Forty Years of Innovation at Electra Polymer
June 26, 2024 | Marcy LaRont, PCB007 MagazineEstimated reading time: 5 minutes
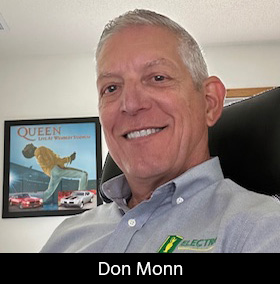
In this engaging interview, Don Monn, national sales manager at Electra Polymers, talks about the company's 40th anniversary and recent developments in inkjet solder mask technology. Don shares insights on the company’s history, commitment to innovation, and the environmental benefits of its products. He discusses the challenges and advancements in the circuit board industry since the 1990s, emphasizing the importance of education and mentorship. The conversation highlights Electra's strategic investments and their confidence in future growth.
Marcy LaRont: Don, Electra Polymers is celebrating 40 years. What is the company’s history?
Don Monn: Electra Polymers started 40 years ago in England as a privately held company. It was formed by someone who wanted to grow our industry with his commitment to solder masks, resists, and other similar products.. Electra has now been in the U.S. for 35 years and grown steadily over that time. We are not the largest supplier in the world, but we believe we offer distinct advantages, especially moving into the newer technologies.
LaRont: You are a pioneer in original direct imaging technology. Let’s talk about solder mask.
Monn: Solder mask, as a whole, is my life. Even when I was building circuit boards in a shop, I ran the screening department. It's really all I've done. I'm proud to admit I've been deeply involved in the promotion of new technologies since before 1990 when the world went from thermal cure solder masks to liquid photo imageable solder masks. I was one of the guys hired by the vendors to teach the technology, application, and process. I convinced OEMs it was good for them and convinced circuit board manufacturers it was a good investment. I taught people the advantages of technology and why it's good for them and the environment.
It is very much the same situation with inkjet solder masks. They're good for the environment, manufacturers, and OEMs. They solve many of the issues with solder masks that circuit board manufacturers are currently experiencing, as well as some of the issues that OEMs and users experience every day—and they're amazing.
I know people don't like change. In the 1990s, folks were hesitant about putting liquid photo-imageable solder masks in because they would have to buy more artwork. Today, there's a lot of hesitancy around adopting inkjet because the customer will have to buy new equipment. It may simply be that it's different, or they believe their OEM won't accept it. But what I want people to understand is that when I'm promoting inkjet solder masks to the PCB manufacturers, I am also promoting them to the end users and educating them on why it's good for their business. We are working on both ends of this to everyone’s ultimate advantage.
LaRont: For the PCB fabricator, it has been a continuous struggle to get an audience with OEMs and end users earlier when it can really make a difference. Why is it important to approach it on all fronts.
Monn: It’s important because it saves production time and time to market. It helps all of us when the OEMs know this technology is coming in advance.
LaRont: Looking back to when LPI was first introduced, what changes and developments have you seen since then?
Monn: In 1990, in the U.S. alone, there were many circuit board shops and a lot of square feet being produced. We didn't even know what a .003" dam was, and nobody talked about .008" drilled holes. Today, you don't walk across the street without having to deal with .003" solder mask dams and .008" drilled holes. It’s commonplace. Circuit boards are getting smaller with more layers. To build this, you must upgrade your technology.
LaRont: Investment is a hot topic right now, especially in the U.S. Is Electra Polymers investing in future growth or executing slower growth as you see demand increase?
Monn: At Electra Polymers, we are so committed to inkjet solder mask, but instead of waiting for everyone to catch on and start buying it, we are building up our capacity. We already have a building and we’re installing lines to make not 100 or 200 hundred kilos a week but thousands of kilos. We've already got the business to support a large percentage of what we're installing.
LaRont: So, it's not “build it and they will come.” You're building it because you know it's coming.
Monn: Our confidence level is high. Our product is just different enough. Our success rate has been undeniable. The people I work with every day are amazing, and I get to witness their experience and level of commitment, not only to the chemistry but to the process as a whole.
LaRont: Many industry folks will take comfort in your high level of confidence. I admire your passion after all these years.
Monn: Marcy, when I came out of the circuit board shop, a man named Gary Amo became my mentor. He took me out of a circuit board shop and taught me how to build relationships. He saw something in me that other people didn't always see. Gary convinced the executives they needed someone who could go into these PCB shops, set up our product on the production line, and run it for our customers. He said, “This kid can do it, so why don't we take advantage of that?” It changed my life.
LaRont: Working in a PCB shop was my first big job coming out of college too. I am so grateful for that time and those companies, as I met some of the best and smartest people I've ever worked with and had some great mentors. Do you have any closing thoughts?
Monn: I would like to close by inviting people to reach out to me personally if they want to talk about this technology and become more educated. If you're an OEM and you're not sure what this is, call me, and I'll explain what’s good about this for you. It’s not always about selling. I love to teach. Like I said, inkjet solder mask is my life.
LaRont: Thank you, Don.
Suggested Items
Silicon Mountain Contract Services Enhances SMT Capabilities with New HELLER Reflow Oven
07/17/2025 | Silicon Mountain Contract ServicesSilicon Mountain Contract Services, a leading provider of custom electronics manufacturing solutions, is proud to announce a significant upgrade to its SMT production capability with the addition of a HELLER 2043 MK5 10‑zone reflow oven to its Nampa facility.
Knocking Down the Bone Pile: Addressing End-of-life Component Solderability Issues, Part 4
07/16/2025 | Nash Bell -- Column: Knocking Down the Bone PileIn 1983, the Department of Defense identified that over 40% of military electronic system failures in the field were electrical, with approximately 50% attributed to poor solder connections. Investigations revealed that plated finishes, typically nickel or tin, were porous and non-intermetallic.
SHENMAO Strengthens Semiconductor Capabilities with Acquisition of PMTC
07/10/2025 | SHENMAOSHENMAO America, Inc. has announced the acquisition of Profound Material Technology Co., Ltd. (PMTC), a premier Taiwan-based manufacturer of high-performance solder balls for semiconductor packaging.
KYZEN to Highlight Understencil and PCB Cleaners at SMTA Querétaro Expo and Tech Forum
07/09/2025 | KYZEN'KYZEN, the global leader in innovative environmentally responsible cleaning chemistries, will exhibit at the SMTA Querétaro Expo & Tech Forum, scheduled to take place Thursday, July 24, at Centro de Congresos y Teatro Metropolitano de Querétaro.
Driving Innovation: Direct Imaging vs. Conventional Exposure
07/01/2025 | Simon Khesin -- Column: Driving InnovationMy first camera used Kodak film. I even experimented with developing photos in the bathroom, though I usually dropped the film off at a Kodak center and received the prints two weeks later, only to discover that some images were out of focus or poorly framed. Today, every smartphone contains a high-quality camera capable of producing stunning images instantly.