-
- News
- Books
Featured Books
- pcb007 Magazine
Latest Issues
Current IssueInventing the Future with SEL
Two years after launching its state-of-the-art PCB facility, SEL shares lessons in vision, execution, and innovation, plus insights from industry icons and technology leaders shaping the future of PCB fabrication.
Sales: From Pitch to PO
From the first cold call to finally receiving that first purchase order, the July PCB007 Magazine breaks down some critical parts of the sales stack. To up your sales game, read on!
The Hole Truth: Via Integrity in an HDI World
From the drilled hole to registration across multiple sequential lamination cycles, to the quality of your copper plating, via reliability in an HDI world is becoming an ever-greater challenge. This month we look at “The Hole Truth,” from creating the “perfect” via to how you can assure via quality and reliability, the first time, every time.
- Articles
- Columns
- Links
- Media kit
||| MENU - pcb007 Magazine
Estimated reading time: 4 minutes
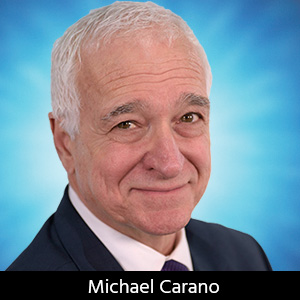
Contact Columnist Form
Trouble in Your Tank: Processes to Support IC Substrates and Advanced Packaging, Part 4
Introduction
In a previous column, the critical process of desmear and its necessity to ensure a clean copper surface connection was presented. Now, my discussion will focus on obtaining a void-free and tightly adherent copper plating deposit on these surfaces.
Metallization
After the desmear process, the task is to insure a continuous, conductive, and void-free deposit on the via walls and capture pad. Today, there are several processes that can be utilized to render vias conductive, including:
- Conventional electroless copper
- Palladium-based direct metallization
- Graphite direct metallization
- Carbon black direct metallization
- Conductive polymer direct metallization
These metallization processes (also known collectively as “making holes conductive” or MHC) are well developed for both plated through-hole and blind via metallization. Direct metallization (DM), in particular, is applicable to horizontal processing, although vertical systems are also used. These processes typically involve the deposition of a conductive coating (palladium, conductive polymer, graphite, carbon black). This step is followed by electrolytic copper; thus, the actual electroless copper step is eliminated.
These processes have been presented and thoroughly discussed elsewhere1. While direct metallization processes may reach certain limitations for use with very high aspect ratio rigid circuit boards, these processes are very efficient and effective for HDI. Direct metallization systems primarily function by coating the substrate, as opposed to a true chemical reaction that is inherent in conventional electroless copper plating processes, such as electroless copper. Contrarians of direct metallization point to sheet resistance measurements of the direct metallization coatings vs. electroless copper. Yet, while the DM films are somewhat less conductive, most of the direct metallization processes have resistances in the neighborhood of 5–25 ohms square. This is more than sufficient to promote electroplating propagation in blind vias and mid- to high-aspect ratio through-holes.
Another advantage that DM processes have over conventional electroless copper is the ability of these DM films to render higher performance materials conductive without overly aggressive desmear tactics. It is well known that electroless copper requires sufficient roughening of the resin to promote palladium adsorption and to insure adhesion of the subsequent copper deposit. However, most direct metallization processes require only minimal resin roughening to promote adhesion. This is because the more popular systems commercially available today rely on coating technology. And with the use of special polymers, these DM materials bond and adhere to a wide variety of resin materials with relative ease2.
It is understood that higher performance resin materials—with the characteristics of higher Tg, lower CTE, and higher Td (temperature of decomposition)—are more chemically resistant, making desmear more difficult. With less resin removal and minimal restructuring of the resin surface after desmear, one can surmise that electroless copper would be less effective on these types of materials. The carbon- and graphite-based direct metallization systems do not require a palladium catalyst to first adsorb onto the glass and resin in order to catalyze the deposition of the copper. The electroless copper deposition process is shown below. The presence of palladium is required to effect the reaction as shown below. The process is essentially two half-cell reactions:
Overall Reaction: Cu(EDTA)2- + 2HCHO + 4OH- → Cu + H2 + H2O + 2CHOO- + EDTA4+
Sources of formate: secondary reducing agent
1. Cu(EDTA)2- + 2HCHO + 4OH- → Cu + H2 + H2O + 2CHOO- + EDTA4+
2. 2HCHO + OH- ↔ CH3OH + HCOO-
A byproduct of electroless copper plating is hydrogen gas (H2). The ability of these fine gas bubbles to lodge in blind vias and high aspect ratio through-holes is well understood. Even with the use of vibration and modified plating solution agitation systems, hydrogen gas remains an issue. However, the direct plating processes, as stated earlier, are coating processes, not chemical reactions. Thus, hydrogen gas evolution is not present.
There is a second byproduct of electroless copper—the Cannizzaro reaction. Here, the reducing agent in the electroless copper plating solution reacts with the caustic component of the solution to produce sodium formate. The sodium formate leads to an increase in specific gravity of the solution, which in turn can lead to solution instability and a slow deposition rate. Additional concerns with increases in specific gravity are plating defects such as hole wall pullaway (HWPA) and interconnect defects (ICD).
Another advantage of these DM systems is the relatively low cost to automate the plating line. As an example, a graphite-based or carbon black process with a horizontal plating tool is able to prepare and coat a board in five to six minutes. The panel is then ready for either panel plating in electrolytic copper or is sent to dry film imaging prior to pattern plating.
In next month’s column of Trouble in Your Tank, I will present a more in-depth discussion of direct metallization.
References
1. HDI Handbook, by Happy Holden.
2. “Comparing the Reliability of a Graphite-based Direct Metallization Process to Conventional Electroless Copper for Rigid Through-Hole Printed Circuit Boards,” by Michael Carano, Electronic Circuits World Convention 12, November 2011, Taipei, Taiwan.
This column originally appeared in the September 2023 issue of PCB007 Magazine.
More Columns from Trouble in Your Tank
Trouble in Your Tank: Metallizing Flexible Circuit Materials—Mitigating Deposit StressTrouble in Your Tank: Can You Drill the Perfect Hole?
Trouble in Your Tank: Yield Improvement and Reliability
Trouble in Your Tank: Causes of Plating Voids, Pre-electroless Copper
Trouble in Your Tank: Organic Addition Agents in Electrolytic Copper Plating
Trouble in Your Tank: Interconnect Defect—The Three Degrees of Separation
Trouble in Your Tank: Things You Can Do for Better Wet Process Control
Trouble in Your Tank: Processes to Support IC Substrates and Advanced Packaging, Part 5