8 Simple Rules for Streamlining Your Design
November 30, 2023 | Chris Young, Young Engineering ServicesEstimated reading time: 5 minutes
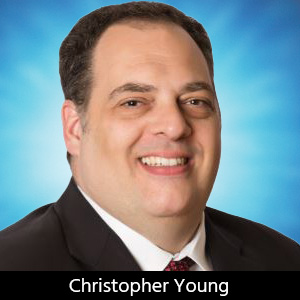
There are many ways, dozens to be sure, and most likely many more, to streamline a PCB design. My goal here is to pick a single-digit number of rules to abide by, that can be reasonably adhered to, and provide some bang for the buck. These rules are meant to reduce design scope creep, avoid PCB respins, and improve production yields.
1: Communicate clearly.
Use explicit communication when addressing ambiguous items. Test point placement can seem like an ambiguous task. Statements like, “Find room for test points,” do not help to define scope or draw boundaries. Instead, try statements like, “Production test points can only be on a single side of the PCB in order to reduce test fixture complexity.” Implicit communication should be reserved for well-defined objectives and processes. An example would be instructing a PCB designer to place test points per the design procedures identified by company policy X, paragraph Y.
2: Proceed with a common goal in mind.
Designing on the fly without a mutually agreed upon set of goals is a catalyst for scope creep and technical debt. A design blitz, as in football, is a defensive high-risk maneuver intended to reduce schedule (offensive) pressure. Instead, take the time needed to establish a well-defined and measurable set of design goals. Include the project stakeholders, get buy in, and then execute.
3: Design your PCB power delivery system (PDS).
Your PCB power delivery system (power planes/structures) should be based on your power distribution requirements and not a coincidence of layout. This means that your PDS design should take place before settling on a board stackup. A typical PDS is composed of discrete capacitors, power plane capacitance, and on-chip capacitance. Determining the amount of plane capacitance needed for a specific design should involve the use of a simulator such as HyperLynx, ADS, or HFSS. Designing an appropriate PDS for your board design is easy to say, much harder to do, and very much worth your time. Improper or poorly implemented PDS designs are nearly impossible to recover from without a costly board respin.
4: Know your drill holes.
A PCB can play host to many types of drill holes for various reasons. A few examples are vias, mounting holes, tooling holes, and press fit holes. Vias come in many forms, but they tend to be some type of plated hole that is typically used for signal, ground, or power transitions from one PCB layer to another. Vias can also be used for thermal conduction between PCB layers. It is important to understand that mechanical engineers typically regard mounting and tooling holes as two very different types of holes that serve entirely different purposes. Mounting holes can be plated or non-plated and provide a clearance/loose fit for the PCB so that it may be attached to some other structure. Tooling holes are designed and manufactured to a tight tolerance so they can provide a transition fit needed for precise alignment of a PCB in an assembly or test fixture. PCBs use interference fit holes for press fit connectors. The connector/PCB mating pins interfere slightly with the holes on the PCB, requiring force to be applied to the connector during the mating process instead of soldering the pins to the PCB itself. Knowing the types of drill holes used on your PCB and their purposes allows designers to effectively communicate their purposes to other stakeholders in a project.
5: Coordinate your design with your fabricator.
The last thing you want to hear from a PCB fabricator is that they are no-bidding your design because it is not compatible with their capabilities. It is perfectly reasonable to include your PCB fabricator in your design reviews. Making sure that your design fits within the manufacturing capabilities of your fabricator is a primary objective, not an “on the side” project. Furthermore, your PCBs built for production should be well within fabricator’s range of capabilities and should not be pushing their edges so that your yields (major PCB cost driver) are not driven by process variations.
6: Consult with the group or company assembling your boards.
It is best to know what practical limitations your assembly process imposes on your design instead of finding out post assembly. Not all pick-and-place machines are created equal. Accuracy of small component placement can vary greatly between different pick-and-place machines. Manually removing assembled boards from panels can damage shock-sensitive components. The risks associated with whoever may be assembling your boards can be mitigated by simply involving them in your design review process.
7: Document your component library process.
A well-documented CAD library process reduces the chances of errors when creating parts. Part requests should include the part number, manufacturer, part description, datasheet(s), priority level, need date, package type, part type, and any descriptive information or notes for symbol or footprint creation. The part that is created to fulfill the request should be documented and linked to the request. The part should then be reviewed and documented as either meeting the request or as needing to be reworked. The documentation could take the form of a spreadsheet, database, or even a physical paper trail. The intent is to explicitly communicate what parts need to be created and how.
8: Test point placement is critical.
PCB test points serve to support design and production. Circuit designers will use test points to assist in integration and verify functionality. Test points are typically used in production to load software/firmware and verify proper PCB assembly. Production using test points should take precedence over design and engineering test points. Test point locations directly impact the complexity of test fixture design, so strive to place them on only one side of the PCB. Do not place components on the opposite side of a PCB underneath a test point. This provides space on the PCB to apply an opposing force to reduce stress and strain on the board assembly when test points are engaged during test. Don’t find space for test points. Make space by performing test point placement alongside component placement.
Resources
- “Power Delivery System Design,” by Lee Ritchey, Altium.
- Simulators – Keysight ADS, Siemens EDA HyperLynx, Ansys HFSS.
- Chris Young is founder and president of Young Engineering Services.
This article originally appears in the November 2023 issue of Design007 Magazine.
Suggested Items
Trump Copper Tariffs Spark Concern
07/10/2025 | I-Connect007 Editorial TeamPresident Donald Trump stated on July 8 that he plans to impose a 50% tariff on copper imports, sparking concern in a global industry whose output is critical to electric vehicles, military hardware, semiconductors, and a wide range of consumer goods. According to Yahoo Finance, copper futures climbed over 2% following tariff confirmation.
Flexible Printed Circuit Board Market to Reach US$40.447 Billion by 2030
07/10/2025 | Globe NewswireThe flexible printed circuit board market will grow at a CAGR of 8.28% to be valued at US$40.447 billion in 2030 from US$27.17 billion in 2025.
TTM Technologies Prepares For the Future with the Acquisition of a Facility in Wisconsin and Land in Penang
07/10/2025 | Globe NewswireTTM Technologies, Inc., a leading global manufacturer of technology solutions including mission systems, radio frequency (RF) components and RF microwave/microelectronic assemblies, quick-turn and technologically advanced printed circuit boards (PCB), announced the acquisition of a 750,000-square-foot facility in Eau Claire, Wisconsin, as well as land rights for an additional future manufacturing site in Penang, Malaysia.
Schweizer Electronic: Annual General Meeting Approves All Proposed Resolutions with a Large Majority
07/10/2025 | Schweizer Electronic AGThe Annual General Meeting of Schweizer Electronic AG took place on June 27, 2025, at the company's headquarters in Schramberg.
Taiwan PCB Industry Adopts Cautious CapEx Strategy, Eyes AI and Southeast Asia for Growth
07/10/2025 | TPCADriven by the stabilization of the global electronics market and the strong demand for AI applications, although the Taiwan printed circuit (PCB) industry is facing a trend of capital expenditure convergence for three consecutive years, its output value and operating performance continue to rise, indicating that the industry is shifting from high investment to high added value development, and the industrial structure is undergoing a steady transformation.