-
-
News
News Highlights
- Books
Featured Books
- pcb007 Magazine
Latest Issues
Current IssueThe Hole Truth: Via Integrity in an HDI World
From the drilled hole to registration across multiple sequential lamination cycles, to the quality of your copper plating, via reliability in an HDI world is becoming an ever-greater challenge. This month we look at “The Hole Truth,” from creating the “perfect” via to how you can assure via quality and reliability, the first time, every time.
In Pursuit of Perfection: Defect Reduction
For bare PCB board fabrication, defect reduction is a critical aspect of a company's bottom line profitability. In this issue, we examine how imaging, etching, and plating processes can provide information and insight into reducing defects and increasing yields.
Voices of the Industry
We take the pulse of the PCB industry by sharing insights from leading fabricators and suppliers in this month's issue. We've gathered their thoughts on the new U.S. administration, spending, the war in Ukraine, and their most pressing needs. It’s an eye-opening and enlightening look behind the curtain.
- Articles
- Columns
- Links
- Media kit
||| MENU - pcb007 Magazine
Traditional Materials, High-Frequency Boards?
June 18, 2024 | I-Connect007 Editorial TeamEstimated reading time: 2 minutes
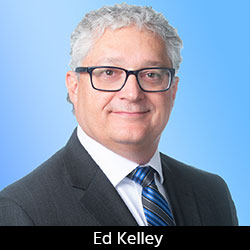
Not long ago, high-frequency and RF boards required specialized laminates, which tend to be costly and difficult to manufacture. But now, high-frequency designers use traditional PCB laminates for certain high-frequency boards. How is this possible?
For some insight, we asked Ed Kelley, founder of Four Peaks Innovation and former CTO of Isola, to discuss how traditional materials have improved and what this means to PCB designers and design engineers today.
Andy Shaughnessy: Kris Moyer at IPC is teaching designers how to avoid overconstraining their board materials. There are ways to build high-frequency boards, even RF boards, without using high-frequency materials. What are your thoughts?
Ed Kelley: If we look back in history, there was a great divide between FR-4 materials and what people used for RF/microwave applications, which really boiled down to Dk and Df properties. If you look back at the loss range, or dissipation factors, and the typical types of polymers that were used in those applications, FR-4s back then would fit into the high-loss and standard-loss categories of today’s material sets. Even back then, the products used in RF applications were in today's ultra- or extremely low-loss categories.
The two markets were separate and there wasn't a lot in the middle. But as digital applications began to require more speed and higher frequencies, those of us involved in developing materials decades ago began to introduce lower Dk, lower-loss materials, with GETEK being one of the first. Material manufacturers created competing products and these other categories—mid-loss and low-loss material segments. We began using different resin chemistries to get to the electrical performance requirements in these materials. When you get down into the very-low, ultra-low, and extremely low-loss categories, the laminate suppliers are beginning to use resins that look more like what had always been used in RF microwave materials.
There were also other differences with RF microwave materials. Historically, they used a lot of fillers that were designed to maintain Dk stability over temperature, humidity, and frequency. One of the participants in that market had patents that limited others from developing similar products. Most of those patents have now expired.
Marcy LaRont: Because of these different polymers, adhesives, and blends, we can now potentially consider “FR-4” material as another option to traditional RF material.
Kelley: Yes, historically FR-4 was virtually all epoxy resins. But you just can't get to the Dk requirements for high-speed digital applications using only epoxy. So, the first step was blending them with other resins, be it PPO, BT, SMA, etc. Eventually, you get to the lowest-loss materials used today in high-speed digital, which usually use a resin called polyphenylene ether (PPE), and blends of PPE and other resins. Over the years, conventional copper-clad laminate (CCL) suppliers, particularly when lead-free assembly came on the scene, began to use a lot of inorganic fillers to control CTE properties. So, you've had this convergence. The RF guys almost always used fillers. Then, the conventional CCL suppliers became familiar with incorporating inorganic fillers into these other resin systems. Even the manufacturing processes look similar, with the exception of PTFE-type RF materials.
To read this entire conversation, which appeared in the May 2024 issue of Design007 Magazine, click here.
Suggested Items
Imec Unveils Record-Low Loss 300mm RF Silicon Interposer for Sub-THz Systems
05/27/2025 | ImecAt the IEEE ECTC 2025 conference, imec – a world-leading research and innovation hub in nanoelectronics and digital technologies – highlights the exceptional performance and flexibility of its 300mm RF silicon interposer platform.
indie Semiconductor Reports Q1 2025 Results
05/13/2025 | BUSINESS WIREindie Semiconductor, Inc., an automotive solutions innovator, today announced first quarter results for the period ended March 31, 2025. Q1 revenue was up 3.3 percent year-over-year to $54.1 million with Non-GAAP gross margin of 49.5 percent. On a GAAP basis, first quarter 2025 operating loss was $38.9 million compared to $49.6 million a year ago.
Keytronic Announces Results for Q3 of Fiscal Year 2025
05/12/2025 | KeytronicKey Tronic Corporation, a provider of electronic manufacturing services (EMS), announced its results for the quarter ended March 29, 2025.
Spirit AeroSystems Reports First Quarter 2025 Results
05/02/2025 | Spirit AeroSystems, Inc.Spirit's revenue in the first quarter of 2025 decreased from the same period of 2024, primarily due to lower production activity on most Boeing programs, particularly the Boeing 737 program.
Elementary Mr. Watson: Navigating RF—A Glide Path Approach to Design Success
04/24/2025 | John Watson -- Column: Elementary, Mr. WatsonOn a flight, I can always tell when we begin our descent because that subtle drop in my stomach tells me the altitude has changed. Landing an airplane involves a gradual, precise process called the glide path. It descends at the correct speed and 3-degree angle to touch down smoothly and safely on the runway without bouncing or coming to a sudden stop. Pilots use specialized tools like the Instrument Landing System (ILS) or GPS to stay on the correct path. Lights on the ground, called PAPI lights, help pilots know if they are too high or too low.