Lean vs. TQM vs. Six Sigma
August 2, 2023 | Steve Williams, The Right Approach Consulting LLCEstimated reading time: 1 minute
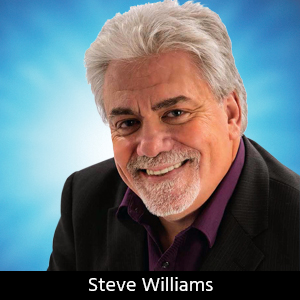
Introduction
Lean, Total Quality Management (TQM), and Six Sigma are three popular methodologies used in business and manufacturing sectors to improve processes, increase efficiency, and reduce waste. While they share some similarities, each approach has its unique focus and tools. Here's a comparison of Lean, TQM, and Six Sigma.
The Founding Fathers
Companies like Toyota are often touted (with good reason) as the gold standard for quality system models. Toyota’s TPS (Toyota Production System) has been highly publicized and has gained increasing acceptance in American manufacturing operations over the last decade or so. What has not been highly publicized is the fact that many of these concepts originated in America, and quality pioneers like W. Edwards Deming had to take their show on the road to Japan only after being rejected by the leaders of American industry. The contributions of such legends as Dr. Deming, Dr. Joseph Juran, Philip Crosby, Dr. Kaoru Ishikawa, Dr. Walter Shewhart, and Shigeo Shingo had such an impact on the world that they truly are the Founding Fathers of modern quality.
“We strive to decide our own fate. We act with self-reliance, trusting in our own abilities. We accept responsibility for our conduct and for maintaining and improving the skills that enable us to produce added value.”
–Excerpt from Toyota Motor Corporation’s internal document, “Toyota Way”
Lean
Lean is a methodology and philosophy that originated from the Toyota Production System (TPS) and is widely used in various industries for process improvement and waste reduction. The core principle of Lean is to maximize value for customers by minimizing or eliminating non-value-added activities or waste. The primary focus of Lean is on creating flow and eliminating waste throughout the entire value stream, from the beginning of a process to its end. Waste, also known as "Muda" in Lean terminology, refers to any activity or process step that does not add value from the customer's perspective. Figure 1 illustrates the eight types of wastes identified in Lean Manufacturing.
To read this entire article, which appeared in the July 2023 issue of PCB007 Magazine, click here.
Testimonial
"Advertising in PCB007 Magazine has been a great way to showcase our bare board testers to the right audience. The I-Connect007 team makes the process smooth and professional. We’re proud to be featured in such a trusted publication."
Klaus Koziol - atgSuggested Items
Gardien Services Installs Customized G93 Flying Probe Tester – Largest Test Area in North America/Europe
08/24/2025 | Gardien GroupGardien Group is proud to announce the successful installation of a customized G93 Flying Probe Test Machine at a major manufacturer in North America. This cutting-edge system features the largest test area of any flying probe tester in North America and Europe, setting a new benchmark for PCB testing capabilities.
ION Storage Systems Launches 'Cornerstone'
08/12/2025 | PRNewswireION Storage Systems, Inc. (ION), a Maryland-based leader in next-generation solid-state battery technology, announces today that it has begun shipping Cornerstone, the first commercial generation of ION's solid-state battery technology, to leading consumer electronics companies.
Benchmark Completes Delivery of the Next Phase of High-Tech Surveillance Solutions for U.S. Customs and Border Protection Share
08/11/2025 | BUSINESS WIREBenchmark Electronics, Inc. proudly announces the successful completion of the delivery of 24 Mobile Vehicle Surveillance Systems with Radar (MVSS-R) for U.S. Customs and Border Protection (CBP) and the Federal Aviation Administration (FAA).
Spirit AeroSystems Announces Definitive Agreement with CTRM for Acquisition of Facility in Subang, Malaysia
08/11/2025 | PRNewswireSpirit AeroSystems Holdings, Inc. announces a purchase agreement to sell its facility and businesses in Subang, Malaysia to Composites Technology Research Malaysia Sdn Bhd (CTRM) for $95,200,000, subject to customary adjustments.
Smart Automation: Pick-and-place Machines—What Matters in 2025
08/12/2025 | Josh Casper -- Column: Smart AutomationWhen people talk about placement technology, they often zero in on speed: How fast can a machine place components? What's the quoted components per hour (CPH)? How many nozzles are on the head? While these metrics matter, on most production floors, the fastest machine on paper isn’t always the most productive.