The Value Side of Training, Part 1: Five Easy Ways to Measure the ROI on Training
July 9, 2024 | Mike Hoyt, IPCEstimated reading time: 3 minutes
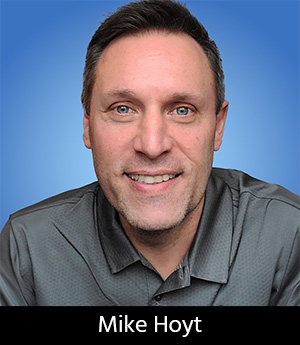
The best thing about a good investment is the yield it provides. This series of articles on the value side of training will focus on how to effectively measure the return on your investment (ROI) when training your staff. I will offer practical, quantifiable metrics you can apply today. Think of it as a quick checklist for every effective training program.
But before we jump into the ROI checklist, here are core principles to consider when it comes to training:
- Training is not a cost; it is an investment
- Not all training is created equal
- Training is not a one-time event
Training is not a cost; it is an investment
This should not be a surprise. For many of you, training is an easy no-brainer. But the opposite is also true, namely the painful results of not training. It’s easy to assume that training is expensive, but let’s not forget how costly and detrimental it is when you don’t invest in something valuable. We can easily quantify into dollars lost the effects of ignorance, poor quality, scrap, and attrition.
Not all training is created equal
It is easy to say, “We already invest in training,” or “That’s why we have a certified IPC trainer.” But let’s be realistic: There are good, bad, and in the middle training programs. Some effective training programs get new hires to proficiency 33% faster than others. While some are very engaging and interactive, others are not. Unfortunately, some training programs simply check the box. They may be outdated and become a negative experience for the learner.
With training programs, it’s important to consider how they perform and evaluate the results. I’m not suggesting changing an effective training program just for the sake of change, but inviting you to be open to new possibilities and better outcomes for the sake of improvement.
Training is not a one-time event
Growth and learning are ongoing processes. At age 88, inventor and artist Leonardo DaVinci said “Ancora imparo” or “I’m still learning.” We all need access to opportunities to personally improve and grow. Believe you can learn something new every day and then apply it to your job and training for all your employees, from entry-level to the C-suite.
In the next few months, I will share five articles on these ROI metrics that you can start using right away in your evaluation:
1. Time to proficiency: How long does it take a trainee to reach an industry-defined level of proficiency? Faster time to production equals more revenue generated and less time in training.
2. Minimal involvement of personnel: How much time do your brightest and smartest employees spend mentoring trainees? How much time are they away from their main responsibilities and from production? Unfortunately, that can hurt your bottom line more than you think.
3. Elimination of error: How much time, personnel, and money is spent on rework, repair, and scrap? How many dollars are lost on unsatisfied customers, especially if they are lost?
4. Mitigation of turnover: How many employees leave each year because training did not help them enough or there are no additional training opportunities for advancement. Think of the time, personnel, and resources that go into the rehiring process.
5. Training content is learned effectively: Using proven educational methods, we are measuring how much a person actually remembers from the training course and can apply to their job. An easy way to measure this is by looking at the quality of their work and whether the trainee had a positive learning experience.
I look forward to sharing more about each of these five areas and helping you build an effective training program that will pay for itself.
Mike Hoyt is the IPC workforce training advisor.
Testimonial
"We’re proud to call I-Connect007 a trusted partner. Their innovative approach and industry insight made our podcast collaboration a success by connecting us with the right audience and delivering real results."
Julia McCaffrey - NCAB GroupSuggested Items
Standard of Friendship: Debbie McDade and Symon Franklin Went From Classmates to Colleagues
08/27/2025 | Debbie McDade, Advanced Rework Technology Ltd.As a fairly new IPC Master Trainer, I nervously attended my first IPC committee meeting in 2002 in New Orleans—a 4,600-mile trip from my home in the UK—for the IPC-610 Task Group. With more than 250 members, it was the largest IPC committee at that time.
MS2 Technologies, LLC/P. Kay Focuses on Central America with First Installation in Honduras
08/24/2025 | P. Kay Metal, Inc.This year MS2 Technologies has turned their focused to the growing electronics market in Central America. With that focus came the adaptation of MS2 and the Akila System from a Honduras-based corporation with manufacturing plants in both Honduras and Mexico.
Meet with The Test Connection Inc. (TTCI) at SMTA Guadalajara 2025
08/18/2025 | The Test Connection Inc.The Test Connection Inc. (TTCI), a trusted provider of electronic test and manufacturing solutions for more than 45 years, is pleased to announce its participation at the upcoming SMTA Guadalajara Expo & Tech Forum, taking place September 17–18, 2025, at Expo Guadalajara, Salón Jalisco Hall D & E.
Creating Connections in Mexico
07/30/2025 | Michelle Te, Community MagazineA concerted effort by the Global Electronics Association—Mexico team over the past year has created inroads for the Global Electronics Association (formerly IPC) with leading electronics companies, government offices, and academic institutions in Mexico. “Our goal is to bring more awareness to what the Global Electronics Association is and what it offers,” says Lorena Villanueva, senior director. “We also aim to increase our membership. Of 3,200 members of the Global Electronics Association, only 180 are in Mexico.”
Confronting the Challenges of an Aging Workforce
07/15/2025 | Becky Calwell and Myriam Sullivan, Jobs for the FutureElectronics manufacturers have faced persistent workforce challenges as they struggle to find skilled workers to meet rising production demands, while rapid advancements in technology raise the bar for technical expertise. These ongoing issues highlight the need for innovative workforce strategies to address talent shortages and adapt to the industry’s evolving demands.