Selecting Flex Materials: Do Your Homework
May 25, 2023 | Mike Morando, PFCEstimated reading time: 3 minutes
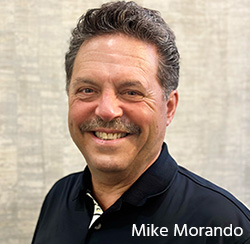
Flex circuits have become more complex in the last decade, driven in part by shrinking designs and components’ higher speeds and signal integrity requirements. Choosing the correct materials for your flex and rigid-flex circuits is a critical part of the design process.
While the layout of the circuit gives us much of the electrical characteristics of the design, your choice of materials can affect the mechanical and electrical characteristics of the circuit. Material choices affect not only the design of the circuit for its environment, but also the manufacturing and assembly processes.
Flex Material Choices: Comprehensive
Your manufacturer’s expertise in flex materials is a true asset, especially with today’s complex multilayer flex and rigid-flex circuits, as well as high speed and signal integrity requirements. In my opinion, it is a requirement to work with your flex manufacturer to communicate all aspects of the circuit, as well as the environment the circuit may encounter.
Here is a list of flex material criteria that you should discuss with your manufacturer.
- Approved process: What materials has your vendor run through their process and approved? All flex vendors etch copper on polyimide, but material availability, equipment, processes, and even humidity can affect processing flex and rigid-flex. Make sure your vendor is familiar with the materials they are proposing and have approved their process. You don’t want your project to become a science experiment.
- UL requirements: Does the flex need to be UL-approved? What material stacks does your vendor have in their UL library? UL approval is affected by the flammability of the adhesives used in their proposed stack.
- Flex stack: Polyimide and copper adhesive-based or adhesive-less? Adhesive-based materials use acrylic adhesive to adhere the copper to the polyimide material. The acrylic adhesive has disadvantages such as via cracking and squeeze-out, and it is more apt to absorb moisture.
- Electrical Characteristics:
- Power: Copper thickness, temperature, and adhesive requirements to meet your current requirements.
- Impedance/signal integrity: Your manufacturer should recommend trace, space, and polyimide thickness, as well as appropriate adhesive requirements.
- Signal speed/low loss: In most cases, standard flex materials can be used up to about 10 Gbps. For speeds above 10 Gbps, your manufacturer should recommend alternative materials. PTFE and LCP are the current popular choices. In addition to the base materials, different adhesives and epoxy films can be used in the lamination process that provide low Dk and thinner material stacks. In addition, there are high-speed coverlays to be considered and tested, depending on the Dk values required.
- Shielding: Material stacks may require shielding either for EMI or for support of high-speed low-loss solutions. You can also add more copper layers, cross hatching, metallized epoxies, and some of the new ferrous cover materials. Adding materials to the stack will always affect the bending of the circuit, so keep that in mind.
- Bend radius: IPC standards recommend the bend radius of a circuit to be 10X the thickness of the material. This likely affects material choices and design. The bend of the circuit may be in a particular section of the circuit only. Share the location of the bend and the number of times the circuit will bend. Your vendor should propose to reduce thicknesses in the required areas by adjusting the material thicknesses.
- Temperature: What temperature is the flex going to encounter? High temperatures affect the adhesives used. Make sure to discuss the environment with your vendor. We have used aluminum for heat dissipation.
- Stiffeners: FR-4 is the most popular stiffener material. It is used for stiffening SMT areas, through-hole connectors, and for ZIF connector interfaces, but we have used additional polyimide as a stiffener, and ceramic and stainless steel, depending on the requirements.
- Coverlay and solder mask: Coverlay (polyimide layer and adhesive over traces) is used in most flex areas, but now with the shrinking of components, the use of solder mask in dense areas has become more common. Remember: Solder mask can crack when bent.
- Plating: We are seeing more requirements for wire bonding on flex. Electroplated soft gold or ENEPIG are the best choices. ENIG is the most common for standard assembly.
Ultimately, after working with your manufacturer and going through this list, you should end up with a material stack that meets all your requirements.
This article originally appeared in the May 2023 issue of Design007 Magazine.
Testimonial
"We’re proud to call I-Connect007 a trusted partner. Their innovative approach and industry insight made our podcast collaboration a success by connecting us with the right audience and delivering real results."
Julia McCaffrey - NCAB GroupSuggested Items
Indium Corporation Promotes Two Leaders in EMEA (Europe, Middle East, and Africa) Markets
08/05/2025 | Indium CorporationWith its commitment to innovation and growth through employee development, Indium Corporation today announced the promotions of Andy Seager to Associate Director, Continental Sales (EMEA), and Karthik Vijay to Senior Technical Manager (EMEA). These advancements reflect their contributions to the company’s continued innovative efforts with customers across Europe, the Middle East, and Africa (EMEA).
MacDermid Alpha Electronics Solutions Unveils Unified Global Website to Deepen Customer, Talent, and Stakeholder Engagement
07/31/2025 | MacDermid Alpha Electronics SolutionsMacDermid Alpha Electronics Solutions, the electronics business of Elements Solutions Inc, today launched macdermidalpha.com - a unified global website built to deepen digital engagement. The launch marks a significant milestone in the business’ ongoing commitment to delivering more meaningful, interactive, and impactful experiences for its customers, talent, and stakeholders worldwide.
KOKI to Showcase Analytical Services and New HF1200 Solder Paste at SMTA Guadalajara 2025
07/31/2025 | KOKIKOKI, a global leader in advanced soldering materials and process optimization services, will exhibit at the SMTA Guadalajara Expo & Tech Forum, taking place September 17 & 18, 2025 at Expo Guadalajara, Salón Jalisco Halls D & E in Guadalajara, Mexico.
Weller Tools Supports Future Talent with Exclusive Donation to SMTA Michigan Student Soldering Competition
07/23/2025 | Weller ToolsWeller Tools, the industry leader in hand soldering solutions, is proud to announce its support of the upcoming SMTA Michigan Expo & Tech Forum by donating a limited-edition 80th Anniversary Black Soldering Set to the event’s student soldering competition.
Koh Young Appoints Tom Hattori as President of Koh Young Japan
07/21/2025 | Koh YoungKoh Young Technology, the global leader in True 3D measurement-based inspection solutions, announced the appointment of Tom Hattori as President of Koh Young Japan (JKY).