paste at SMTA Guadalajara 2025
07/31/2025 | KOKIKOKI, a global leader in advanced soldering materials and process optimization services, will exhibit at the SMTA Guadalajara Expo & Tech Forum, taking place September 17 & 18, 2025 at Expo Guadalajara, Salón Jalisco Halls D & E in Guadalajara, Mexico.
Weller Tools Supports Future Talent with Exclusive Donation to SMTA Michigan Student Soldering Competition
07/23/2025 | Weller ToolsWeller Tools, the industry leader in hand soldering solutions, is proud to announce its support of the upcoming SMTA Michigan Expo & Tech Forum by donating a limited-edition 80th Anniversary Black Soldering Set to the event’s student soldering competition.
Koh Young Appoints Tom Hattori as President of Koh Young Japan
07/21/2025 | Koh YoungKoh Young Technology, the global leader in True 3D measurement-based inspection solutions, announced the appointment of Tom Hattori as President of Koh Young Japan (JKY).