-
- News
- Books
Featured Books
- pcb007 Magazine
Latest Issues
Current IssueInventing the Future with SEL
Two years after launching its state-of-the-art PCB facility, SEL shares lessons in vision, execution, and innovation, plus insights from industry icons and technology leaders shaping the future of PCB fabrication.
Sales: From Pitch to PO
From the first cold call to finally receiving that first purchase order, the July PCB007 Magazine breaks down some critical parts of the sales stack. To up your sales game, read on!
The Hole Truth: Via Integrity in an HDI World
From the drilled hole to registration across multiple sequential lamination cycles, to the quality of your copper plating, via reliability in an HDI world is becoming an ever-greater challenge. This month we look at “The Hole Truth,” from creating the “perfect” via to how you can assure via quality and reliability, the first time, every time.
- Articles
- Columns
- Links
- Media kit
||| MENU - pcb007 Magazine
Amitron's Leap Into the AI Frontier
December 12, 2023 | Nolan Johnson, PCB007Estimated reading time: 2 minutes
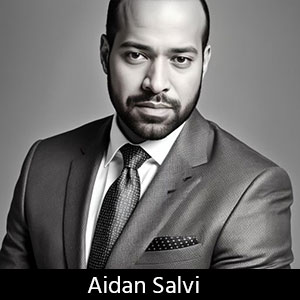
In a conversation with Aidan Salvi, Amitron’s chief transformation officer, he spoke of the interaction of machine learning on registration. Amitron has been modernizing much of its manufacturing equipment, and Aidan points out that improving registration is a key objective. He sees registration as a holistic system. To make smart improvements, you need data. To get data, you need equipment and sensors which capture the data. To make sense of the data, you need analysis and, eventually, predictive tools.
Nolan Johnson: Aidan, you’re leading a transformation at Amitron, and you’ve shared that registration improvement is one of the objectives of your modernization. Where do you see machine learning and AI contributing?
Aidan Salvi: There are steps to making AI impactful. It all starts with gathering the data. We operate our process with nearly 60 different pieces of equipment that do different functions. When looking at what the future of AI could be, the biggest challenge is how we consolidate that data. How do we create standards? How do we create scalable hardware that can store and retrieve the data? This is a tremendous amount of data; companies need to look at their data infrastructure and assess how to integrate and pull it all together. That is the first hurdle I see for AI in the future.
Johnson: When it comes to bringing AI into the PCB factory, is this a hardware processing horsepower and data storage challenge, or maybe one with software tools or people and skills? Where do you start using machine learning and AI appropriately for registration?
Salvi: There are at least three things I see as the cornerstones of this challenge. First, it's integration with the equipment. You must deal with quite a few manufacturers to extract the necessary data out of the equipment in a consistent way, and that doesn't exist in our industry as well as it could. Second, it's not necessarily computing horsepower, but more of an infrastructure design issue. We're dealing with quite a bit of real-time data that needs to be transported over networks, stored, and processed. In other words, it’s designing infrastructure that can handle the future needs of AI computing. The last piece is cloud integration, where much of AI is built. That starts moving us away from the physical component, and into looking at how we can start processing the data at scale and building data systems in a virtual cloud architecture. These are challenging things to put in place because of the overall cost and knowledge gaps that exist.
To read this entire conversation, which appeared in the November 2023 issue of PCB007 Magazine, click here.
Testimonial
"In a year when every marketing dollar mattered, I chose to keep I-Connect007 in our 2025 plan. Their commitment to high-quality, insightful content aligns with Koh Young’s values and helps readers navigate a changing industry. "
Brent Fischthal - Koh YoungSuggested Items
Macronix Introduces Cutting-Edge Secure-Boot NOR Flash Memory
08/08/2025 | PRNewswireMacronix International Co., Ltd., a leading integrated device manufacturer in the non-volatile memory (NVM) market, announced ArmorBoot MX76, a robust NOR flash memory combining in a single device, the essential performance and an array of security features that deliver rapid boot times and iron-clad data protection.
Inside the AI Hardware Boom: Servers, Substrates and Advanced Packaging
08/07/2025 | Edy Yu, Printed Circuit Information, China, and Marcy LaRont, I-Connect007AI is rewriting the hardware playbook, marrying complex software and algorithms to run and improve machine and equipment operations. Sorting through, managing, and utilizing massive amounts of data takes tremendous data storage and processing power. Enter the new generation of supercomputers and data servers. The data servers being built today are not your momma’s server, as they say.
AI Is the Golden Track Reviving Electronics and PCBs
08/06/2025 | Edy Yu, Chief Editor, ECIO, and the I-Connect007 Editorial TeamRemember 2021? Despite COVID, the electronics industry hit a high. Then came the slide. By 2023, the industry was deep in the red. With inflation, policy shifts, and exchange rate shocks, the problems were long, and the outlook was bleak. Recovery finally appeared in 2024, but it was fragile. Automotive electronics slumped, wireless demand stayed soft, and the ride up was anything but smooth. Yet, amid the uncertainty, one bright track emerged: artificial intelligence (AI).
Brent Laufenberg Appointed CIO of the Global Electronics Association, Advancing Technology and Member Services
07/31/2025 | Global Electronics AssociationThe Global Electronics Association (formerly IPC International Inc.) announces the appointment of Brent Laufenberg as its new Chief Information Officer (CIO).
SES AI Accelerates Timeline for Revenue Growth and Profitability with Acquisition of UZ Energy
07/31/2025 | BUSINESS WIRESES AI Corporation, a global leader in the development and manufacturing of AI-enhanced high-performance Li-Metal and Li-ion batteries, today announced it has executed a definitive agreement to acquire 100% of UZ Energy, an energy storage systems (“ESS”) provider, for a purchase price of approximately $25.5 million, subject to earnout adjustment based on the achievement of specified financial targets.