-
- News
- Books
Featured Books
- pcb007 Magazine
Latest Issues
Current IssueInventing the Future with SEL
Two years after launching its state-of-the-art PCB facility, SEL shares lessons in vision, execution, and innovation, plus insights from industry icons and technology leaders shaping the future of PCB fabrication.
Sales: From Pitch to PO
From the first cold call to finally receiving that first purchase order, the July PCB007 Magazine breaks down some critical parts of the sales stack. To up your sales game, read on!
The Hole Truth: Via Integrity in an HDI World
From the drilled hole to registration across multiple sequential lamination cycles, to the quality of your copper plating, via reliability in an HDI world is becoming an ever-greater challenge. This month we look at “The Hole Truth,” from creating the “perfect” via to how you can assure via quality and reliability, the first time, every time.
- Articles
- Columns
- Links
- Media kit
||| MENU - pcb007 Magazine
Planning, DFM, and Inspection: Key to High-reliability Fab
October 30, 2023 | I-Connect007 Editorial TeamEstimated reading time: 2 minutes
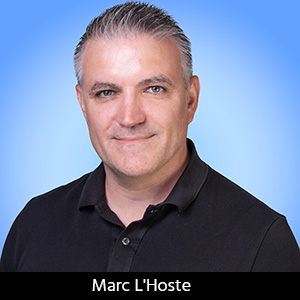
At PCB West, Andy Shaughnessy and Kelly Dack spoke with Marc L’Hoste, VP of West and South Americas for ICAPE Group, a company that supplies and manufactures high-tech PCBs at locations around the world.
We asked Marc to share some advice regarding high-reliability fab. In this conversation, Marc is clear that planning, pre-work, and inspection are the key ingredients to high-reliability success.
Kelly Dack: Marc, you fabricate quite a few high-reliability PCBs. How do you define high reliability and what is your perspective on what high reliability means in our industry?
Marc L’Hoste: IPC class 3 stands out for high-reliability printed circuit boards, but it also depends upon the type of industry and the type of customer. When we look at our own customers, about 20% of them are in the automotive industry, which has always been very complex to navigate. Automotive suppliers have very high standards to follow, such as the IATF ISO certification. For example, the quality levels are usually measured in parts per million (PPM) of manufactured parts. Over the past 15 years, we've been able to deliver fewer than 40 PPM for the automotive industry, which means less than 40 defective PCBs per million—significantly better than we see in standard consumer production where we are usually talking about 250 PPM. The same applies to other critical industries, such as aerospace, with certifications like AS9100, and critical processes with sampling and DPPM (defective parts per million) controls.
Dack: That’s a pretty low defect rate. What are some of the most typical causes of failures you see in high-reliability fabrication?
L’Hoste: A lot of different points need to be checked. For me, it always starts with the design itself, and making sure that whoever designs the board follows the IPC guidance. We have spreadsheets and guidance sheets that we can share with our customers. Let’s say Bob is tasked with selecting the right manufacturer for his boards. Bob must make sure that, if you build a flex or rigid-flex circuit board, you're not working with a factory that specializes only in rigid or metal PCBs. Selecting the right manufacturer usually means auditing them to make sure they have the right technical capabilities to build these boards. Choosing the right materials and finishes is also critical, and the finishes you select will depend upon the type of components on your boards. OSP (organic solderability preservative) is great, of course. It's very cost-effective, but if you have a BGA on your board, that might not necessarily be the right finish to choose.
Once you've nailed down all these different points, make sure that you do a good inspection on your board. A 100% test is always mandatory. Automatic visual inspection is very important, too. What we propose at ICAPE Group is a kind of double inspection. We have about 60 quality inspectors, and some of them are directly working with our engineering and manufacturing partners. Their job is to control the quality of our boards at these different locations. We have double points of inspection in the process: 100% inspection on our boards at the factory, and then inspection with our own quality people at our partners’ locations before we ship.
To read this entire conversation, which appeared in the October 2023 issue of PCB007 Magazine, click here.
Testimonial
"The I-Connect007 team is outstanding—kind, responsive, and a true marketing partner. Their design team created fresh, eye-catching ads, and their editorial support polished our content to let our brand shine. Thank you all! "
Sweeney Ng - CEE PCBSuggested Items
Advint and SanRex Expand High-Performance DC Rectifier Access for North American PCB Fabricators
08/12/2025 | Advint IncorporatedAdvint Incorporated has entered a strategic partnership with SanRex Corporation, enhancing access to industrial-grade DC rectifiers for the US printed circuit board industry. With a legacy of power innovation and performance across the globe, SanRex rectifiers are available through Advint’s proficient distribution network.
ZESTRON to Exhibit at Upcoming SMTA Guadalajara Expo
08/07/2025 | ZESTRONZESTRON, a global leader in high-precision cleaning solutions and services, is excited to announce its participation in the 2025 SMTA Guadalajara Expo & Tech Forum.
Magnalytix’s Dr. Mike Bixenman to Guide PDC at SMTA High-Reliability Cleaning and Conformal Coating Conference
07/31/2025 | MAGNALYTIXMagnalytix, providing real-time reliability solutions for electronics manufacturing, is excited to announce that Dr. Mike Bixenman will present the professional development course “The Effects of Flux Residues and Process Contamination on the Reliability of the Electronic Assembly” on Wednesday, Aug. 13 at 9:00 AM CST to open the second day of the STMA High-Reliability Cleaning and Conformal Coating Conference.
Federal Electronics Mexico Enhances SMT Line with Installation of Heller Industries Reflow Oven
08/01/2025 | Federal ElectronicsFederal Electronics, a leader in providing advanced electronic manufacturing services, has enhanced its surface mount technology (SMT) operations with the installation of a new Heller Industries reflow oven at its facility in Hermosillo. This upgrade supports the company’s continued growth in high-reliability markets such as aerospace, medical, industrial, and instrumentation.
KYZEN Cleaning Experts to Provide Insights at SMTA High Reliability Cleaning and Coating Conference
07/29/2025 | KYZEN'KYZEN, the global leader in innovative environmentally responsible cleaning chemistries, announced today that three members of the KYZEN team of cleaning experts will present technical presentations as part of KYZEN’s participation at the 2025 SMTA High Reliability Cleaning and Conformal Coating Conference scheduled to take place Aug. 12-14, 2025 at the Westin DFW Airport.