The SD11 Inkjet Printer and Ventec Giga Solutions
October 10, 2024 | Marcy LaRont, PCB007 MagazineEstimated reading time: 8 minutes
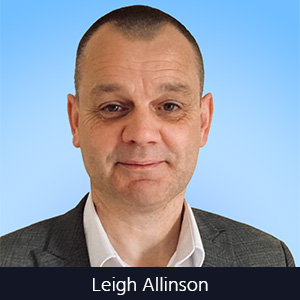
Ventec expanded last year to provide greater portfolio solutions to its customers, all of which are aligned with Ventec’s core business in laminates and distribution products. I sat down with Ventec Giga Solutions’ Commercial Director Leigh Allinson, who is deeply rooted in both the PCB and supply chain sectors. He explores the innovative realms of the company and its cutting-edge SD11 inkjet printer. Leigh brings insight into the fabric of the electronics manufacturing industry through the lens of pushing technology limits and delving into the strategic expansions of Ventec Giga Solutions.
Marcy LaRont: Leigh, tell me a little bit about your background and experience.
Leigh Allinson: I started in PCBs at the age of 15, qualifying through day-release courses. I got my UK Higher National Certificate and diploma in chemistry through Exception PCB, followed by a certificate and diploma in management studies, again on day release and night school. In 2007, I joined MacDermid where I worked for 12 years, then joined Ventec in 2020. I have about 16 years of experience making PCBs and approximately 17 years in the supply chain. I was very much hands-on at the customer site, especially with MacDermid. If a customer had a problem, I was always happy to roll my sleeves up. It is the same with Ventec and Ventec Giga Solutions.
LaRont: It’s valuable for a salesperson to have the perspective of both sides. Tell me about this new venture of Ventec Giga Solutions.
Allinson: We launched Ventec Giga Solutions in June 2023. When you think of Ventec, you think of laminates and distribution products. The natural way to gain more exposure in the market is to have another division that complements your core business. So, we now have an equipment company, Ventec Giga Solutions.
LaRont: What are the machine lines you currently provide?
Allinson: We started with lamination press plates with Cardel. More recently, we announced distribution agreements with HiPrint inkjet printers for applications such as solder mask and legend printing, and the Sunus portfolio of machines for vacuum filling of through-holes and blind vias.
LaRont: You provide a full spectrum of solutions around your part of the manufacturing process. Tell me about the Hi-Print SD 11 inkjet printer.
Allinson: We released SD11 several weeks ago. We believe it fills a gap in the market. Inkjet technology has been around for years, but mainly for legend printing rather than full solder mask. The capability of this machine is for full solder mask coverage with tighter tolerances, smaller dams, and higher accuracy. We didn't want to bring a “me too” machine to the market. We saw an opportunity to create something unique that offers a bit more to the inkjet process. The SD11 machine has 10 print heads with the ability to program using three different colors of solder mask and/or legend.
LaRont: That's a lot of printheads.
Allinson: It is, but having 10 heads gives you that flexibility. You may want to configure the machine primarily for production, so you may have all your greens going through six heads and have the other set up for two different colors. You can set it up for three different colors, or a green with a legend as well.
LaRont: You can have the solder mask and legend set up at the same time on the same machine without having to change or adjust anything?
Allinson: Yes. You just configure them how you wish, which is all programmable. You tap it on the touch screen, and it does it all for you.
LaRont: What about the maintenance of your 10 printheads? Is this a smart machine with a self-maintenance capability?
Allinson: The SD11 has an integrated print head maintenance system that continually cycles the ink or automatically purges it so that the print heads don't get blocked. One critical issue with inkjets is that you can’t let the print heads dry out. It will damage them.
LaRont: Can you list the benefits of this type of technology, in terms of the technology that it can create, and the environmental sustainability benefits?
Allinson: There are many benefits to moving away from traditional screen-printed inks or LDI-based machines (laser direct imaging). Generally, there is significantly less wastage. Traditionally with a solder mask, you screen print it all over your board and then wash it back off. With an inkjet, you put the ink exactly where you want it, so no extra ink is wasted and nothing needs to be removed. Also, by having a single machine, you're able to eliminate other parts of the process. You can remove the developer and reduce your chemical costs and water usage. You now have a machine you don’t have to pay to maintain. That’s a big deal when talking about environmental sustainability goals, and general business and manufacturing costs. Most significantly, this technology allows for the solder mask printing of very fine features, with improvement in both quality and consistency, which translates to yields and, ultimately, profitability.
LaRont: How fine of features are we talking about?
Allinson: Some of the initial tests with our solder mask partners have achieved 50-micron dams. In the past, it has been difficult for inkjets to achieve less than 75 micron. However, there are now greater demands for PCB board designs to have smaller features with more functionality, so it has become important to achieve those 50-micron dams.
LaRont: What about machine footprint? Space is a significant challenge for many fabricators, at least in the U.S. and the UK. You are getting rid of at least one machine, but how big is the SD11?
Allinson: The machine measures 2.5 x 1.9 x 2.1 meters and consolidates more or less the entire process on this one platform, so the overall footprint is a great deal smaller. By our calculations, a fabricator could go from 3,000 square feet to 300, so the entire process could take place in a part of the factory that previously may have been unsuitable. You get more freedom to optimize the end-to-end production flow across the factory floor. This machine was designed with that in mind. It also uses Fuji heads, so reliability, repeatability, and pin-sharp coating accuracy are assured. The maximum print area of 24 x 30 inches can handle a wide panel-size range, and it works with panel thicknesses starting from 5 millimeters.
LaRont: Is this designed specifically for a particular global market?
Allinson: This machine is suited to high-mix, low-volume work. Think about the amount of production time saved by not having to make additional artwork and constantly change your setups on machines to accommodate different jobs. The machine will put in your panel program and product identification. It doesn't necessarily mean that you reduce your labor in the factory, it just means that you can use that labor in other areas. You now have better resource utilization of your highly trained workers. So, it's about maximizing your resources to keep overall costs down. You have more control and consistency in your process.
LaRont: Yes, the easy programmability and flexible control are known advantages of digital inkjet printing. But there are other criteria in mind, such as raw throughput. How do you see this technology handling demands for larger quantities?
Allinson: The SD11 can hold its own in the mid-volume marketplace too. With 10 heads, you can take advantage of the flexibility to set up, say, six heads for green solder mask and then run lower-volume jobs on the remaining four heads.
LaRont: What has the reception been for this machine and technology?
Allinson: When we launched, the general feedback was that inkjet wasn't quite where it needed to be. Today, that view has changed noticeably, and a greater proportion of the companies we are talking to see that the technology can meet their demands. I can see that the effort we have put into preparing the market will soon begin delivering rewards.
LaRont: When you're speaking with customers about this as a potential solution, do you have an ROI calculation?
Allinson: I'm working with the ink suppliers to develop a solid formula for ROI. There are several factors to consider in the calculations, including the overall cost savings on labor, energy, water, etc. Moving to this technology is about value—increased flexibility, space savings, the aesthetic quality of inkjet—rather than cost. We are doing our best to educate our customers and the market about that.
LaRont: What is Ventec Giga Solution’s tech service model, installation support, and beyond?
Allinson: As said, we launched Ventec Giga Solutions in June 2023. A big part of our culture is providing a superior level of after-sales support; we’re not simply about selling machines. Marc Ladle recently joined us to head up our after-sales team. He’s a well-known, experienced engineer with a significant amount of PCB knowledge and I’m excited to see how he will strengthen our service portfolio. This sort of equipment generally has a PLC control with a direct link to Ventec for support. You plug it into a modem, and we can help diagnose the machine remotely. Something that differentiates Ventec from some of its competitors is that we have application support as well. We can help our customers with the specific products they are trying to build based on their end markets. That is where Marc’s PCB experience and the PCB expertise of his engineering staff are key, and a tremendous value add for our customers. It's about that total package.
LaRont: If one of your customers is working on NPI they can call you up and say, “This is what we're trying to do. Can you help us optimize the process to achieve X?”
Allinson: Yes, and we have the expertise in house to respond to those sorts of requests for any product we sell. This is a key differentiator for Ventec Giga and reflects our commitment to partner with companies that are developing disruptive and cutting-edge technologies and to build up appropriate support capabilities in-house. We aim to offer comparable customer support for every product in our portfolio.
LaRont: Tell me about Hi-Print, your partner on the SD11.
Allinson: Hi-Print was established in 2009, and the company has quickly built up a roster of great OEM customer references. We are happy to partner with a supplier of their caliber.
LaRont: What about the qualified ink suppliers?
Allinson: Currently, the machines are qualified with Electra and Taiyo inks, and we are in discussions with Peters. The machine has been tested with those inks. But feasibly, other manufactured inks can be used. This technology is not unique to any one ink supplier.
LaRont: Leigh, this has been an interesting conversation. Thank you.
Allinson: My pleasure, Marcy.
Suggested Items
Smarter Machines Use AOI to Transform PCB Inspections
06/30/2025 | Marcy LaRont, PCB007 MagazineAs automated optical inspection (AOI) evolves from traditional end-of-process inspections to proactive, in-line solutions, the integration of AI and machine learning is revolutionizing defect reduction and enhancing yields, marking a pivotal shift in how quality is managed in manufacturing.
Technica USA Announces New Strategic Partnership with I.T.C. Intercircuit Production GmbH
06/24/2025 | Technica USATechnica USA is pleased to announce a new distribution and representative agreement with I.T.C. Intercircuit Production GmbH, a globally recognized manufacturer of advanced equipment for the PCB manufacturing industry.
Smart Automation: The Power of Data Integration in Electronics Manufacturing
06/24/2025 | Josh Casper -- Column: Smart AutomationAs EMS companies adopt automation, machine data collection and integration are among the biggest challenges. It’s now commonplace for equipment to collect and output vast amounts of data, sometimes more than a manufacturer knows what to do with. While many OEM equipment vendors offer full-line solutions, most EMS companies still take a vendor-agnostic approach, selecting the equipment companies that best serve their needs rather than a single-vendor solution.
Sierra Circuits Boosts High Precision PCB Manufacturing with Schmoll Technology
06/16/2025 | Schmoll MaschinenSierra Circuits has seen increased success in production of multilayer HDI boards and high-speed signal architectures through the integration of a range of Schmoll Maschinen systems. The company’s current setup includes four MXY-6 drilling machines, two LM2 routing models, and a semi-automatic Optiflex II innerlayer punch.
MVTec, Siemens Expand Technological Cooperation
06/12/2025 | MVTecMVTec Software GmbH and Siemens are expanding their technological cooperation in the field of industrial automation. To reinforce their increasingly close collaboration, Siemens joined the MVTec Technology Partner Program in May 2025.