Book Excerpt: 'The Printed Circuit Designer's Guide to... Manufacturing Driven Design', Chapter 3
August 29, 2023 | I-Connect007 Editorial TeamEstimated reading time: 2 minutes
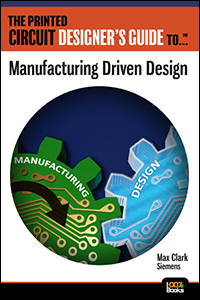
Excerpt from: The Printed Circuit Designer's Guide to... Manufacturing Driven Design, Chapter 3: Why a Change is Needed
What Is Manufacturing Driven Design?
Manufacturing Driven Design is the process of providing full manufacturing awareness within the design process in a manner that allows designers to optimize a design for manufacturing with the first release.
MDD begins at the incarnation of the design idea. In the context of manufacturing, the initial step involves defining the material requirements for the stackup based on the desired electrical requirements. Once the material stackup has been established, the design layout can then be carried out. This simultaneously considers a manufacturer’s process capabilities as well as the traditional design rule check (DRC). A traditional DRC is mainly focused on copper or electrical spacing requirements and does not consider manufacturing needs.
Currently what we call DFM is not necessarily Design for Manufacturing; it’s Manufacturing in spite of Design.
This improved approach of MDD is already implemented in silicon wafer production, where the foundry’s production capabilities are taken into consideration right from the placement of the first pattern during design. This approach resulted from the skyrocketing cost of missing an assignment to a wafer production schedule and having to wait for the next opportunity. Imagine a PCB DFM release process that behaved in the same manner. Consider the financial and environmental savings if PCB manufacturers and design organizations took the same approach. The opportunity for overall PCB manufacturing and environmental improvement would be staggering. The environmental impact of excessive PCB production cannot be measured in the recovery of unneeded bare PCBs alone, but also in the extra board edge trim, wastewater—which contains copper, any number of stripping materials, tin, lead, and much, much more. Analyzing the environmental impact of PCB manufacturing is outside of this book's scope but should not be overlooked.
How Is MDD Different From DFM?
Design for Manufacturing today is seen as a step performed after the design is completed but before it is tooled for manufacturing. Often it is done with limited visibility of the applicable manufacturing partners’ process capabilities for that design technology.
Manufacturing Driven Design facilitates a more advanced level of collaboration, automation, and intelligence to achieve complete manufacturing awareness, surpassing the capabilities of DFM. In its ideal form, MDD covers all manufacturing details that can impact the yield, cost, or reliability of the PCB. It should include the following at a minimum:
- Fabrication process constraints
- Assembly process constraints
- Test process constraints
- Actual PCB material stackup to be used
- Assembly array and fabrication panel configurations
Very few manufacturers today provide their manufacturing process capabilities in a systematic, comprehensive manner to their design customers. Information is conveyed as requested, and only on the specific topic(s) at hand. Even then, it is communicated via email or a PDF of their manufacturing process capabilities specification—nothing that can be automatically acted upon within the design process. MDD provides the infrastructure to share all the necessary manufacturing process capabilities in an automated, synchronized method.
Carrying Capabilities Forward
Understanding the importance of MDD within electronics begins with the end. Ideally, manufacturing processes (fabrication, assembly, test) would be completed with the highest yield and reliability for the lowest cost possible. As the phrase “Manufacturing Driven Design” implies, the manufacturing process capabilities would be introduced at the beginning of the design process, which is carried forward throughout the process. Stated another way, a PCB design is constrained by not only the electrical requirements, but also by the manufacturing process capabilities.
Testimonial
"Advertising in PCB007 Magazine has been a great way to showcase our bare board testers to the right audience. The I-Connect007 team makes the process smooth and professional. We’re proud to be featured in such a trusted publication."
Klaus Koziol - atgSuggested Items
Trouble in Your Tank: Minimizing Small-via Defects for High-reliability PCBs
08/27/2025 | Michael Carano -- Column: Trouble in Your TankTo quote the comedian Stephen Wright, “If at first you don’t succeed, then skydiving is not for you.” That can be the battle cry when you find that only small-diameter vias are exhibiting voids. Why are small holes more prone to voids than larger vias when processed through electroless copper? There are several reasons.
The Government Circuit: Navigating New Trade Headwinds and New Partnerships
08/25/2025 | Chris Mitchell -- Column: The Government CircuitAs global trade winds continue to howl, the electronics manufacturing industry finds itself at a critical juncture. After months of warnings, the U.S. Government has implemented a broad array of tariff increases, with fresh duties hitting copper-based products, semiconductors, and imports from many nations. On the positive side, tentative trade agreements with Europe, China, Japan, and other nations are providing at least some clarity and counterbalance.
How Good Design Enables Sustainable PCBs
08/21/2025 | Gerry Partida, Summit InterconnectSustainability has become a key focus for PCB companies seeking to reduce waste, conserve energy, and optimize resources. While many discussions on sustainability center around materials or energy-efficient processes, PCB design is an often overlooked factor that lies at the heart of manufacturing. Good design practices, especially those based on established IPC standards, play a central role in enabling sustainable PCB production. By ensuring designs are manufacturable and reliable, engineers can significantly reduce the environmental impact of their products.
50% Copper Tariffs, 100% Chip Uncertainty, and a Truce
08/19/2025 | Andy Shaughnessy, I-Connect007If you’re like me, tariffs were not on your radar screen until a few months ago, but now political rhetoric has turned to presidential action. Tariffs are front-page news with major developments coming directly from the Oval Office. These are not typical times. President Donald Trump campaigned on tariff reform, and he’s now busy revamping America’s tariff policy.
Global PCB Connections: Understanding the General Fabrication Process—A Designer’s Hidden Advantage
08/14/2025 | Markus Voeltz -- Column: Global PCB ConnectionsDesigners don’t need to become fabricators, but understanding the basics of PCB fabrication can save you time, money, and frustration. The more you understand what’s happening on the shop floor, the better you’ll be able to prevent downstream issues. As you move into more advanced designs like HDI, flex circuits, stacked vias, and embedded components, this foundational knowledge becomes even more critical. Remember: the fabricator is your partner.