Planning, DFM, and Inspection: Key to High-reliability Fab
October 30, 2023 | I-Connect007 Editorial TeamEstimated reading time: 2 minutes
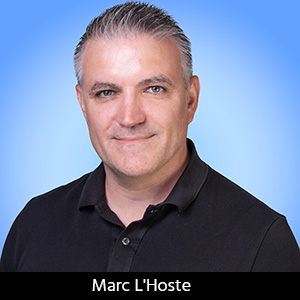
At PCB West, Andy Shaughnessy and Kelly Dack spoke with Marc L’Hoste, VP of West and South Americas for ICAPE Group, a company that supplies and manufactures high-tech PCBs at locations around the world.
We asked Marc to share some advice regarding high-reliability fab. In this conversation, Marc is clear that planning, pre-work, and inspection are the key ingredients to high-reliability success.
Kelly Dack: Marc, you fabricate quite a few high-reliability PCBs. How do you define high reliability and what is your perspective on what high reliability means in our industry?
Marc L’Hoste: IPC class 3 stands out for high-reliability printed circuit boards, but it also depends upon the type of industry and the type of customer. When we look at our own customers, about 20% of them are in the automotive industry, which has always been very complex to navigate. Automotive suppliers have very high standards to follow, such as the IATF ISO certification. For example, the quality levels are usually measured in parts per million (PPM) of manufactured parts. Over the past 15 years, we've been able to deliver fewer than 40 PPM for the automotive industry, which means less than 40 defective PCBs per million—significantly better than we see in standard consumer production where we are usually talking about 250 PPM. The same applies to other critical industries, such as aerospace, with certifications like AS9100, and critical processes with sampling and DPPM (defective parts per million) controls.
Dack: That’s a pretty low defect rate. What are some of the most typical causes of failures you see in high-reliability fabrication?
L’Hoste: A lot of different points need to be checked. For me, it always starts with the design itself, and making sure that whoever designs the board follows the IPC guidance. We have spreadsheets and guidance sheets that we can share with our customers. Let’s say Bob is tasked with selecting the right manufacturer for his boards. Bob must make sure that, if you build a flex or rigid-flex circuit board, you're not working with a factory that specializes only in rigid or metal PCBs. Selecting the right manufacturer usually means auditing them to make sure they have the right technical capabilities to build these boards. Choosing the right materials and finishes is also critical, and the finishes you select will depend upon the type of components on your boards. OSP (organic solderability preservative) is great, of course. It's very cost-effective, but if you have a BGA on your board, that might not necessarily be the right finish to choose.
Once you've nailed down all these different points, make sure that you do a good inspection on your board. A 100% test is always mandatory. Automatic visual inspection is very important, too. What we propose at ICAPE Group is a kind of double inspection. We have about 60 quality inspectors, and some of them are directly working with our engineering and manufacturing partners. Their job is to control the quality of our boards at these different locations. We have double points of inspection in the process: 100% inspection on our boards at the factory, and then inspection with our own quality people at our partners’ locations before we ship.
To read this entire conversation, which appeared in the October 2023 issue of PCB007 Magazine, click here.
Suggested Items
Indium Wins EM Asia Innovation Award
05/01/2025 | Indium CorporationIndium Corporation, a leading materials provider for the electronics assembly market, recently earned an Electronics Manufacturing (EM) Asia Innovation Award for its new high-reliability Durafuse® HR alloy for solder paste at Productronica China in Shanghai.
Fresh PCB Concepts: Key Considerations for Reliability, Performance, and Compliance in PCBs
05/01/2025 | Team NCAB -- Column: Fresh PCB ConceptsAs a field application engineer with many years of experience, I’ve conducted thousands of designs for manufacturing (DFM) analyses on printed circuit boards (PCBs). From basic one-layer boards to complex high density interconnect (HDI) designs, I’ve provided technical advice across a wide spectrum of technologies.
Rising Star Award: Paavo Niskala, TactoTek
04/28/2025 | Nolan Johnson, I-Connect007Paavo Niskala joined the IPC community in 2022 as part of the inaugural steering group for in-mold electronics. He led the development of standard IPC-8401, Guidelines for In-Mold Electronics, chairing the project from its inception to its publication in 2024. Currently, Paavo serves as vice chair of the D-84A Plastronics Accelerated Reliability Testing Task Group, contributing his expertise to advancing reliability standards in the field.
INEMI Call-for-Participation Webinar: BiSn-Based Low-Temperature Soldering Process and Reliability Project Phase 3b
04/28/2025 | iNEMIIn 2015, INEMI initiated the BiSn-Based Low-Temperature Soldering Process and Reliability Project to assess the feasibility of using low-temperature solders (LTS) in the SnBi system to address various technological, economic and ecological drivers for assembly of consumer computer electronic board products.
Microchip Completes Radiation-Hardened Power MOSFET Family to MIL-PRF-19500/746 and Achieves JANSF 300 Krad Capability
04/22/2025 | MicrochipThe JANS qualification represents the highest level of screening and acceptance requirements, ensuring the superior performance, quality and reliability of discrete semiconductors for aerospace, defense and spaceflight applications.