Audits: A Critical Element of Process Control
September 3, 2024 | Randy Cherry, IPCEstimated reading time: 1 minute
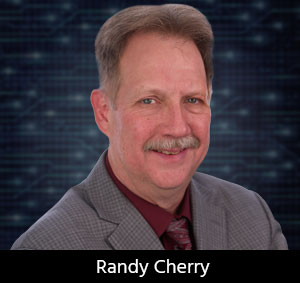
A formal audit always seems difficult to justify. Companies do not want the expense, and employees do not want the hassle. There is always a chance of failure, and management struggles to understand the benefits. If you or your company has had issues with auditing, hopefully, this article will help you feel a little more comfortable about the auditing process.
First, let’s discuss the internal process audit, which can help you avoid or eliminate many costly manufacturing problems, reduce scrap, increase yields, and directly improve your bottom line.
Process auditing can be simple and easy to maintain if you create a repeatable, impartial auditing process. Start with a Process Verification or Surveillance process audit. Create a basic yes/no checklist that covers each key manufacturing process within your facility. Another idea is to design a checklist covering all manufacturing processes from receiving to shipping and everything in between.
The Process Verification or Surveillance process audit is designed to be high-level. Unlike with a formal audit, objective evidence is not required. You are simply looking for gaps in the manufacturing process against your own internal procedures, standards, and work instructions. If your company operates by industry standards, add those to your checklist. It is best practice to perform Process Verification or Surveillance process audits once per quarter. As you collect and analyze data from the checklist, you can determine the most beneficial internal audit frequency moving forward. Let data drive the decision on audit frequency. Do not base it on opinions.
Going All the Way
Once you have determined your internal manufacturing processes and have met your goals for the Process Verification or Surveillance process audits, you may opt for the next step, which is to have a third-party auditor from an outside company perform a full manufacturing process audit to industry standards and your internal procedures and work instructions. The focus must be on the manufacturing processes, not your quality standards. Most companies have ISO certifications already in place that cover most quality concerns.
To read the entire article, which was originally published in the August 2024 issue of PCB007 Magazine, click here.
Testimonial
"Advertising in PCB007 Magazine has been a great way to showcase our bare board testers to the right audience. The I-Connect007 team makes the process smooth and professional. We’re proud to be featured in such a trusted publication."
Klaus Koziol - atgSuggested Items
The Art and Science of PCB Floor Planning: A Comprehensive Guide
08/14/2025 | Cory Grunwald and Jeff Reinhold, Monsoon SolutionsPCB design is an intricate and crucial part of developing electronic products. One of the foundational stages of PCB design is floor planning, a phase where the placement of components and the flow of signals are meticulously mapped out. A good floor plan ensures that the PCB performs well, is easy to manufacture, and meets all mechanical and electrical requirements. We’ll explore the essential aspects of floor planning, from its objectives and process to the challenges that designers face.
Advint and SanRex Expand High-Performance DC Rectifier Access for North American PCB Fabricators
08/12/2025 | Advint IncorporatedAdvint Incorporated has entered a strategic partnership with SanRex Corporation, enhancing access to industrial-grade DC rectifiers for the US printed circuit board industry. With a legacy of power innovation and performance across the globe, SanRex rectifiers are available through Advint’s proficient distribution network.
Advint and Sayron Bring Advanced Rectifier Solutions to High-Reliability PCB Manufacturers
08/01/2025 | Advint IncorporatedAdvint Incorporated has partnered with Sayron, a leading global rectifier manufacturer, to supply cutting-edge IGBT-based DC rectifiers to high-performance PCB manufacturers across North America and beyond. Sayron’s precision-engineered rectifiers align with the stringent requirements of advanced PCB processes.
Trouble in Your Tank: Metallizing Flexible Circuit Materials—Mitigating Deposit Stress
08/04/2025 | Michael Carano -- Column: Trouble in Your TankMetallizing materials, such as polyimide used for flexible circuitry and high-reliability multilayer printed wiring boards, provide a significant challenge for process engineers. Conventional electroless copper systems often require pre-treatments with hazardous chemicals or have a small process window to achieve uniform coverage without blistering. It all boils down to enhancing the adhesion of the thin film of electroless copper to these smooth surfaces.
Magnalytix’s Dr. Mike Bixenman to Guide PDC at SMTA High-Reliability Cleaning and Conformal Coating Conference
07/31/2025 | MAGNALYTIXMagnalytix, providing real-time reliability solutions for electronics manufacturing, is excited to announce that Dr. Mike Bixenman will present the professional development course “The Effects of Flux Residues and Process Contamination on the Reliability of the Electronic Assembly” on Wednesday, Aug. 13 at 9:00 AM CST to open the second day of the STMA High-Reliability Cleaning and Conformal Coating Conference.