-
- News
- Books
Featured Books
- pcb007 Magazine
Latest Issues
Current IssueInventing the Future with SEL
Two years after launching its state-of-the-art PCB facility, SEL shares lessons in vision, execution, and innovation, plus insights from industry icons and technology leaders shaping the future of PCB fabrication.
Sales: From Pitch to PO
From the first cold call to finally receiving that first purchase order, the July PCB007 Magazine breaks down some critical parts of the sales stack. To up your sales game, read on!
The Hole Truth: Via Integrity in an HDI World
From the drilled hole to registration across multiple sequential lamination cycles, to the quality of your copper plating, via reliability in an HDI world is becoming an ever-greater challenge. This month we look at “The Hole Truth,” from creating the “perfect” via to how you can assure via quality and reliability, the first time, every time.
- Articles
- Columns
- Links
- Media kit
||| MENU - pcb007 Magazine
Estimated reading time: 7 minutes
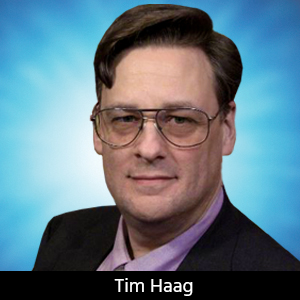
Tim’s Takeaways: PCB Design and Manufacturing—Let’s Work Together
Twas the night before deadline, when all through the house,
Not a creature was stirring, not even an optical mouse;
The components were all placed on the board with care,
In hopes the design review would be gentle and fair.
The traces were routed, with not a single net left,
While power and ground were connected, all expectations were met.
The designers were tired, and ready for a rest,
But hold on everyone, the manufacturer was next in line to test.
Yes, that was embarrassingly cheesy, but I penned this prose to highlight how PCB design and manufacturing has traditionally been treated as two different disciplines when, in reality, we should all be working together.
Let’s Work Together
Circuit board design combines electrical, mechanical, and manufacturing engineering. There are many other engineering disciplines involved, such as component and reliability engineering, but the first three are the ones the PCB layout designer will usually spend the most time with. Although electrical and mechanical teams can and usually do have their own dramatic conflicts with each other, they usually end up working everything out in the end.
Manufacturing engineering can be a very different story, especially when those requirements come from an outside vendor. Design teams often are more concerned about whether their design is functioning as intended, as opposed to how it gets built. On the other hand, the manufacturer can be more focused on building the design rather than on how it will function once it is built. For the PCB layout engineer, it is essential to realize that neither should be labeled as “the bad guys.” Instead, they both have important needs that must be met.
I have spoken with many different companies, and have found that adherence to manufacturing requirements in PCB layout varies quite a bit. On one side are those design groups that don’t exercise a lot of caution when it comes to manufacturing requirements. These are often designs produced in lower numbers, and error-free yields aren’t their primary concern. The boards are manufactured knowing they will require a lot of manual clean-up to get working units finished.
On the flip side are those companies whose designs are produced in high numbers, and error-free manufacturing is critical to cutting costs. The manufacturing requirements are usually very detailed and process automation is essential to reduce overhead and increase yields. As you would expect, some companies fall between these two extremes. Many of these companies will use different levels of manufacturing requirements depending on the needs of the project, such as prototype vs. regular production builds.
But whether your design team is building prototypes or high-production runs, your success lies in understanding how to work with your manufacturer.
DFM: A Bridge Between Design and Manufacturing
The key to designing circuit boards that can be successfully manufactured with minimal errors is to follow design for manufacturing (DFM) rules. We are all familiar with our CAD system’s suite of DFM checking routines, but design for manufacturability is more than just checking off a standard list of rules. It means working with your manufacturer to find out what they need before you hand them the design files. This includes board layer stackup and materials, part selection, and the correct location and spacing of components, traces, and other PCB elements. For the DFM process to truly succeed, consider these three points before you go to layout.
1. Document It
Documenting your company’s DFM process so that everyone has a clear understanding of what the objectives are is essential to the long-term success of design for manufacturability. There can be a big difference between how design groups document their standards and procedures, and those with established DFM practices are typically at the top of the list. DFM and other standard operating procedures are usually carefully documented and available to employees electronically or in printed format. In some instances, the design is gated to DFM documentation and won’t be released until official reviews are completed and signed off by specific stakeholders. Then there are those groups with very little in the way of official documentation. If they follow DFM practices at all, it is usually in the form of “tribal knowledge” based on previous manufacturing experiences. Do yourself a favor and document your DFM processes and requirements.
2. Enforce It
The next step is to ensure that our DFM is fully documented and ready to be used. This is a great idea, but how can we do it? Here are some ideas to try:
- If you are working at a company where the DFM processes are not well documented, you can start by getting some of these processes recorded. “Is that really my job,” you might ask. Well, if you are laying out circuit boards, then the answer is a resounding yes.
- A good place to start is by working with your manufacturing vendors. Contrary to how they are sometimes viewed, they are not the enemy; in fact, they are highly vested in wanting you to be successful. After all, if you are successful, they will be too, and the way they will make you successful is by building your circuit boards correctly, on time, and without errors. Therefore, spend some time with them and find out how you can help them so they can better help you.
- Start capturing some of these standards and get them documented. Even if all you do is create some simple bullet points, it’s a good place to begin. You don’t have to start out by trying to write a novel; just get the basics down in one place. Once you gather some of these ideas, you will probably find that they will start flowing into what will eventually become a good working document.
Once your documentation starts to build up, make sure that it is published for all to see and incorporate its use in your job requirements. It is important that designers see quality as an important part of their overall job performance.
3. Automate It
Now that you’ve started the process of creating your DFM documentation and are enforcing its use by the design team, the next step is to automate. Look for ways to incorporate automated DFM checking into the design process, because there is a big difference out there in how this is being done. Some design teams don’t have any DFM checking processes in place and rely solely on their manufacturer to find, report, and even fix DFM errors. Others will perform only a visual check of their designs, while others have built in a very sophisticated automated checking process. Traditionally, automated DFM checking has been handled by the manufacturing vendors with their results reported back to the original designers. Any problems that are found require design changes, and sometimes the board layout has to be completely redone to resolve any bugs found by the manufacturer. Since these same types of DFM checking tools used by manufacturers are available to design teams, engineering teams should put them to work.
There are a lot of applications that will incorporate DFM checking into the design process, and it may even be that the tools you’re using have some new and enhanced features built in that can help. Believe me, full DFM checking by the engineering team before the design goes to manufacturing will save you a lot of time and effort later. But there’s still one important step that can potentially save your design team a lot of time and effort: Communication.
How Can We Make It All Work?
One of the best things we can do to help the relationship between design teams and our manufacturing partners is to improve communications. Too often this relationship has been looked at as one of merely throwing the design “over the wall.” That may have worked in the past, but it’s very outdated considering the amount of information that needs to be exchanged between engineering and manufacturing for a design. Throwing things over the wall is just as likely to end up hitting you squarely in the head and knocking you flat. I know it’s tempting to want to dump the completed design in someone else’s hands and move on to the next exciting project, but that doesn’t work anymore. Our goal as designers should be to see the project through all the way from inception to completion, and that means partnering with our manufacturing vendors to accomplish this task together.
One way to strengthen communication is to encourage participation between designers and manufacturers. Many vendors will happily schedule an onsite visit so you can see exactly what happens during the production of your circuit board. Manufacturers also put a high value on pre-design meetings, design reviews, and in-process questions and check-ins. So, do yourself a favor and spend some time with the people who will build what you design. In the long run it can only help you to design a better product and grow in your career. Until next time, everyone, keep on designing.
This column originally appeared in the January 2024 issue of Design007 Magazine.
More Columns from Tim's Takeaways
Tim’s Takeaways: One for the ArchivesTim’s Takeaways: The Art of Technical Instruction
Tim’s Takeaways: Take It From Scotty, Simple Really is Better
Tim’s Takeaways: Human Ingenuity and the Rigid-flex PCB
Tim’s Takeaways: How I Learned Advanced Design Strategies
Tim’s Takeaways: Batter Up—Stepping Up to the Substrate
Tim’s Takeaways: Tribal Knowledge—Not the Villain You Thought
Tim’s Takeaways: Threading the Needle Through Advanced Packaging