Estimated reading time: 4 minutes
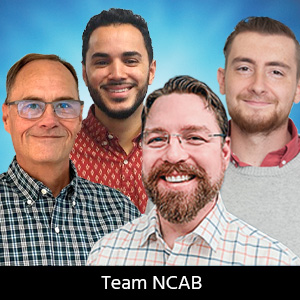
Fresh PCB Concepts: The Journey of a PCB—A Tale of Sustainability and Circularity
Imagine a bustling factory floor where hundreds of PCBs hum with potential, each one destined to be the brain of a new electronic device. From the sleek smartphone in your pocket to the intricate systems in electric vehicles, PCBs are the unsung heroes of our digital world. But have you ever wondered what happens to these tiny powerhouses when their work is done? The journey of a PCB doesn’t end when a device reaches the end of its life. In fact, that’s where the next chapter begins—a chapter that’s critical for our environment and our future.
Globally, we generate over 50 million metric tons of electronic waste (e-waste) each year. PCBs, central to virtually all electronics, contribute significantly to this massive waste stream. Without proper disposal and recycling, the toxic materials in PCBs, like lead and mercury, can leach into the environment, contaminating soil and water. On the other hand, these boards are rich in precious metals like gold, silver, and copper, which can be reclaimed and reused. Effective recycling reduces the need for mining, conserves natural resources, and lessens the environmental impact of electronics.
When compared to Europe and other parts of the world, the U.S. places less emphasis on sustainability and recycling. The capitalistic environment often hinders the growth of recycling industries, as profitability remains a challenge. As a result, only a few companies operate in this space domestically, with most of the refining processes being outsourced overseas. Due to the intricate design and diverse materials used in their construction, recycling PCBs is a complex process.
Most companies begin by accumulating massive quantities of PCBs and other electronic waste, often in the tens to hundreds of tons. Electronic waste is typically kept in its original assemblies, as disassembling components and boards would be excessively labor-intensive. The initial step in the recycling process is usually mechanical, where the waste is shredded into small pieces roughly the size of quarters. This is sometimes followed by physical separation techniques, such as sieving, magnetic separation, and eddy current separation, to extract metals and other valuable materials. While this method is effective in recovering metals like copper and aluminum, it often yields materials of lower purity.
Most metal refining takes place overseas. Among the most effective methods for recovering a high percentage of valuable metals is pyrometallurgical processing. In this technique, PCBs are incinerated at high temperatures, enabling the extraction of precious metals. However, this process is energy-intensive and can produce harmful emissions if not properly managed. Another widely used method is hydrometallurgical processing, which involves using acids and solvents to leach metals from the PCBs. While this method yields metals of high purity, it also poses environmental and health risks due to the hazardous chemicals involved. Lastly, electrochemical recycling is an emerging technique that uses electricity to dissolve metals from PCBs, allowing for their recovery with minimal environmental impact. Although still in its early stages, this method holds promise for more sustainable PCB recycling.
Recycling is crucial, but considering the entire lifecycle of PCBs is essential. Circularity in PCB manufacturing, which focuses on designing products with their end-of-life in mind, ensures components can be easily disassembled, recycled, or repurposed. This reduces e-waste, conserves resources, and keeps valuable materials in circulation. Modular designs allow for component upgrades without discarding entire devices, extending electronics' lifespan and reducing raw material demand. Additionally, exploring biodegradable materials in PCB production enhances sustainability.
At NCAB, we collaborate with material manufacturers like Jiva, Papermill, and Shegyi to develop biodegradable materials and reduce material usage. We've advocated for reducing the standard FR-4 and copper thickness when possible, which decreases waste, conserves water and energy, and lowers CO2e emissions. We're also working with manufacturers on cutting-edge additive manufacturing technologies, including fully additive FPCs in Japan and Austria, to further minimize raw material usage and improve resource efficiency. Lastly, NCAB Group is cooperating with IMEC on lifecycle assessment of PCB production to establish better standards for consistent and reliable data collection and reporting.
Recycling and circularity in PCBs offer benefits beyond environmental protection. According to the United Nations University, up to 95% of precious metals in PCBs can be recovered, reducing the need for environmentally harmful mining, and providing a steady supply of critical materials for the electronics industry. As global demand for electronics rises, so does the pressure on natural resources. Embracing recycling and circularity helps alleviate this pressure, lowers the carbon footprint of devices, and fosters a more sustainable future.
The journey of a PCB, from its creation to its eventual recycling, is a story of innovation and responsibility. As consumers and industry players, we have a role to play in ensuring that this journey is as sustainable as possible. By partnering with suppliers who prioritize sustainability in everything they do, like we do at NCAB Group, and collaborating with our engineers to design products with circularity in mind, we can turn the tide on e-waste and pave the way for a greener, more sustainable future. In the end, every discarded PCB has the potential to be reborn, to power the next generation of devices, and to contribute to a world where technology and sustainability go hand in hand.
Ramon Roche is a field application engineer for NCAB Group.
More Columns from Fresh PCB Concepts
Fresh PCB Concepts: Assembly Challenges with Micro Components and Standard Solder Mask PracticesFresh PCB Concepts: The Power of a Lunch & Learn for PCB Professionals
Fresh PCB Concepts: Key Considerations for Reliability, Performance, and Compliance in PCBs
Fresh PCB Concepts: Traceability in PCB Design
Fresh PCB Concepts: Tariffs and the Importance of a Diverse Supply Chain
Fresh PCB Concepts: PCB Stackup Strategies—Minimizing Crosstalk and EMI for Signal Integrity
Fresh PCB Concepts: PCB Plating Process Overview
Fresh PCB Concepts: PCB Design Essentials for Electric Vehicle Charging