Estimated reading time: 2 minutes
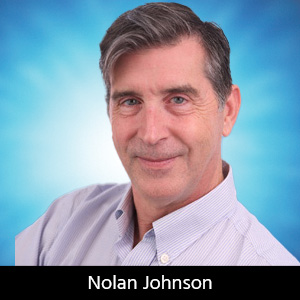
Solder Printing: A 1:1 Ratio of Technical and Creative
When things get technical, I’m in my happy place. It’s why I work in technology in the first place. I also happen to enjoy creative pursuits, and my real happy place is when both creative and technical happen at the same time. Over the years, it seems that most of us engaged in printed circuit design and manufacture are similarly wired. I don’t think I’m alone in stating that finding a creative solution to a technical problem is one of the highlights of our workday. We get bonus points if the solution is particularly simple or uncomplicated.
Technological innovation is creative problem-solving at its very core. Straight-up-and-down engineering logic and thinking that turns everything into a flowchart collaborate with creativity’s leaping, intuitive, lateral thinking. For me, that’s when the magic occurs. Some call it serendipity, which can emerge from some of the most mundane parts of our everyday experiences.
One ubiquitous component in PCB assembly is solder paste. It’s what makes assembly happen. We can’t attach components without solder, and solder paste is a requirement for surface-mount components. It hardly seems like there’s much room for innovation in something so common and basic.
But they probably thought the same thing in 1968, when a 3M researcher named Spencer Silver, who was trying to create a strong adhesive for use in aerospace, inadvertently created an adhesive that “stuck lightly to surfaces but didn’t bond tightly to them.” Meanwhile, Silver’s colleague, Art Fry, was frustrated that the paper scrap bookmarks he used to mark passages would often fall out. Fry put his problem-looking-for-a-solution and Silver’s solution-looking-for-a-problem together, and Post-It Notes™ was the result.
Truthfully, quite a lot happens when creating and applying solder paste. As components get smaller, the grit of the solder needs to get finer. Likewise, as BGAs and the like get larger, the solder ball gets smaller to make room for more contact points, requiring smaller solder grit. Even when our components get larger, the solder still gets finer. Where it gets complex, though, is that these divergent parts increasingly require different thicknesses of solder paste to bond properly. For stencils, this can be a particular challenge.
Meanwhile, solder print technologies—primarily dispensing and jetting—are gaining acceptance. The tried-and-true method of solder stencils still works, of course. But printhead-based alternatives have made strides. If you’ve not looked at these pieces of equipment before, now might be the time to do so. It’s not lost to me that legend printing, solder mask jet printing, and solder paste printing are all technologies simultaneously on the rise.
But changing solder paste, or solder paste application, can cause cascading changes down the line. Changes in the flux formulation can require changes in cleaning, reflow, and virtually everything.
So, for the September 2024 issue of SMT007 Magazine, we get down to the nitty-gritty of solder paste. Ron Lasky and Adam Murling kick open the door with a discussion on current solder trends for printing, and Mike Konrad and Tony Lentz follow right behind with an overview of the technologies. Wolfgang Heinecke of Mycronic gets into the details of jetting, and Sunny Agarwal of Camalot Dispensers does the same for dispensing, and our newest contributor, Josh Casper, debuts this month with equipment insights.
This column appears in the September 2024 issue of SMT007 Magazine.
More Columns from Nolan's Notes
Nolan’s Notes: Finding Your Sweet SpotNolan’s Notes: Moving Forward With Confidence
Nolan's Notes: The Next Killer App in Component Manufacturing
Nolan’s Notes: Looking Deep Into the Future With X-ray
Nolan’s Notes: Your Golden Ticket
Nolan's Notes: Find the Help You Need—Accessing Technical Resources
Nolan’s Notes: Emerging Trends in 2025
Nolan’s Notes: Soldering Technologies